ロボットバリ取り技術
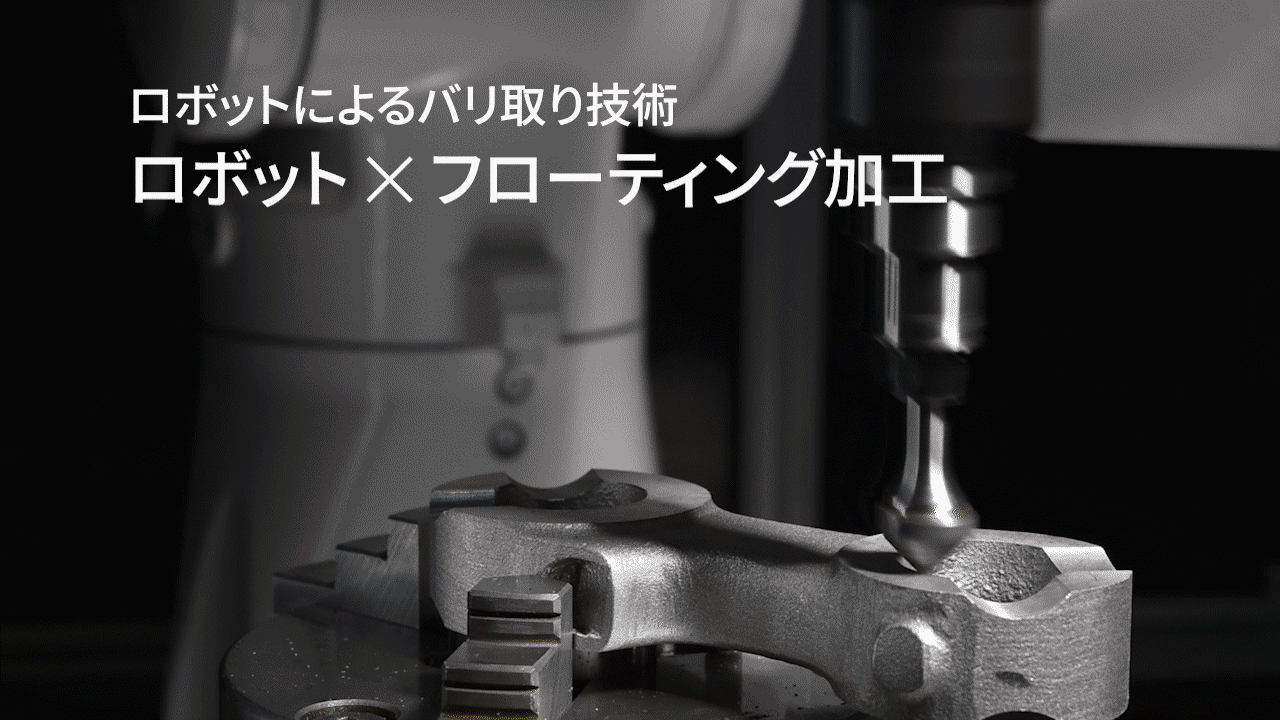
近年、産業用ロボットが加工現場に普及した事でロボットによるバリ取りの自動化も検討されるようになりました。ところが、実際には様々な問題が発生しスムーズに自動化できることは稀です。それら多くの問題を解決するため、スギノマシンではフローティング機構を搭載したエンドエフェクタBARRIQUAN(バリカン) を開発しました。デバラボでは、フローティング加工技術を洗練し皆様と課題解決に挑戦します。
ロボット × フローティング加工
手作業のバリ取りを自動化させる方法として、人の動きに近い動作が行えるロボットが検討に挙がります。ところが、正確な加工軌跡を作るのが難しいロボットの構造的な問題や、切削工具の摩耗によるバリの大きさ・形状の変化、ワーク寸法のばらつきなど、バリ取り自動化特有の問題が生じます。
このような問題を解決するのが、「フローティング加工」 です。
フローティング加工とは、フローティング機構を備えたエンドエフェクタによって工具をワーク形状にならわせることで、ロボットの加工軌跡のズレを吸収しつつワーク形状の変化に対応し、ワークの削れ過ぎやバリの取り残しを防ぐ加工方法です。
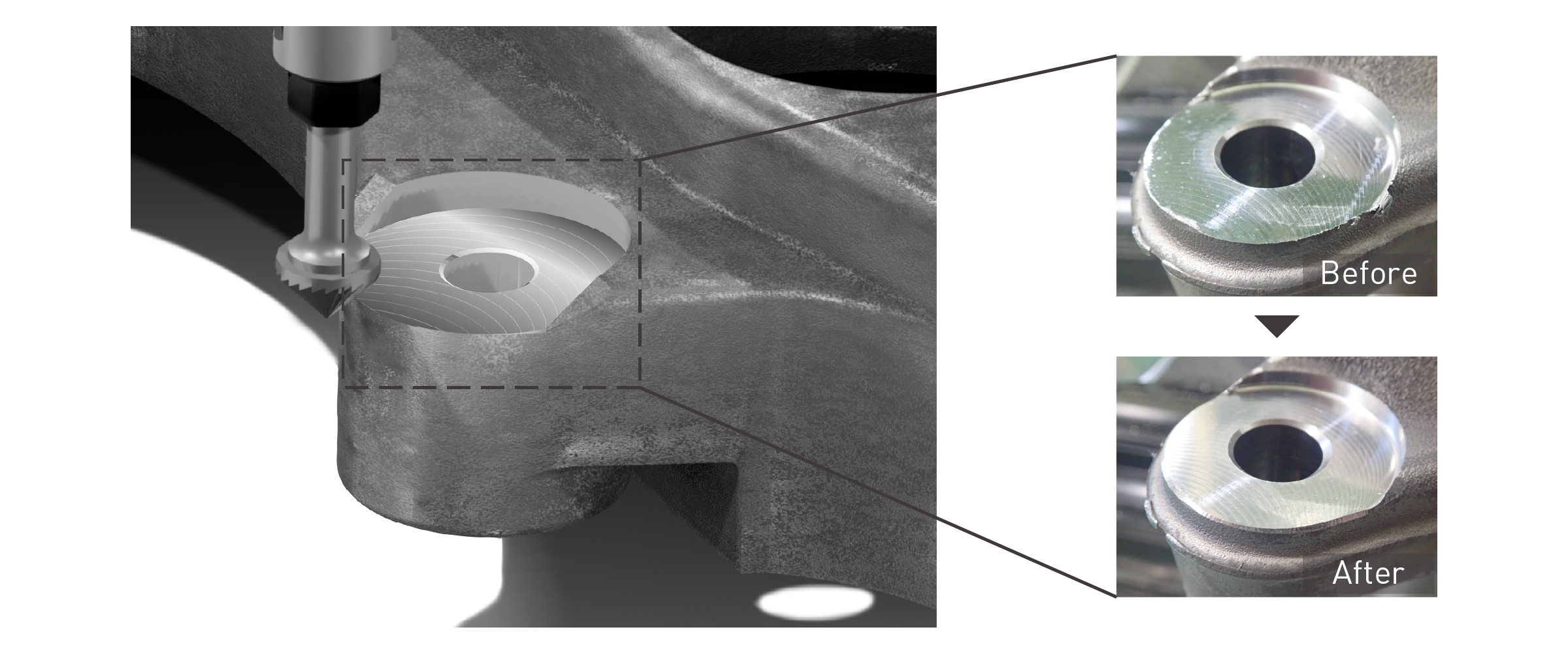
