Machining Center: Benefits of Automation
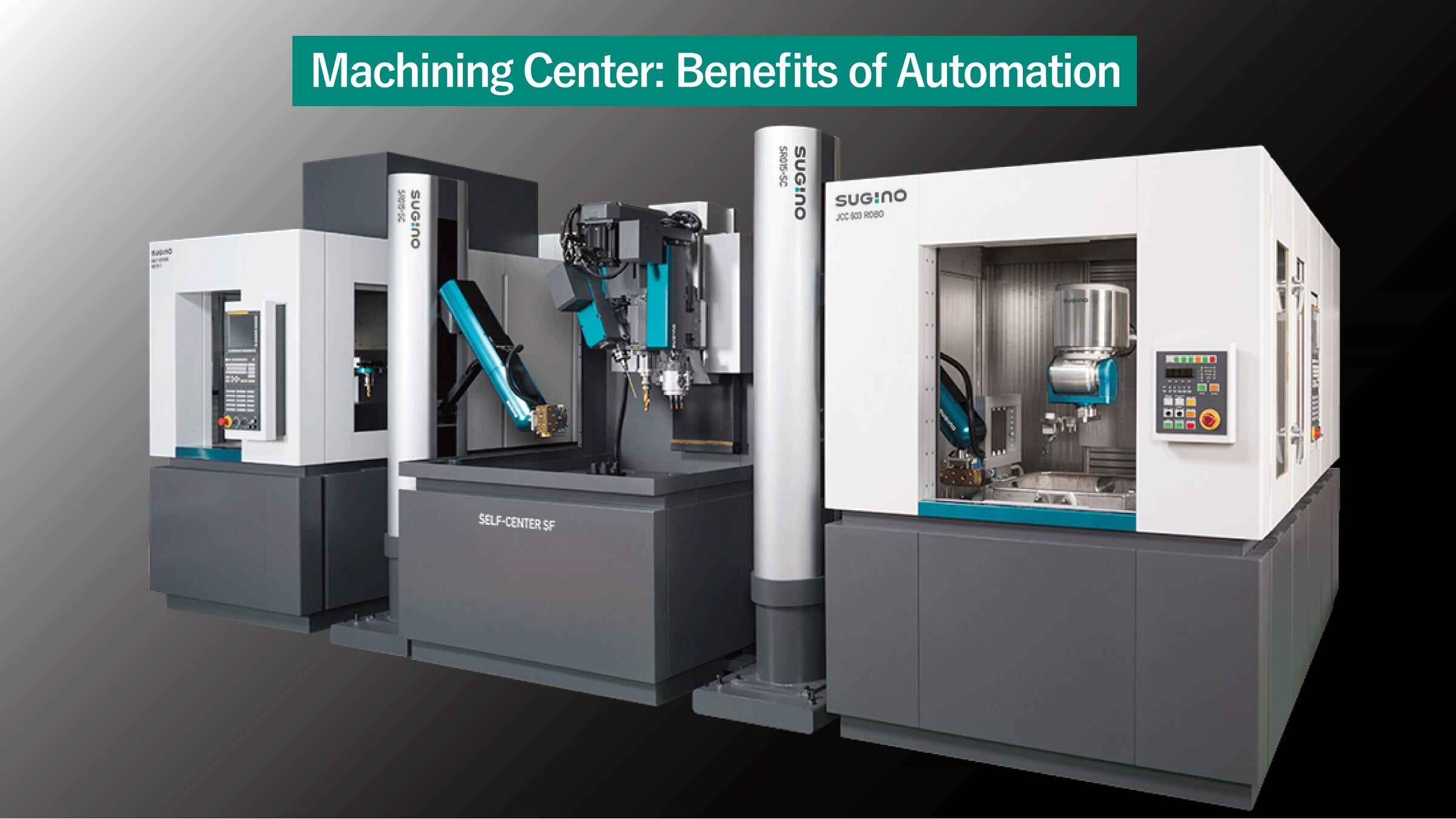
Automation is the replacement of manual tasks and processes with machines.
In machining centers, tasks such as transportation, attachment/detachment, deburring, coolant management, cleaning, and drying are all performed manually. Automating these processes is expected to have many benefits, including improved working conditions, increased productivity, and stabilized quality. However, automation cannot be achieved simply by replacing humans with robots. We will introduce the benefits of automation, as well as challenges and solutions, and ways of thinking about it.
