旋盤による切削加工を安定させる工具 シングルローラ・スパロール
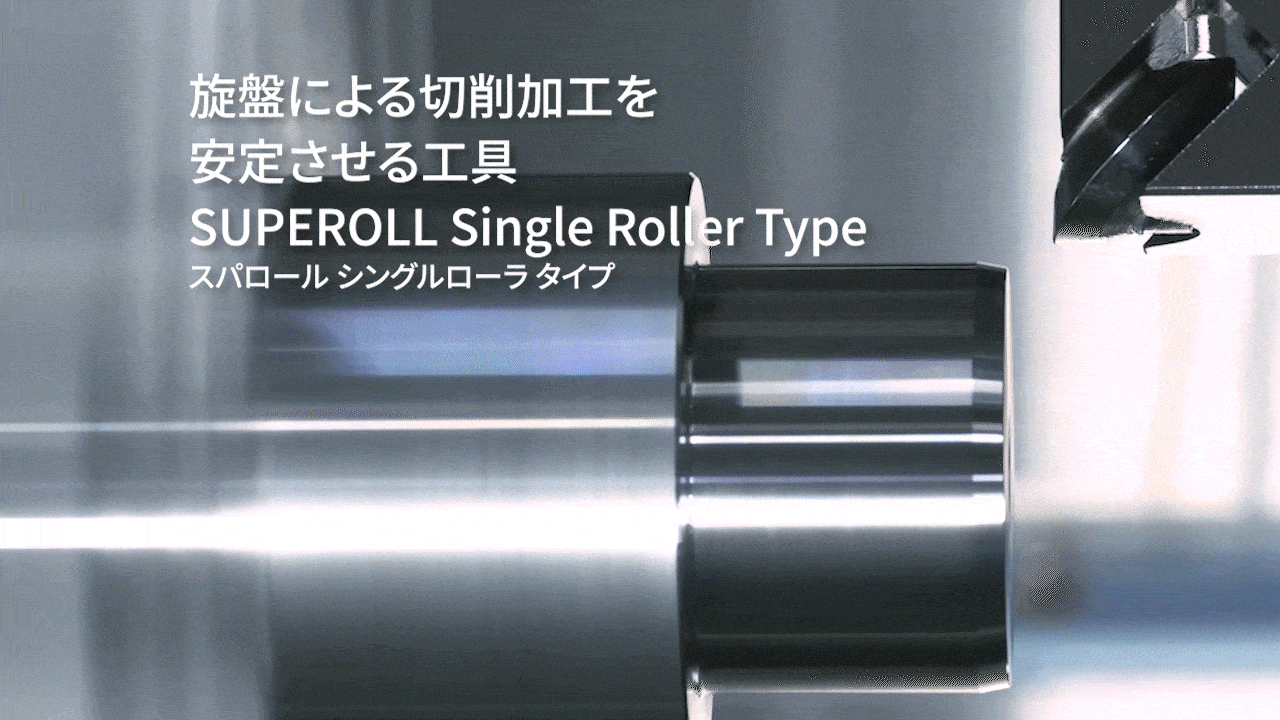
旋盤加工で、こんなお悩みはありませんか?
- 表面粗さが安定しない。
- 切削チップの寿命が短い。
- 研磨をなくして工程集約したい。
このページでは、旋盤による切削加工を安定させる方法を、表面粗さが理想通りにならない要因とあわせて解説します。
表面粗さとは?
「表面粗さ」とは、物体の表面にある幾何学的で微細な凹凸のことです。旋削加工では、切削チップの先端形状が転写され形成される山谷の高さを指します。
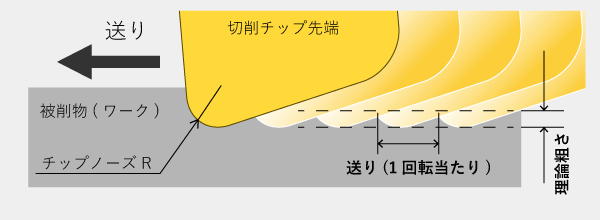
表面粗さ【Rz】理論値の求め方
表面粗さ【Rz】理論値は、次の計算式で求められます。

表面粗さの計算式
空欄に数値を入力すると、理論値が表示されます。
つまり、理論値に合わせた加工条件で、目標の表面粗さを出せるはずです。
ですが、実際の生産現場で、理論値通りの表面粗さになりますか?