ロボットバリ取りに重要な4要素
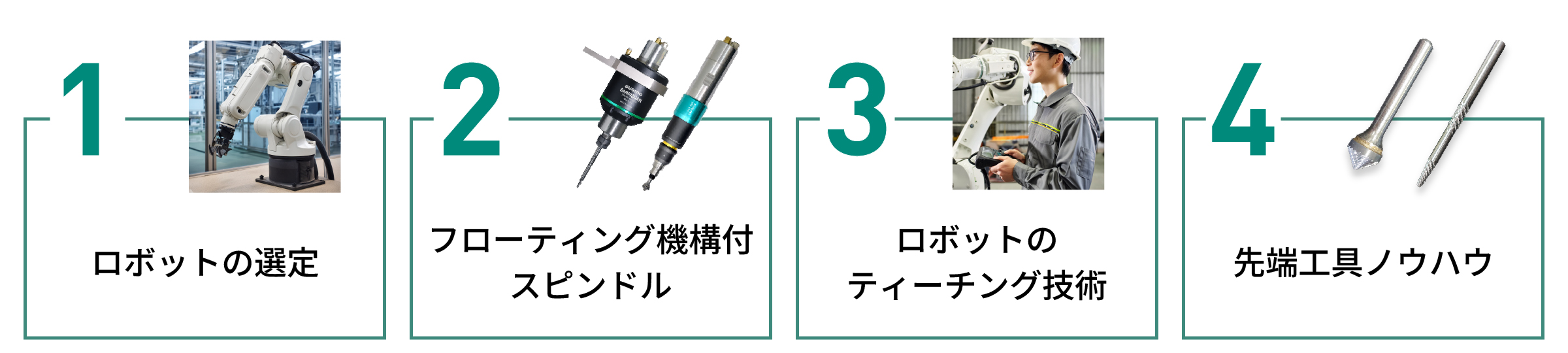
ロボットバリ取り自動化をスムーズに実現するために必要な4つの要素について解説します。
1 ロボットの選定
産業用ロボットは用途により構造が異なり、性能もさまざまですが、バリ取りに適したロボットを選定することで安定的な自動化を実現します。
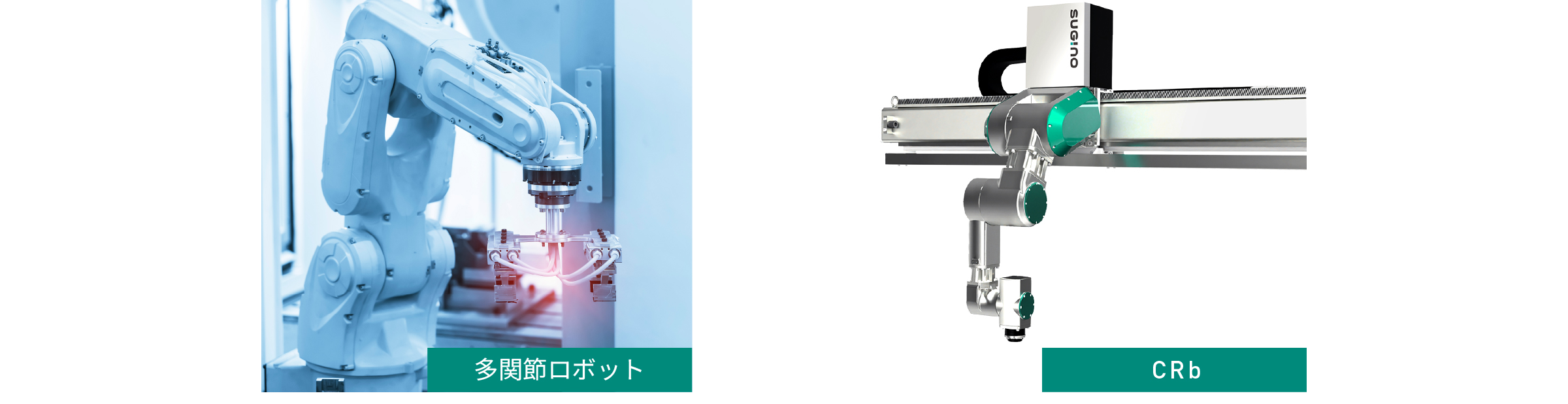
① 垂直多関節ロボット
多関節構造を持ち人間の腕のような形状が特徴の産業用ロボットの一種です。立体的かつ自由度が高く、人の動きに近い動作ができる特徴から、手作業で行っていた繰り返しの単純作業を代替させるのに適しており、ロボットバリ取りにおいて最もポピュラーです。
多関節ロボットには安全柵が必要となる産業ロボットと不要な協働ロボットがありますが、バリ取りにおいては作業員の安全とロボットの動作速度の観点から産業ロボットがより適しています。また、使用環境によっては微細な切粉や切削油が飛散するため、IP等級の確認は必要です。
② CRb – Connected Robot
狭い空間に設置し、稼働できるスリムな構造が特徴の産業用ロボットです。省スペースで、剛性が高く、優れた直進性と高い位置決め精度が特徴です。
