部品洗浄とは
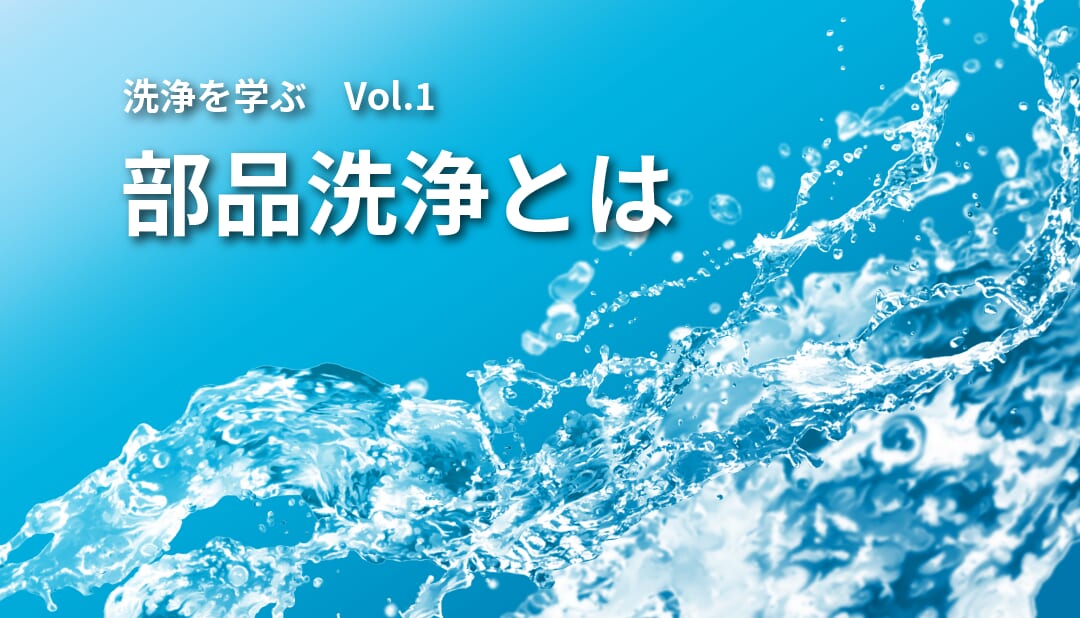
1. 部品洗浄とは
部品洗浄とは、”対象物に付着した汚れや不要なもの”を、界面活性剤の化学的作用や、噴流などの物理的な作用で除去し、製品の使用に支障が出ない程度まで低減することを指します。
機械を構成する部品は、機械加工やプレス加工、溶接、研磨、表面処理など、様々な製造工程を経て製作されています。各工程の前後では、加工油、切粉、粉じん、スケールなどを除去するために部品洗浄を行い、機能面から考えられた要求品質である”清浄度”を達成します。
また、製品に付着した不純物のことを「コンタミネーション」、略して「コンタミ」と呼びます。このコンタミを除去することが、部品洗浄の主目的です。
自動車を例に挙げると、かつて新車を購入した際は「慣らし運転」が必要とされ、1,000km程走行した後はオイル交換が求められました。これは製造時に部品に残留したバリや切粉などの異物が、使用とともに機械内部に流出するため、運転初期に排出することが目的でした。流出した異物は減速機・ギアなどの駆動部や制御用の油圧回路などに噛みこみ、早期摩耗や不具合を引き起こすため、オイル交換を行うことで未然に防いでいました。
近年では、このような慣らし運転やオイル交換はあまり必要とされていません。これは洗浄技術が向上し、部品に残留する異物が大幅に減少したことが要因の一つです。
このように、機械製造において洗浄工程は重要な役割を担っており、現代のものづくりには無くてはならないものとなっています。
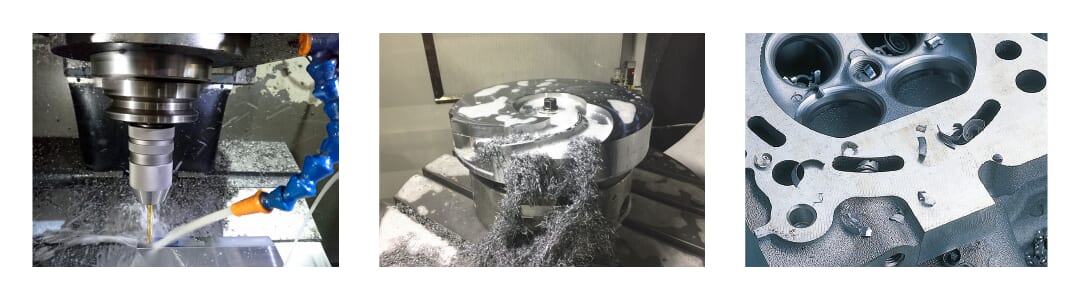
2. 部品洗浄機の種類
部品加工現場で使われる洗浄機は、以下のように分類されます。
(1) 超音波洗浄機
超音波洗浄機は、街中の眼鏡店の店頭などで見かけることがありますが、それと同じ原理です。超音波を液体中で照射すると、音圧の振動によりキャビテーション(気泡)が発生します。その気泡が崩壊するときの衝撃力を利用して、部品表面から汚れを除去します。
超音波洗浄は部品形状を選ばないため、複数のワークを同時に洗浄することに適しており、バッチ処理に多く使われます。メッシュ状のバスケット・カゴに部品を入れて、一度に大量に洗浄します。製造現場では、粗洗浄・リンス洗浄・乾燥と、一連の工程を順に行う自動機もよく使用されています。
超音波洗浄では溶剤系の洗浄液を用いるケースが多く、化学反応を併用します。炭化水素系洗浄剤は、炭素と水素から構成された化学物質で、油と同じ成分でできているため油分を溶かしやすく、油汚れの洗浄に適しています。しかし、炭化水素系洗浄剤は可燃性であることが懸念点として挙げられます。室温よりも引火点が高いものは常温で引火することはありませんが、万が一に備え防爆などの対策が必要です。また、消防法により取扱量が制限されているため、導入時に検討が必要です。