理論値通りの表面粗さにならない理由
理由1 構成刃先で表面粗さが悪化する
加工条件が適切でないと切削チップの先端に構成刃先が発生し、加工面が均一な形状にならず、理論形状から乖離します。
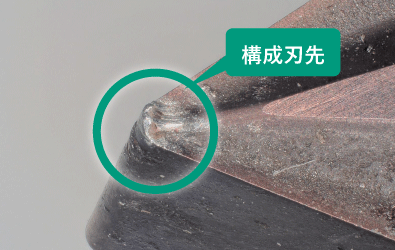
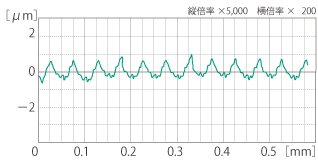
送り速度を下げると表面粗さは小さくなりますが、送り速度が遅ければ遅い程、凝着(ぎょうちゃく)が発生しやすくなるため、高速回転で加工しなければなりません。
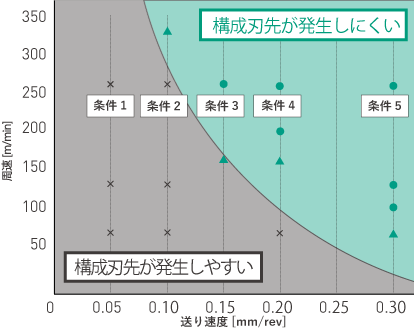
加工条件
ワーク : φ30 SCM440
切削チップ: 超硬 ノーズR0.4
クーラント: 未使用
周速 : 50~250 m/min
送り : 0.05~0.3mm/rev
切込量 : 0.4mm ※一定
条件1~5の表面粗さグラフ
周速250mm/minで、送り速度のみ変えた場合の粗さ理論値と実際の値について
条件1【F=0.05mm/rev】
理論値 Rz0.8μm
実際Rz1.476μm(1.85倍)
凝着あり
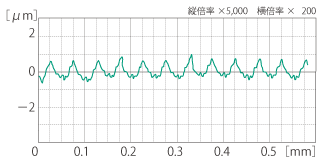
条件2【F=0.1mm/rev】
理論値 Rz3.2μm
実際Rz3.548μm(1.1倍)
凝着あり
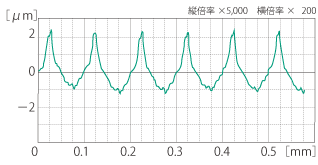
条件3【F=0.15mm/rev】
理論値 Rz7.0μm
実際Rz7.215μm(1.0倍)
凝着なし
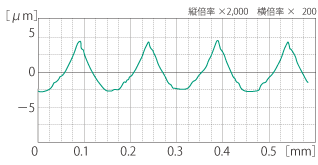
条件4【F=0.2mm/rev】
理論値 Rz12.5μm
実際Rz12.837μm(1.0倍)
凝着なし
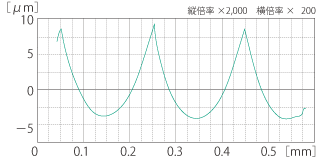
条件5【F=0.3mm/rev】
理論値 Rz28.1μm
実際Rz29.458μm(1.0倍)
凝着なし
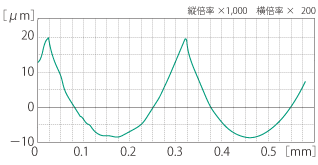
例えば、上記条件においてRz3.2を狙う際、理論値から算出すると送り速度0.1mm/revが妥当ですが、その時に必要な周速は350mm/min(3,714rpm)となります。
理由2 切削工具の摩耗
切削工具の摩耗により、表面粗さは次第に悪化します。
Rz3.2を量産で狙う場合、次第に悪化することを想定すると、送り速度0.07mm/revが妥当となり、対応する周速は450mm/min(4,775rpm)となります。
ところが、切削速度(周速)を上げると、切削温度上昇により工具寿命が著しく低下します。
また、送り速度を下げると逃げ面摩耗が大きくなり工具寿命の低下につながります。
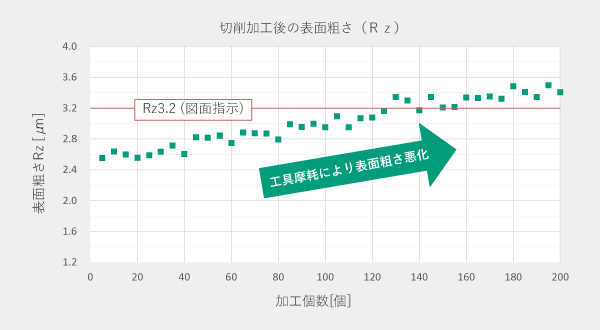