狭小空間において最小限の動作でバリ取りを行いたい場合や、長尺ワークを加工する際に効果を発揮します。
2 フローティング機構付きスピンドル(エンドエフェクタ)
ロボットバリ取りにおいてはワークの変化にどう対処するかが重要となります。
ビジョンカメラや力覚センサを用いたソフトウェアによるフィードバック制御で対処する方法もありますが、高い品質が得られる反面、導入コストの高さや加工速度の遅さという欠点があります。
バリやワーク寸法の変化に対応できるエンドエフェクタの選定により、フィードバック制御を不要にすることで、コストと加工速度を両立させたロボットバリ取りが行えます。
回転工具を使用したロボットバリ取りを行うには、フローティング機構付きのスピンドルを使用したフローティング加工が有効です。フローティング機構には伸縮型と傾動型の2種類があり、バリの発生箇所に応じて選定する必要があります。
① 伸縮型
伸縮型は、工具をZ方向に伸縮することでワークにならいます。
ワークのエッジに発生するバリ取りに適していて、鋳物の輪郭や機械加工後のバリ取りで多く使用されます。
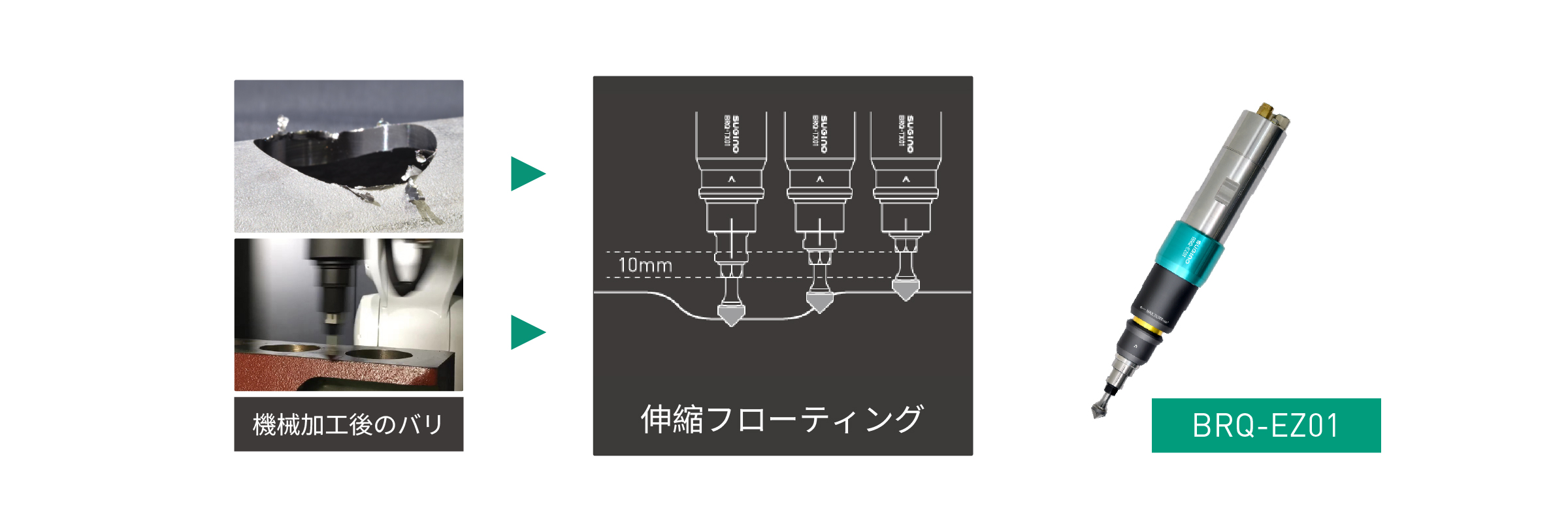
② 傾動型
傾動型は、工具が傾くことでワークにならいます。