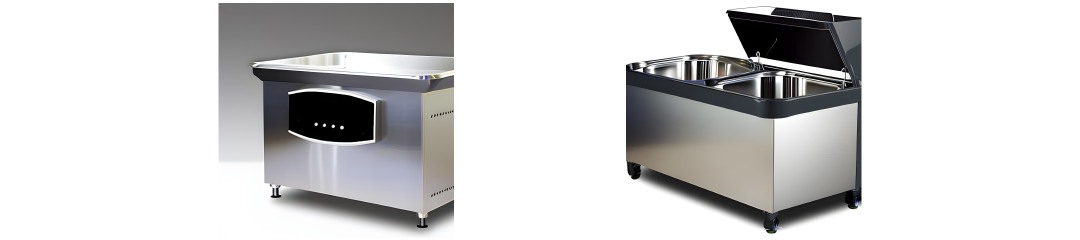
(2) 噴射洗浄機(シャワー洗浄機/高圧ジェット洗浄機)
私たちが日常使っているお風呂のシャワーをイメージするとわかりやすいでしょう。低圧シャワー洗浄機(0.2~2MPa)や、高圧ジェット洗浄機(2~100MPa)があります。ポンプにより加圧された水をノズルから噴射し、部品に当てて洗浄します。洗浄圧力が高いほど噴射速度が速くなり、流体の持つ運動エネルギーも大きくなります。
外観に付着している切りくずや油分を洗い流すには、低圧のシャワー洗浄機が適しています。より高清浄度が求められる場合は、付着力の高い頑固な汚れや、タップ穴に引っかかった切りくずなどを除去できる高圧ジェット洗浄機が使用されます。圧力が20MPaを超えると、洗浄と同時にバリも除去できるようになります。使用される洗浄液は水系洗浄剤が多く使われていますが、水をそのまま使うケースもあります。高圧ジェット洗浄は、塗装面の剥離や建物のアスベスト除去にも用いられています。
噴射洗浄はノズルの配置により水の当たる位置が決まるため、設計時に十分な検討が必要です。ノズルの位置を任意に決められるように、ノズルを移動装置でプログラム移動させるNC洗浄機も広く用いられています。
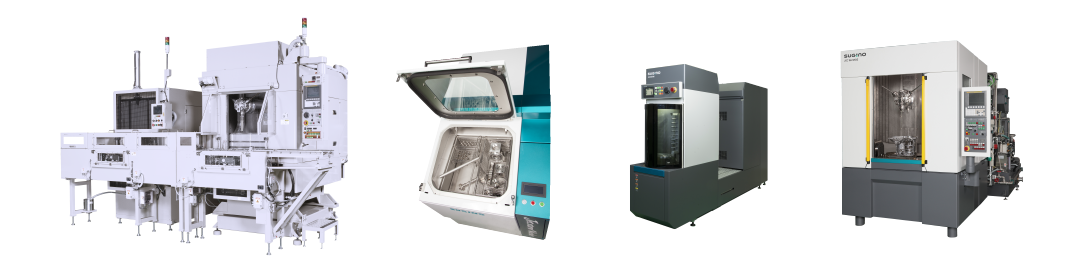
3. 洗浄不良が引き起こすトラブル
(1) 製品性能・安全性への悪影響
もし、私たちが日頃使用している自動車のエンジンに異物が入っていたら故障の原因や事故の原因になることは容易に想像できます。産業機械においても同じで、LMガイドなどの直動部品、減速機などの駆動装置内部に残留する異物は、装置の誤動作や短寿命の原因となり、本来持っている性能が発揮できなくなります。これを防ぐために、洗浄技術が重要です。
装置を構成する部品の製造工程では機械加工が行われ、加工油が使用されます。加工で発生する切りくず(切粉)は、加工油が接着剤のように働き、細かなスラッジと共に加工部品に付着します。この汚れは非常に強固で、表面だけでなく部品の奥深くにも流れ込んで付着しています。後工程の洗浄が不十分で汚れが残ってしまうと、駆動機械の内部やガイド機構の摺動部品の摩耗を促進し、機械寿命に悪影響を与えます。
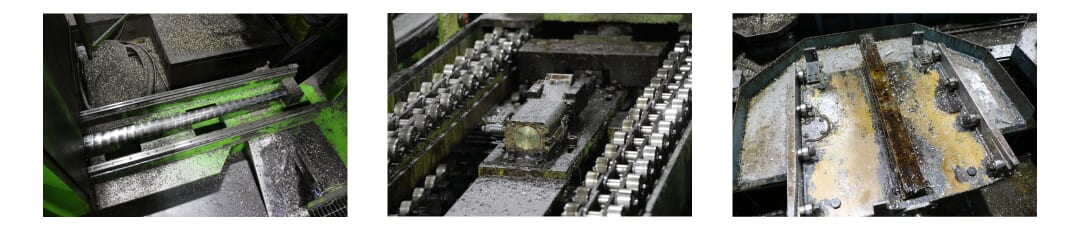
(2) 後工程への不良品流出
残留したバリや異物は、部品の組付けの際に障害となります。特に嵌合部品に与える影響は大きく、正しく組付けできないだけでなく、部品に傷がついて不良品発生の原因になります。不良品がそのまま市場に流れれば、コンプライアンスの問題に発展する可能性もあります。
後工程や部品を使用する次の作業者、最終製品のことを考えると、清浄な部品の必要性がよく分かります。