1. Five benefits of automation
1. Improving working conditions
Since machining centers are machines that perform cutting processes, the surrounding area can become a poor working environment due to the noise of the process, the heat exhausted from the machine, and the misty atmosphere. By automating tasks around the machine, such as the attachment and detachment of workpieces, workers can be moved away from the machine and the working environment can be improved.
Even if there are setup tasks that cannot be automated, if the attachment and detachment of workpieces can be automated, it is possible to not only improve the working environment but also reduce the number of people by adjusting the time allocation, such as performing setup during the day and concentrating processing at night.
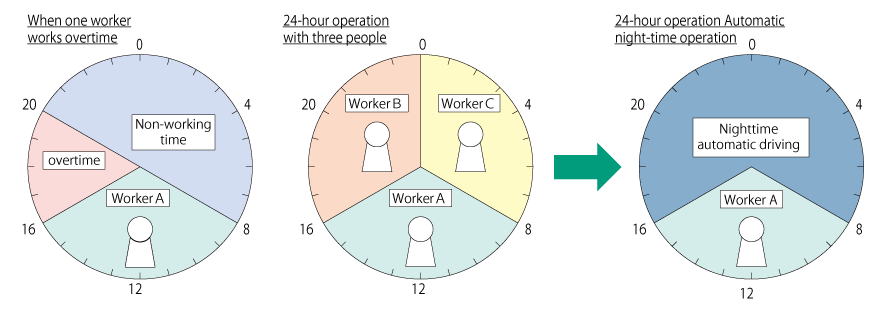
2. Improving productivity
Labor saving improves productivity.
Improvements in the performance of machines and tools have shortened processing times. However, the timing of workpiece attachment/detachment and transportation has become faster, making it difficult for people to leave the machine and do other work. As a result, shortening processing time can lead to a contradiction in which the burden on the worker increases. If transportation and attachment/detachment are automated, such contradictions do not occur and the effect of shortening processing time can be maximized.
In addition, skilled workers and multi-skilled craftsmen perform various tasks every day, but not all of them are difficult. By automating simple tasks by entrusting them to robots, time can be saved and they can focus on tasks with higher added value. As a result, productivity improves dramatically.
3. Stable quality
Automation and mechanization can reduce subtle variations in mounting position that occur when workers attach and detach workpieces, resulting in stable quality.
Automating deburring also results in a uniform finish and prevents defects caused by burrs that are left behind.
Automating and mechanizing cleaning can improve cleaning quality and shorten cleaning time.
4. Reducing human error
Robots and machines perform their work precisely according to the program, eliminating human error such as incorrect operation or missed checks.
5. Improve your company’s image by adopting automation technology
In the manufacturing industry, chronic labor shortages have become a social issue. The introduction of automation technology will greatly contribute to securing talented personnel and increasing employee motivation.
In addition, to create an environment where women and the elderly can work comfortably, there is a need to improve the image of “tough, dirty, and dangerous” and embody “easy (reduced workload), clean (clean environment), and safe (simplification).”
【Examples of automation and their effects】
1. Improving working conditions | 2. Improving productivity | 3. Stable quality | 4. Reduction of human error | |
---|---|---|---|---|
Workpiece attachment/detachment | - | ○ | ○ | ○ |
Coolant Management | ○ | - | ○ | ○ |
Workpiece transport | ○ | ○ | - | ○ |
Deburring | ○ | ○ | ○ | ○ |
Cleaning | - | ○ | ○ | ○ |
Dry | ○ | ○ | - | ○ |
2. Automation Issues and Solutions
Automation has many benefits, but many challenges must be overcome to keep an automated system running smoothly.
We will therefore divide the operation of automated equipment and systems into the following phases: “1.Startup”, “2.Operation”, “3.Changeover”, and “4.Maintenance”, and introduce the challenges and solutions for each phase.
1.Startup
Advanced technology is required for communication with external devices and for handling pre- and post-processing
Automated equipment requires advanced know-how for setup, such as teaching the robot how to attach and remove workpieces, and linking the NC operation of the machining center with external devices.
It is not uncommon for equipment for each process to be made up of multiple manufacturers, and connecting to external devices and exchanging electrical signals can take a lot of time and effort. Therefore, one effective option is to outsource the setup to a specialist company or equipment manufacturer that can handle all of this.