ワークのエッジよりも、「面」に発生する突起やバリに適しています。アルミダイキャストのパーティングライン除去等で多く使用されます。
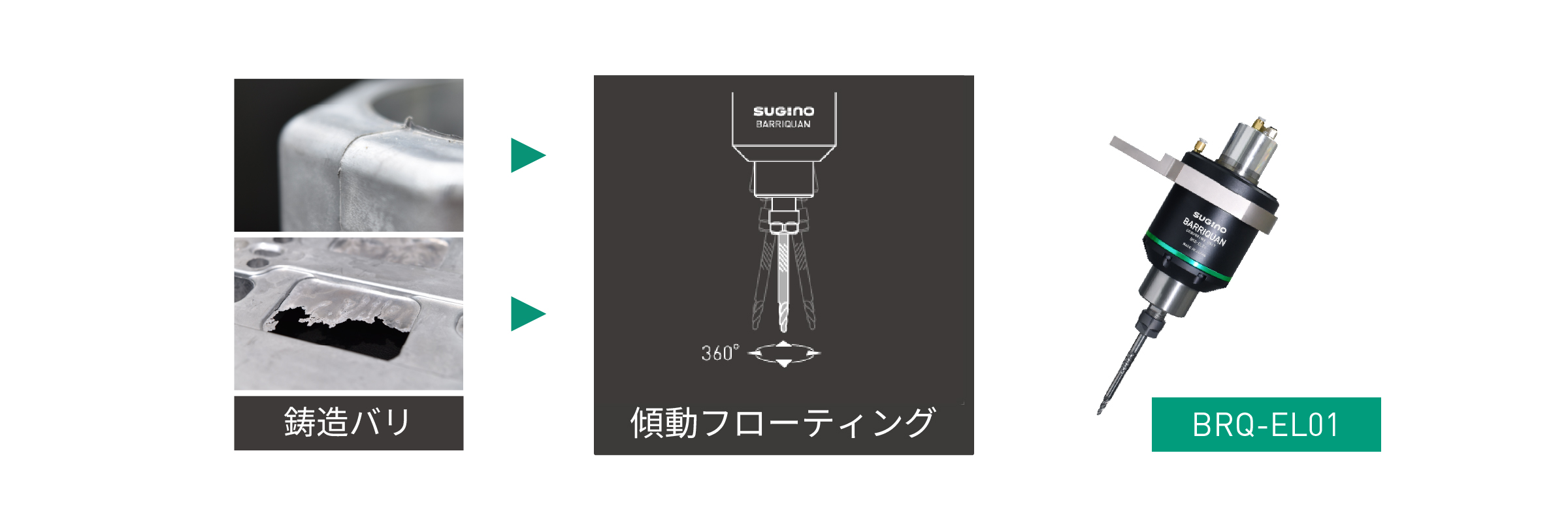
3 フローティング機構の特性を理解したロボットティーチング技術
フローティング加工は、切削加工でありながら先端工具の位置が断続的に変化する、精密切削加工では通常ありえないバリ取りに特化した工法です。
このため、品質を追求するためには一般的な切削理論に加えて、フローティング加工独自の特性を理解したティーチングを行う必要があります。
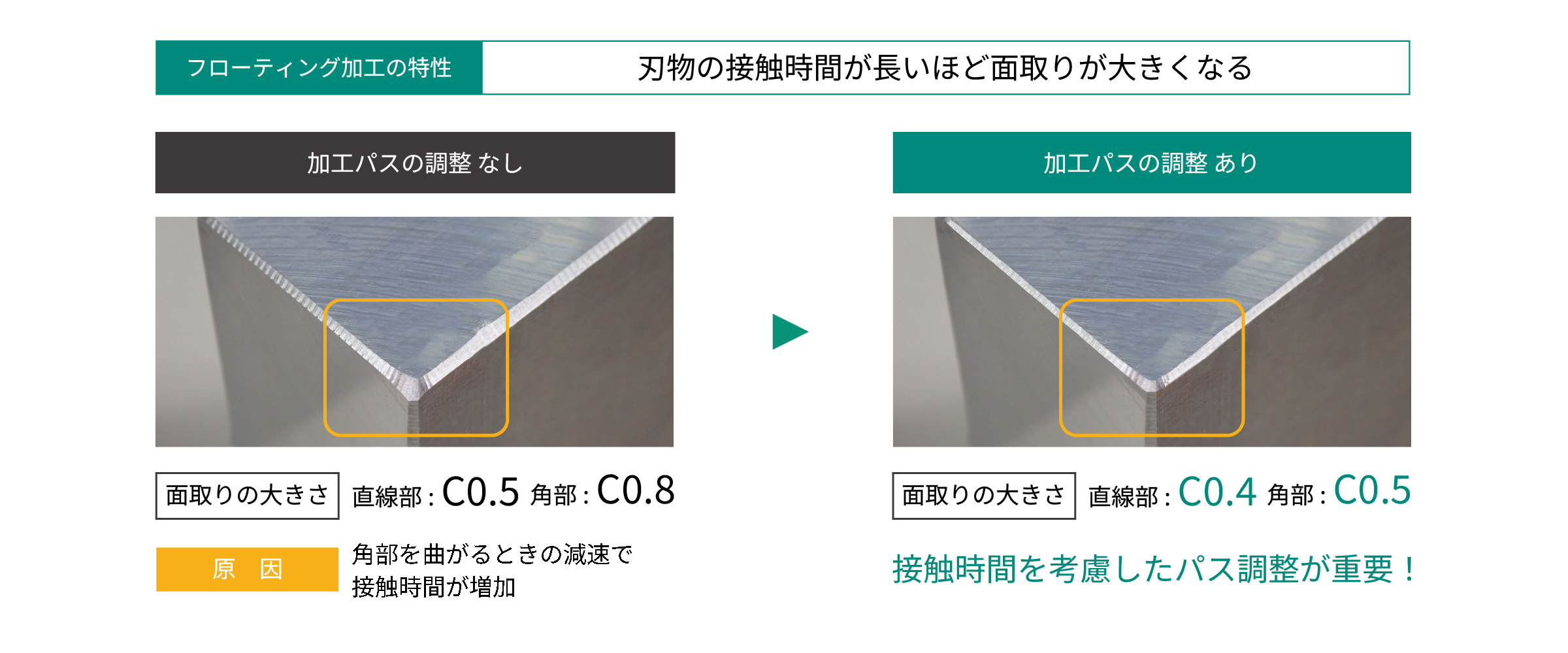
4 先端工具のノウハウ
ロボットバリ取りでは手作業と同様、目的のバリ取り品質を得るために、バリの種類や大きさに合せた工具を選定します。フローティング加工においてはさらに、フローティング加工と工具の相性も鑑みた工具選定が重要になります。
伸縮フローティング加工で良く使われる90°円錐型超硬ロータリーバーを例に紹介します。超硬ロータリーバーは、刃先の種類でおよそ4種類に大別できます。それぞれに切削性や二次バリの抑制具合に差がありますが、同じ刃先の種類であったとしてもメーカごとに特性や相性が異なります。さらには材質やバリの種類によってもフローティング加工との相性が変化するため、最適な先端工具を選定し品質を追求するためには専門的な知見が必要となります。