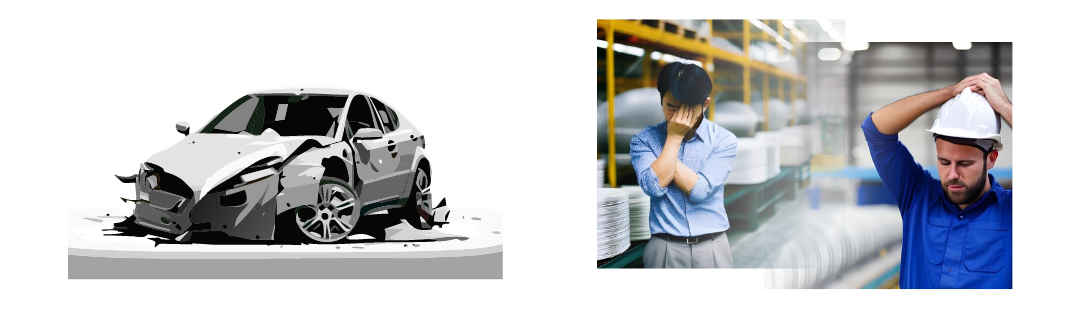
4. 近年の洗浄ニーズ
(1) 高清浄度の要求
近年、欧州を中心に自動車部品に求められる清浄度が厳しくなっています。従来は「残渣の重量が〇g以内」といった重量法が清浄度の基準でした。近年は「残渣の最大径が〇μm以内」といった、粒子の大きさを基準とする方式が主流になっています。これは、燃料噴射ノズルなどの小径オリフィスへの目詰まりや、摺動部品の摩耗低減が考慮されているものと考えられます。すなわち、残留異物の大きさを洗浄技術で制御することが求められており、清浄度検査についての国際規格”ISO-16232”や、”VDA19”が制定されました。
自動車はパワートレイン内の潤滑油の粘度を下げることで、燃費性能が向上することが知られていますが、これにも残留コンタミの大きさが関係します。一般的に潤滑油の粘度が下がると、形成できる油膜が薄くなります。油膜が薄いと、機械の摺動部や駆動部内で許容できる異物サイズが小さくなります。それに伴って部品に求められる清浄度が厳しくなっています。
建機部品や油圧部品、航空機のエンジン部品などでも、残留コンタミサイズにより清浄度が管理されるケースが多く見られるようになっています。部品により清浄度を達成するプロセスは違いますが、丁寧かつ確実に部品を洗浄することが求められています。
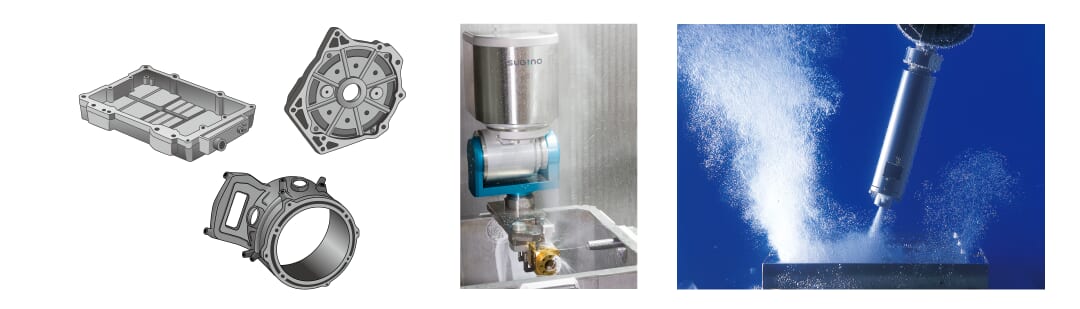
(2) 省人化・自動化
かつて洗浄工程は作業者の手作業に頼ることが多く、脱脂性の強い溶剤に浸漬する方法が長く使われてきました。近年はオゾン層の保護などの環境面や、人体への安全性を求める動きから、使用できる洗浄用溶剤が制限されています。そのため、自動運転を行う洗浄機や新しいタイプの洗浄剤の開発が年々進んでいます。
近年は少子化が進み労働力が集まりにくく、洗浄工程においても自動化が求める声が増えています。洗浄評価テストや乾燥テストで来社されるお客様のお話を伺うと、以前は清浄度やバリ取りなど品質面のニーズがほとんどでしたが、最近では人手不足から自動化のために導入したいという声が増えています。今後はより自動化のご要望が増えていくものと考えられます。
5. 洗浄不良が起こる理由とその対策
(1) 油分・切りくず(切粉)残り
加工部品の汚れは、大きく分けると”油分(脱脂)”と、切りくず(切粉)などの”異物”に分けられます。油分は、洗浄剤の化学反応や洗浄液の温度を上げて融解させる方法で除去します。切りくずなどの異物は、洗浄噴射による衝撃力や水流により、洗い流すことで除去します。
細かな異物は油と共に部品表面に付着しているため、効率良く確実に除去するには、噴射力と洗浄剤の化学的性質との相乗効果を狙うことが有効です。