There is a demand for equipment capable of handling multi-product production
In the past, the prerequisite for automation was to accurately mass-produce products. Nowadays, the priorities have changed, and the ability to handle multi-product production has become an important point for automation.
The widespread use of industrial robots has improved their versatility in a variety of processes, but the functions and performance of the main processing machines, as well as jigs and programs, must also be able to handle multi-product production. When there are significant changes to the workpiece shape or size, processing content, or process, it becomes complicated to modify jigs and change programs, so it is important to make detailed plans at an early stage.
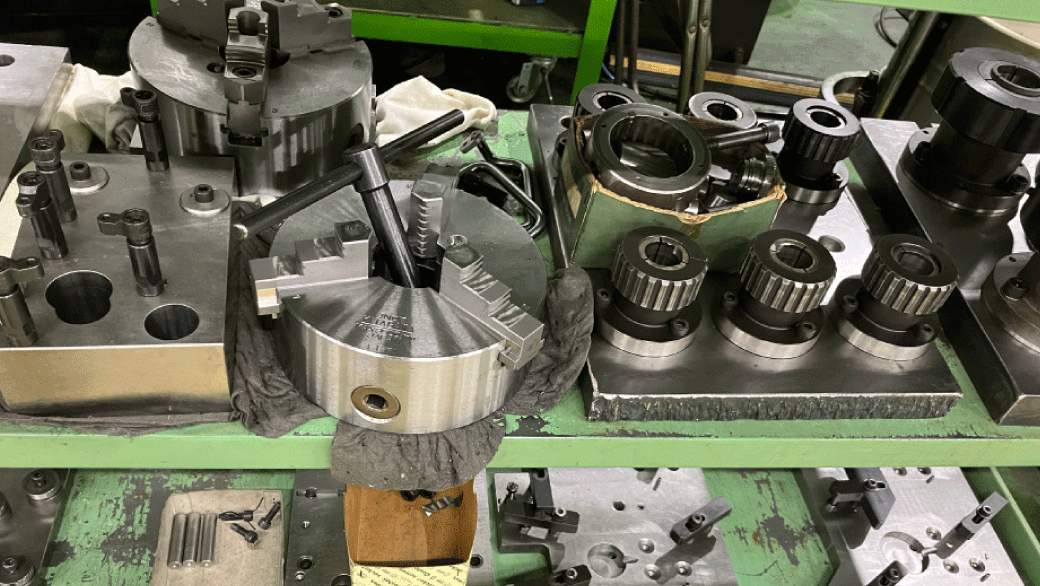
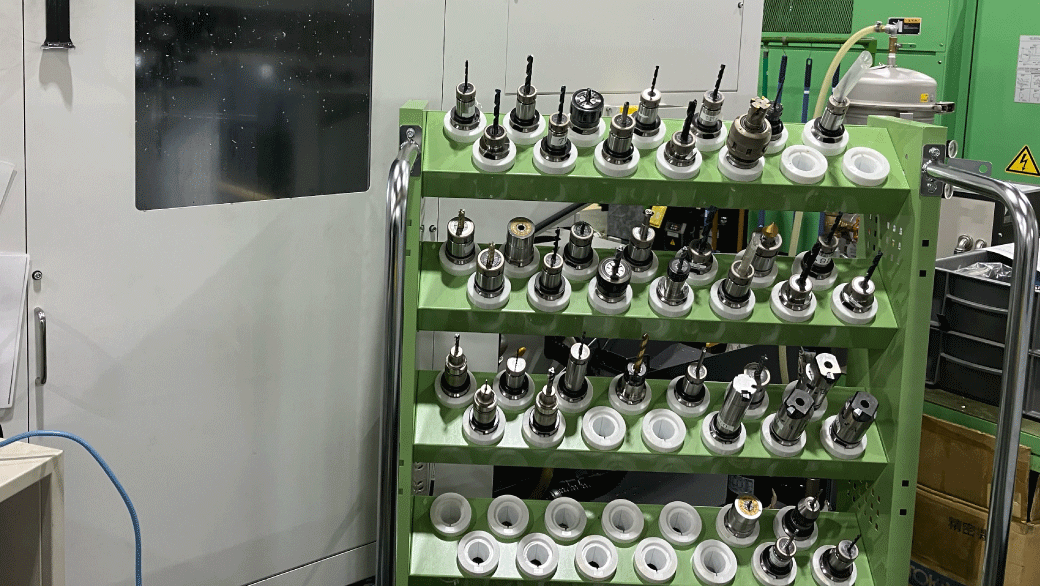
2.Operation
Nighttime automation cannot be achieved unless the causes of equipment stoppages are eliminated.