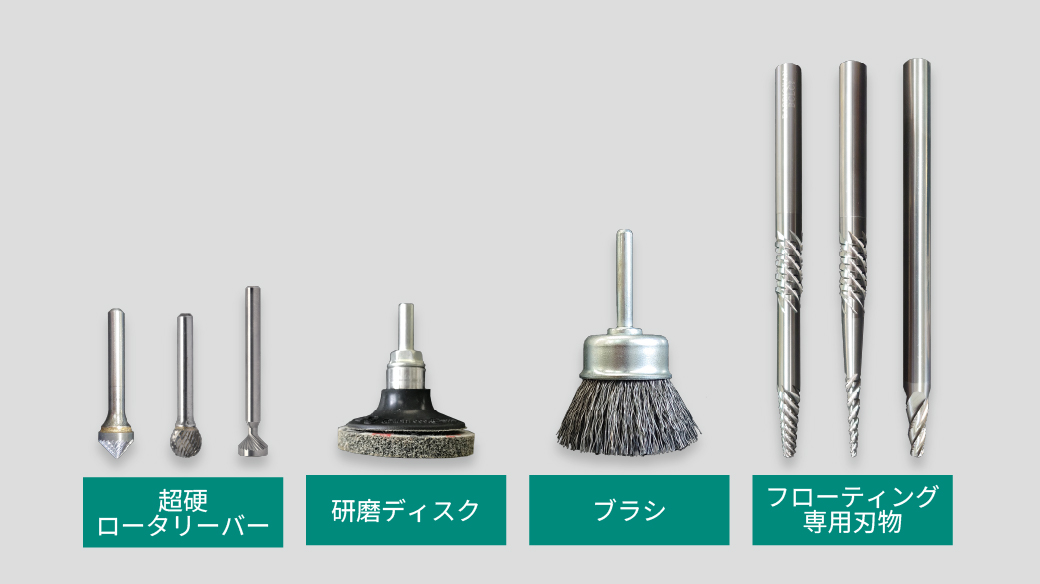
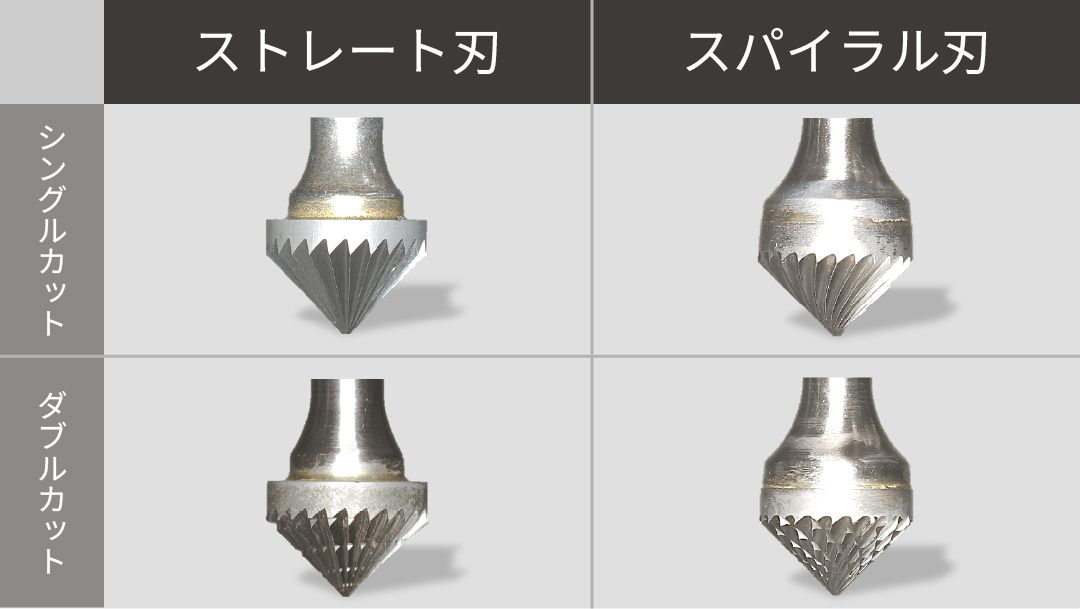
ロボット × フローティング加工 バリ取りの特長
1 立体的な複雑形状も加工できる幅広い適応力
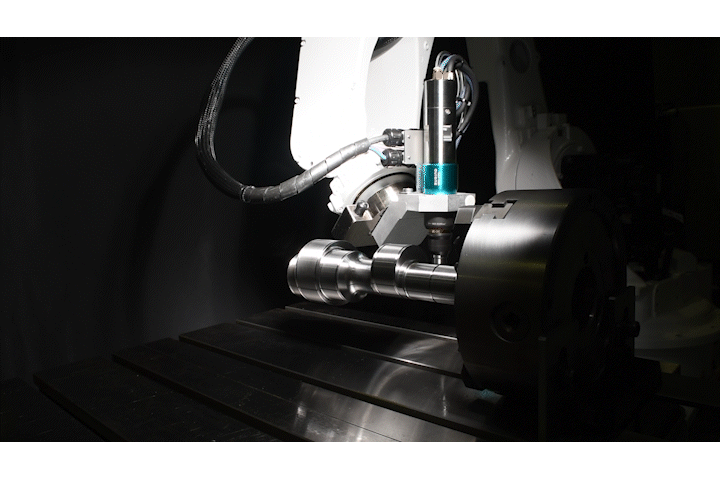
ロボットの多関節構造で人の動きに近い動作ができることを活かし、自由な角度や姿勢からアプローチできるため、立体的な複雑形状のワークのバリ取り加工にも適応します。
マシニングセンタのような加工機では複数軸の同時制御が必要になる動作でも、ロボットであれば1台で完結させることができます。
また、適応できる形状が多いため、1機種の専用機ではなく多品種の汎用自動バリ取りシステムとすることも可能です。
2 安定した品質のバリ取りが可能
作業者を人からロボットに置き換えることで、人的要因に影響されない連続加工が可能となります。
フローティング加工を組み合わせることでワークやバリの変化に対応しつつ、ロボットの加工軌跡のズレも吸収するシステムとなるため、連続加工した際の品質が格段に安定します。