油分やコンタミ残留などの洗浄不良はなぜ起こっているのか、対象になる部品を部位ごとに分けて原因を考えると、対策が見えてきます。ここからは部品の部位ごとの洗浄技術について解説します。
① 部品外観の洗浄不良
十分に洗い流せていないか、洗浄水が当たっていないことが主な原因です。鋳物部品のリブ形状の影や、深いくぼみ、深穴など、部品の形状によって、洗浄液が当たらない洗浄死角が生まれます。洗浄条件を考える際は、洗浄死角が発生しないように注意する必要があります。
部品の表面に付着する汚れが切りくずの場合は、流量を増やして切りくずを洗い流すことで洗浄できます。油分のように固着する汚れについては、洗浄圧力を上げて噴流で落とすか、洗浄剤の化学的性質を利用し、油分を分解除去することが有効です。
よくある不具合として、ノズルの配置設計が悪く洗浄液が全面に当たっていないことや、複数のノズルから同時噴射する際に、ノズルから噴射される水流同士が干渉して洗浄対象部位に届いていないことが挙げられます。これでは洗浄の対象部位をしっかりと洗うことができません。対策として、プログラム調整により洗浄条件を用意に変更できるノズル移動方式の洗浄機を用いることが挙げられます。洗浄水が当たっていても汚れが取れない場合は、噴射力自体が足りないことが考えられるため、洗浄圧力を増やすなどの対策が求められます。
② タップ穴など、止まり穴の洗浄不良
止まり穴の洗浄不良は困難な課題です。タップ穴の奥底まで洗浄液が届かないと、油分や切りくずを除去できません。ジェット洗浄でタップ穴から切りくずが排出される様子(動画)をご覧ください。
シャワー洗浄機やジェット洗浄機で切りくず残りが発生する場合は、ノズルの狙いが正しく設定されていないために、狙い位置がずれていたり、洗浄水が垂直に当たっていなかったりすることが考えられます。また、噴射水圧が不足していると、穴の奥底まで噴流が届かないこともあります。
切りくずの除去にはノズルの性能も関係します。確実に狙った箇所を洗浄するには、ノズルからの噴射水が広がらない=収束性の良いノズルが必要です。加えて、確実に真っすぐ飛ぶ=直進性も求められます。噴射性能の良いノズルを選択し、対象部に確実に洗浄水を当てる設計検討が必要と言えます。
カール状の切りくずがバネのようになって、タップの谷に引っかかっているケースもよく見られます。この場合は、高圧洗浄などの大きな外力をかけて吹き飛ばすか、前工程の加工条件を見直し、切りくずを小さくして引っかからないようにする対策が求められます。
また、超音波洗浄の場合は、穴の内部に空気が残り、超音波が伝播しないことがあります。この場合は真空脱気や、ワークの向きを工夫することが必要です。
③ 油回路などの深穴の洗浄不良
油回路や潤滑回路の場合は要求される清浄度が厳しく、洗浄液を用いて油分や切りくずを除去することが求められます。