From the perspective of safety and quality assurance, machining centers require that the machine be stopped without delay if an abnormality occurs in the equipment. For example, by creating a program that measures the tool before and after processing and immediately stops the machine if an abnormality is detected, the production of defective products can be prevented.
However, once equipment stops, human intervention is required to restart it, and if conditions where human intervention is not possible continue for long periods of time, such as at night, productivity drops significantly. To achieve long-term continuous operation, in addition to setup skills and appropriate equipment selection, it is necessary to eliminate causes of equipment stoppages in advance by taking various considerations, such as setting conditions to prevent cutting chips from accumulating and cutting tools from suddenly breaking.
The quality of tools and coolant must be maintained for a long time.
By selecting tools with durability in mind and introducing a coolant purification system, the frequency of replacing consumables can be reduced, minimizing production line downtime.
3.Changeover
The tool layout must be changed every time the workpiece is changed.
Machines for producing a wide variety of products, in which the products to be processed change frequently, need to be equipped with a large number of tools to match the number of processes. If the number of tools that can be installed is limited, manual changes to the tool layout are required every time the product changes, increasing machine downtime and reducing productivity.
The equipment must be stopped and the tool length corrected.
Tool length correction is often done manually, requiring skilled work such as test cutting, measurement, and inputting the data into the NC device, with the device stopped.
By introducing an automatic tool length measurement system, the measured tool length can be fed back to the NC device and the tool length can be automatically corrected, realizing long-term automatic operation. It also makes it possible to prevent defective products caused by setting errors.
4.Maintenance
A maintenance area must be secured
It is important that machining centers and automated equipment are designed to allow for easy and quick maintenance, from daily inspections to responding to abnormalities.
The operation panel and accessible parts are clearly arranged, making it easier to perform routine inspections and maintain the equipment in its normal operating condition.
Poor maintenance leads to increased frequency and reduced production efficiency.
Equipping your machine with an efficient chip disposal system, such as a chip conveyor, not only improves product quality but also makes maintenance work more efficient.
Additionally, preventing coolant and cutting chips from entering the machine room of a machining center is an important factor that is directly linked to maintainability. Preventive maintenance can prevent equipment from being shut down for long periods of time.
3. Machining centers that support automation
Sugino Machine manufactures and sells automation systems for machining centers.
Sugino Machine can handle all the complicated and wide-ranging setup of automation systems, from manufacturing our own machining centers to teaching the robots that load and unload workpieces, and setting up workpiece transport devices such as conveyors. Utilizing the experience and know-how we have gained from providing automation systems for machining centers over many years, we provide customers with the optimal automation system.
Furthermore, poor machining accuracy and equipment stoppages, which are major obstacles to the introduction of automation, are often caused by cutting chips. Sugino Machine’s machining center, the SC-V40a, is equipped with thorough measures to prevent cutting chips and was developed to be the ideal machining center for automation, without equipment stoppages. Furthermore, with a width of 1,440 mm, it is one of the smallest in the industry for a #40 machining center, yet has a wide machining area, allowing a wide range of machining to be performed with just one machine. This machining center is truly ideal for automation, as it can achieve both high-mix production and long-term automatic operation.
Sugino Machine’s Strengths
- Robot teaching and setup are also carried out by Sugino Machine.
- Sugino Machine can also handle the setup and linkage of transport equipment.
- Sugino Machine provides all the jigs and programs required for automation.
- All communication regarding launch can be completed by Sugino Machine alone!
- Our specialized department also provides thorough after-sales service after delivery!
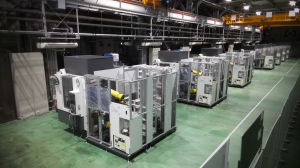
Strengths of the small machining center “SC-V40a”
Slim #40, perfect for automation
The compact size of the machine width of 1,440 mm and the rigidity of the No. 40 spindle make it possible to machine a wide variety of workpieces. This enables automation of multi-product production.