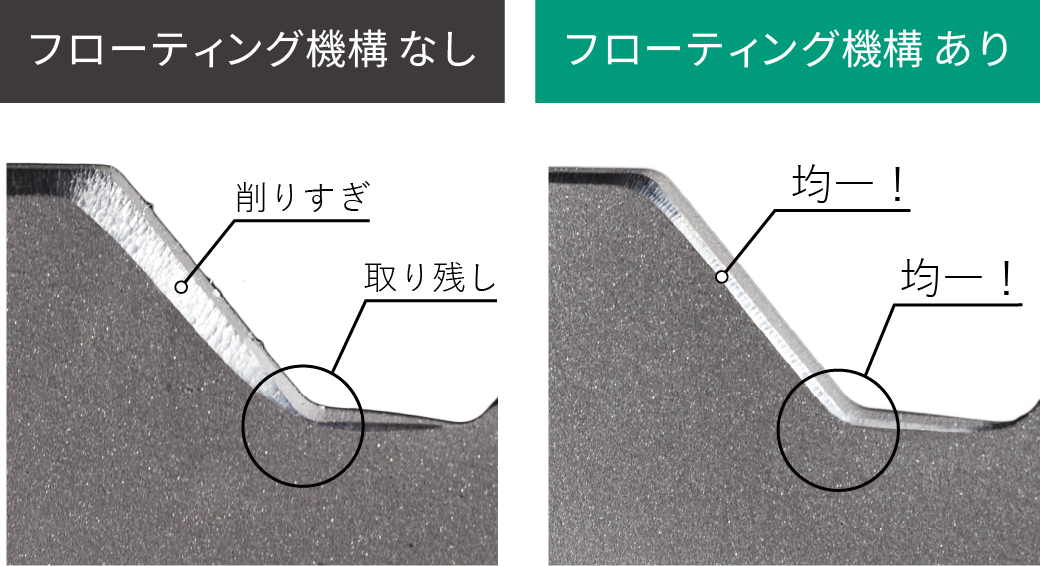
3 小型ロボットをバリ取り加工機に
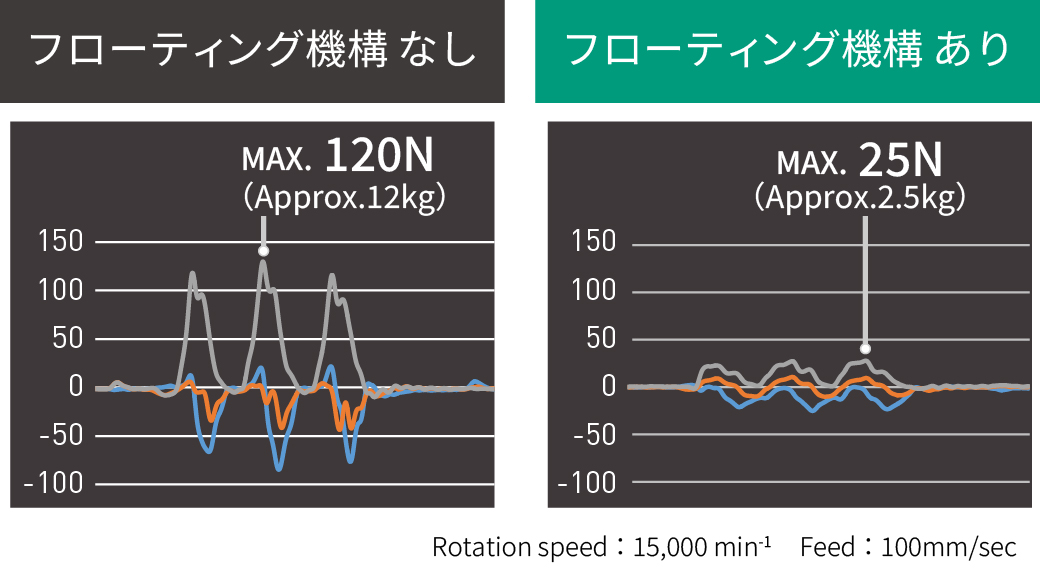
ロボットで加工する場合、ロボットの可搬重量はエンドエフェクタ自体の重さに加えて加工負荷に耐えられるだけの可搬重量が必要となるため、大型化する傾向にあります。
フローティング機構には加工反力の衝撃を吸収するダンパーの役割を果たし、ロボットにかかる加工負荷を軽減する効果があります。
フローティング機構なしの場合は20kg可搬以上のロボットが必要になる加工条件でも、伸縮フローティング機構ある場合では7kg可搬以上のロボットで加工が可能となるため、小型ロボットで省スペースながらも高速バリ取り加工が可能となります。
4 工具寿命の安定化
フローティング機構は、刃物押付け力と切削抵抗の均衡により刃先位置を変えて加工します。このため加工中、突発的に切削抵抗が増大しても加工圧が自動調整され一定の力で加工するので、先端工具に過大な負荷がかかりにくく工具寿命が安定します。
オプション品のSGフローター(C-FS01)は加工トルクでも反応する高反応仕様であり、よりフローティングしやすくなったことで工具寿命のさらなる安定化や、切削抵抗の変化が大きい高低差のあるワークの面取り量安定に効果が見込めます。