油穴は、メインの穴から枝分けされた経路が複数繋がっていることが多く、洗浄液を流す順番が重要です。切りくずが途中で引っかからないように、細い穴から太い穴の方向へ流すように洗浄します。また内部経路が長いため、圧力を高めたり、時間をかけて十分な流量を流したりする必要があります。このとき、複数のノズルから同時に噴流を流した場合は、中間地点で水流同士が干渉してしまい、流れを阻害することがあるので注意が必要です。事前に流体解析や 実ワークを使用した洗浄テスト で検証することが重要です。
油穴の奥部は鋳肌などの素材面であることも多く、鋳砂や離型剤などが残留していることがあります。対象部位に直接洗浄液を当てることが重要で、汚れが強固な場合はブラシを通して除去することも有効です。
(2) 洗浄液の汚れ
洗浄機で使用する洗浄液は、フィルタを用いて循環ろ過して、再利用するケースがほとんどです。フィルタは部品の材質や付着異物など、捕捉対象によって方式やろ過精度を選択します。フィルタの破損やろ過精度が不十分な場合は、2次側に異物が流出し洗浄液の水質が悪化します。当然ながら、汚い洗浄液で洗浄してもワークはきれいになりません。清浄度を達成するために水質管理は大変重要です。
洗浄液の水質悪化の原因は、前工程から持ち込まれるコンタミや油分にあります。液中のコンタミを除去するためには、フィルタのろ過精度を高くすることが有効です。フィルタのろ過精度の表記は、フィルタの目の大きさを示す公称値や、フィルタが捕捉できる大きさを示す絶対値があり、求められる清浄度からフィルタの要求精度を求めて決定します。その一方で、ろ過精度を必要以上に高くすると目詰まりの頻度が高くなり、フィルタ交換が頻発してランニングコストに影響するため注意が必要です。サイクロンフィルタのように、交換材がないメンテナンスフリーのフィルタもあります。使用条件や予算に合わせて選択することが重要です。
液中の油分を除去するためには、オイルスキマーなどの油分回収装置を用います。ベルト方式やフロート回収方式、マイクロバブルによる浮上分離方式など、様々な方式の油分回収装置が各社から販売されています。
(3) 切りくずの再付着
洗浄機内に洗浄した部品の汚れが蓄積し、洗浄時に汚れが壁や天井から跳ね返って再付着する場合があります。水中でのジェット洗浄や超音波洗浄においても、液中に汚れや異物が浮遊している場合、それらが再付着することがあります。壁面を洗浄して汚れの蓄積を防止する、リンス工程を追加するなどの対策を行います。
(4) 洗浄後の完成部品の取扱不良
せっかくきれいにした部品も、洗浄後の搬送時に汚してしまうことがあります。作業者による手動搬送の場合は、洗浄後の部品は常にきれいな手・手袋で取り扱うように注意が必要です。また自動搬送装置の場合は、クロスコンタミネーション(交差汚染)を防ぐために、搬入出で接触する部品を分離することが求められます。