まとめ
表面粗さを安定させるためには、「送り速度を落とす」か「切削速度を上げる」必要がありますが、これらは工具寿命悪化の原因となります。
工具寿命が悪化すると、寸法精度が不安定になります。つまり、「表面粗さ安定」と「寸法精度の安定」は相反します。
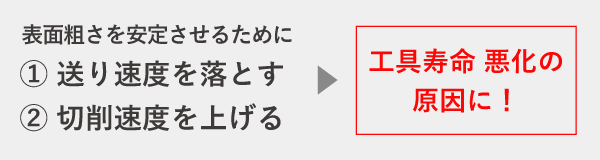
スパロールを活用した解決方法
スパロールとは
ローラで金属表面を押し均して、なめらかに仕上げる工具です。
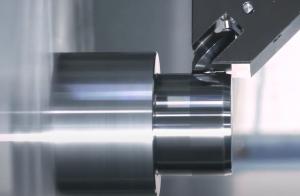
「粗加工」+「寸法仕上げ」+「表面仕上げ」で粗さと寸法を両立させる
加工を「粗加工」+「寸法仕上げ」+「表面仕上げ(スパロール)」の3つの工程に分けることで、それぞれ最適な条件に設定でき、寸法精度と粗さ精度の安定を実現します。
従来の工法
切削チップのみ
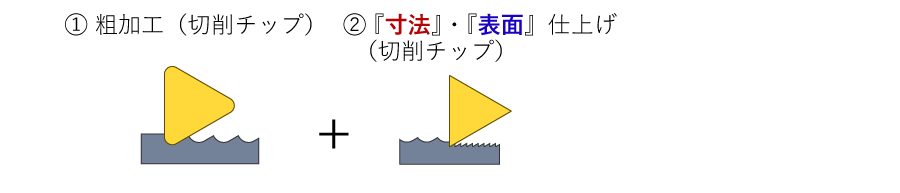
表面仕上げのみ研磨(別工程)
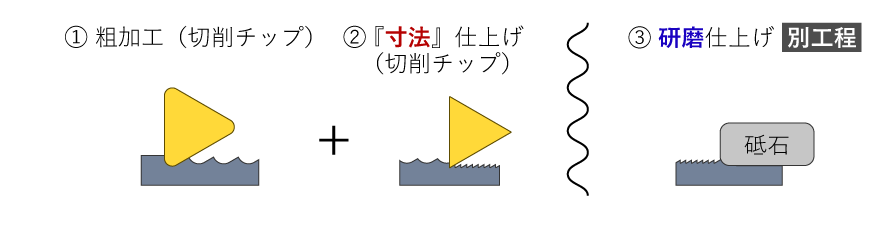
ご提案する工法
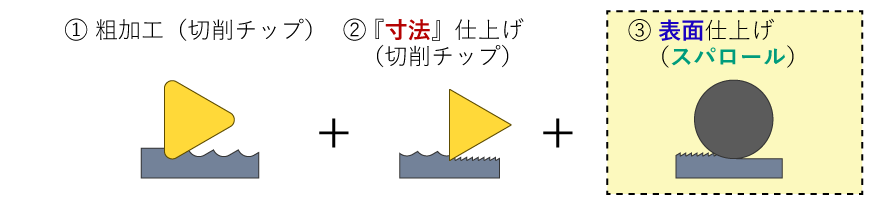
切削工具で寸法精度を維持し、スパロール加工で表面粗さを確保する。
これで、旋盤のみで目的の寸法精度と表面粗さを達成することができます。
よくある質問
Q
ツールポストへの取り付け方法は?
切削バイトを取り付けるホルダに装着できます。タレットに1つ空きがあることをご確認ください。
Q
切削加工とは違いますか?
バニシング加工(塑性加工)と呼ばれる工法で、削りではありません。切削の山谷の「山」を押し潰すことで、「谷」が隆起し表面を平滑に仕上げます。
Q
押し込み量(取り代)はどれぐらいですか?
ツールによって違いはありますが、0.4mm程度(径)押し込みます。ワークに力が伝わるように、内部に伸縮する機構があるので、ローラはワークに食い込みません。
Q
加工後の径の変化量は?
ワークの材質や肉厚にもよりますが、数ミクロン程度です。寸法をある程度仕上げたのち、スパロール加工をおすすめします。
Q
加工可能な材質は?
次のとおりです。
加工可能な材質: 鉄系・非鉄金属。アルミ、SUS、SCM、S45C、FC、ADC、真鍮 など
加工不可能な材質:純チタン、マグネシウム、木材、ガラス、セラミック、プラスチック など
旋盤加工でお困りではありませんか?
スギノマシンでは、ローラ・バニシングツール「スパロール」をご提供しています。開発企業ならではのノウハウにより、表面粗さの仕上げ加工をお手伝いいたします。
無料のツール貸し出しサービスも行っています。技術サポート付きのため、借りたものの上手く使えない、時間ばかりかかる…といったご心配にもお応えします。どうぞお気軽にお問い合わせください。