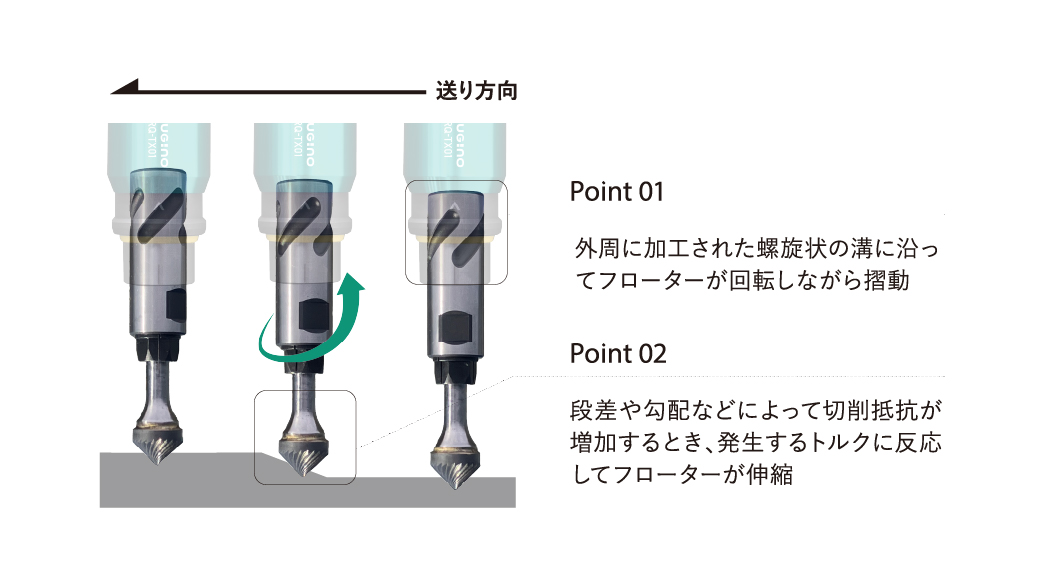
ロボット × フローティング加工でできること
フローティング加工が得意なバリ

① 機械加工後のバリ
フライスやエンドミル加工後や研削加工後のワーク端面に発生するバリを除去することを得意としています。
特に素材面と加工面の境目のような輪郭が不定形な箇所や、歪みやたわみのあるワークにおいて効果を発揮します。
主に伸縮型のフローティング機構付きエンドエフェクタを選定します。
② 鋳造バリ(パーティングライン・膜バリ)
金型の合わせ面に発生するパーティングラインや膜バリの除去といった鋳造品の中仕上げ~最終仕上げを得意としています。
大型のスピンドルやトリミングプレスによる粗仕上げでは取り切れない細部まで仕上げることができます。
主に傾動型フローティング機構付きのエンドエフェクタを選定します。
フローティング加工が不得意な加工
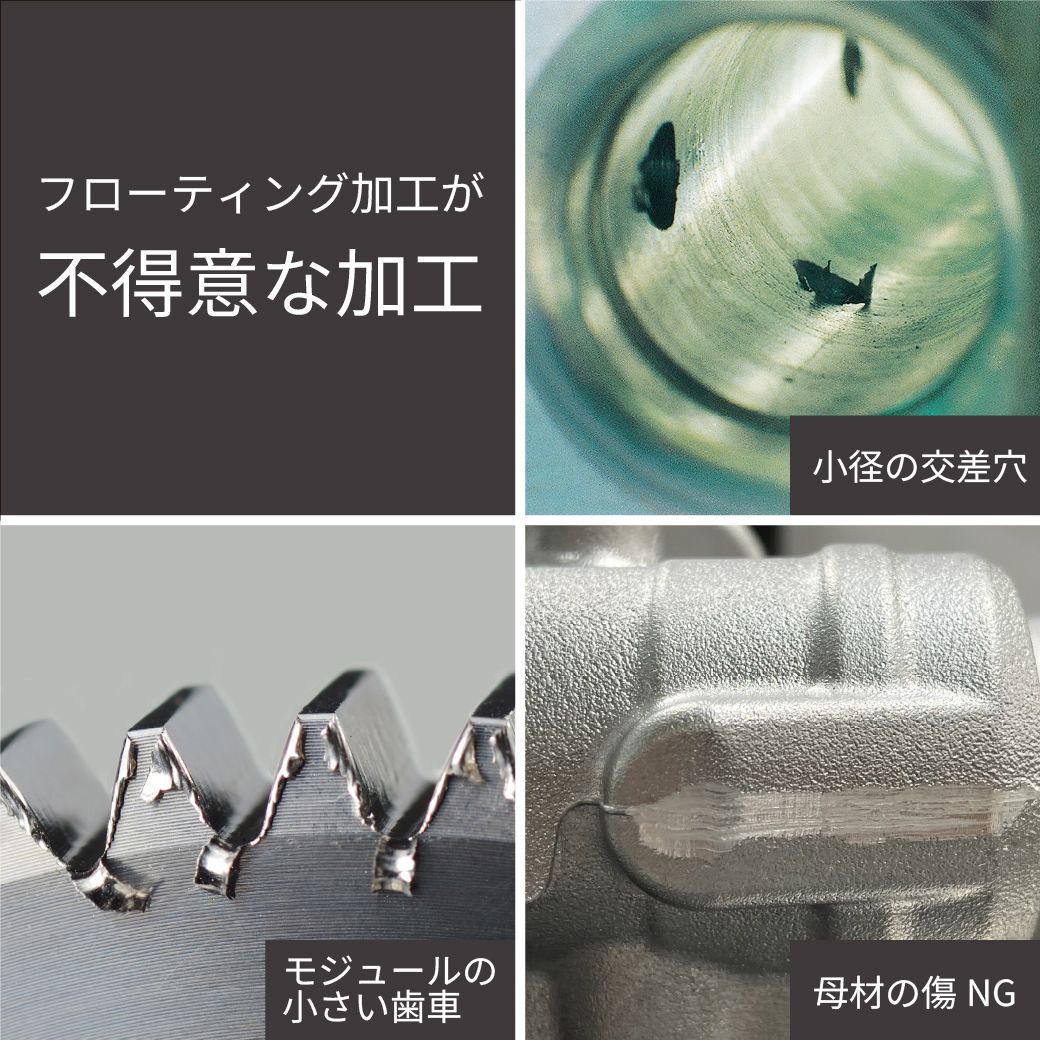
① 先端工具がアプローチできない箇所
フローティング加工は切削加工であるため、先端工具が当たらなかったり干渉したりする箇所は加工自体ができません。