洗浄後の部品が周囲の機器などに接触し、部品の一部が欠けて新たに異物を発生させることも考えられますので、取り扱いには注意が必要です。清浄度を測定する検査作業にも同じことが言えます。清潔な環境や、金属接触が発生しないような治工具の準備が求められます。
空気中に浮遊する汚れが部品に付着することもあります。洗浄後の部品は袋に入れて保管し、後工程をクリーン環境にすることが有効です。
6. 最適な洗浄方法を見つけるには
部品に付着している汚れの種類と、部品が構成されている形状要素を分類します。その後に生産性、すなわち洗浄にかけられる装置の導入費用や日々の作業者の人工を考慮し、それぞれの現場に適した洗浄機や運用方法を選定していきます。
その後、各洗浄機メーカーに依頼して、実際のワークまたは類似条件にて洗浄テストを実施して、洗浄機の能力を確認します。最適な洗浄方法には複数の要因が関係しますので、ご導入前には 実機テスト にて性能を見極めることをおすすめします。
(1) 汚れの種類とその対策
① 油汚れ(脱脂)
・洗浄流量を増やす
・洗浄剤の化学的性質を利用して溶解する
・洗浄剤の選定のため洗浄機メーカーに相談する
・液温を上げて溶解しやすくする
・洗浄液を綺麗に保つ
・前工程からの持ち込み油を減らす
・洗浄機のタンク内で油を除去して水質を維持する
② 切りくず(切粉)
・洗浄圧力を上げる
・洗浄死角を作らない確実な設計検討を行う
・ノズル移動方式を採用し調整を容易にする
・再付着対策を行う
③ 繊維質など、周囲環境からの持ち込み
・洗浄後のワークはクリーン環境で取り扱う
・軍手など繊維材質の手袋を用いない
(2) 構成部位ごとの洗浄方法
① 止まり穴/止まりタップ穴
・洗浄噴射は穴に対して垂直に当てる
・圧力を上げて奥底まで確実に洗う
② 貫通穴/通しタップ穴
・穴内部の側面に水が当たるように、斜めに狙う
③ 油穴
・流量を増やす/洗浄時間を増やし十分に粗い流す
・メイン穴や枝穴を同時に洗うのではなく、細い穴から順番に洗う
・水中洗浄 を行う
④ 部品外観
・洗浄死角を作らない(リブや深みぞは要注意)
・ノズルや治具の設計時に十分に検討する
・十分に洗い流せるだけの流量を確保する
・ノズルからの噴流同士が干渉しないように気を付ける
(3) 生産性を考えた洗浄機と運用方法について
① 生産形態
・バッチ処理 or ライン流し
・手動搬送 or 自動搬送(コンベア方式/ロボット搬送/etc.)
・サイクルタイム
装置台数=各洗浄機の必要時間/ラインサイクルタイム
② 予算の目安
・低圧リンス洗浄機 :500万円~
・高圧ジェット洗浄機:1,500万円~
(4) 洗浄テスト
スギノマシンでは、業界トップクラスの充実したテスト環境をご用意しております。詳しくは、リンク先の案内をご確認いただき、ご希望の際はお気軽にお申し付けください。