また、先端工具は当たるもののフローティング機構が適切に機能する先端工具の選定やアプローチ方法ができない場合、加工をすると品質不良やエンドエフェクタの早期破損につながるため対応不可です。
例:交差穴、モジュールの小さい歯車など
② 母材への傷がNG
フローティング加工は回転工具がワークをならうため、必ず加工面には切削痕が残ります。切削痕が残ることで問題となる外観部品や機能部品は対応できない場合があります。
例:切削痕NGの部品、外観部品、内面研磨仕上面、シール面など
このようなバリには高圧水による「ウォータージェットバリ取り」が有効です。
ウォータージェットは噴射距離が離れても衝撃力が減衰しにくく非切削加工のため、深穴や交差穴など刃物が届きにくい場所や、母材を傷つけたくないワークのバリ取りに適しています。
加工テスト実施中
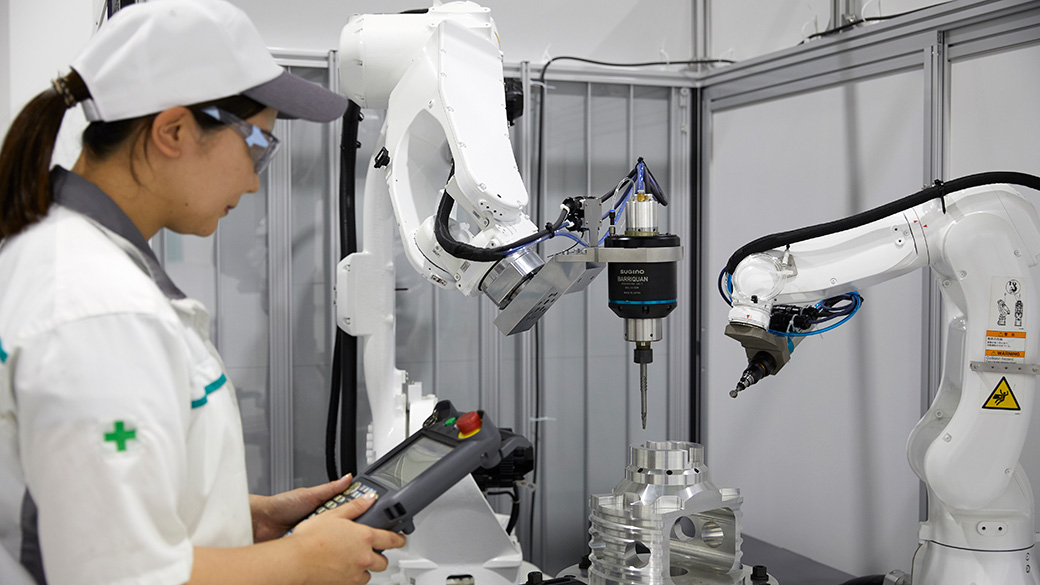
バリ取り研究所”デバラボ”では、ロボットでバリ取り自動化を検討されているお客様からの加工テスト依頼を随時承っております。
ただ加工テストを行うのではなく、テスト実施前にお客様のお困り事を共有いただき、目指すゴールを明確化した上で、デバラボの設備でテスト加工を行います。テスト結果はレポートにまとめご報告させていただきます。
加工テストを通して、お客様とともに自動化の実現を目指し検討させていただきます。