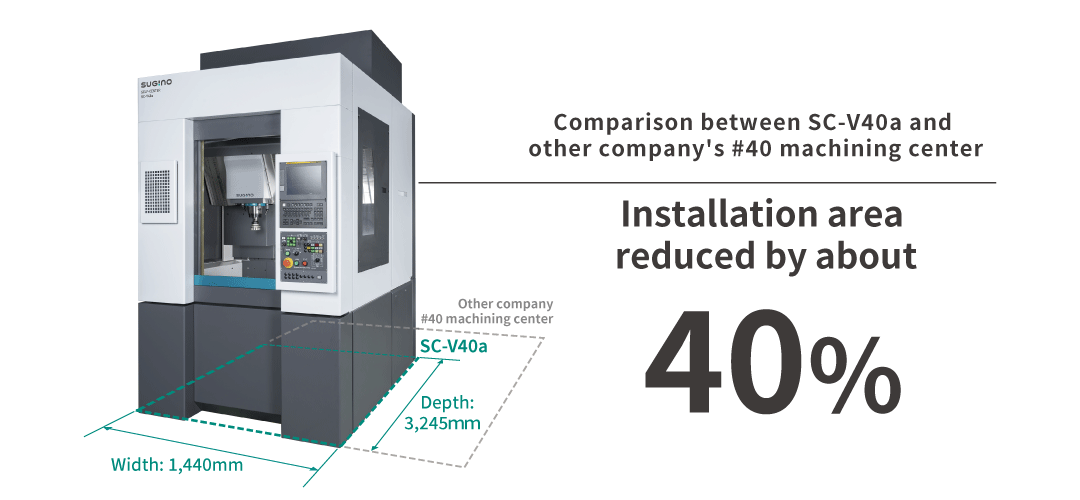
Structure that thoroughly removes chips
A center trough structure is used to thoroughly remove chips from inside the machine by allowing coolant to flow at a large rate throughout the machining chamber.
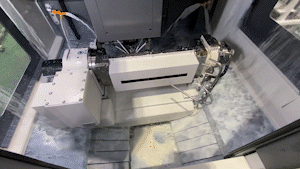
Wiring and piping-free design that does not stop equipment
The machine room is designed without wiring or piping, preventing equipment stoppages due to chip buildup and damage to wiring and piping.
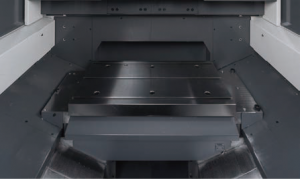
Click here for details on the “SC-V40a” machining center, which is ideal for automation.
4. Proposals that contribute to automation
Sugino Machine not only manufactures and sells automated machining centers, but also a variety of other equipment that solves the problems associated with automation and labor saving.
Proposal 1: Liquid-borne micro-contamination and oil removal unit “JCC-HM”
When a machining center continues to operate, fine cutting chips and lubricant oil carried over from the previous process accumulate in the coolant, causing various adverse effects.
Regular cleaning and coolant replacement are required, which requires manual work. By installing the JCC-HM, a micro-contaminant and oil removal unit in a machining center, it is possible to keep the coolant clean, reducing the maintenance work and enabling stable, long-term unmanned operation. It also reduces the frequency of coolant replacement, significantly reducing the cost of replacing coolant.
Proposal 2: Deburring tool holder/spindle motor “BARRIQUAN”
When machining die-cast or cast parts, the intersection of the machining surface and the casting surface is determined by the precision of the casting, so there is a large variation in dimensions and deburring must be done by hand. The floating mechanism of the clipper makes it possible to follow the cutter along the workpiece, making it possible to remove burrs uniformly even with machines or robots.
Proposal 3: Modular parts washer “JCC-Module”
In parts processing, cleaning is carried out before and after each process to remove processing oil, cutting chips, dust, scale, etc.
The modular parts washing machine “JCC-Module” uses “swing targeted cleaning” to perform overwhelmingly high-precision cleaning and deburring in a short amount of time. In addition, by simply selecting and combining the modules required by function, from cleaning and drying to transport, you can create the optimal automated line for your needs.
Proposal 4: Vacuum dryer “EVADRY”
After cleaning, moisture remaining on workpieces is often dried manually using air blowers. However, it is difficult to completely dry the workpieces using air blowers, and the working environment is poor due to moisture scattering and noise generation.
The “EVADRY” vacuum dryer uses a vacuum to evaporate moisture at room temperature, completely drying even moisture deep inside the workpiece. Not only does it eliminate the need for manual drying, it also improves the work environment. In addition, vacuum drying consumes much less power than air blowing, so by replacing air blowing with vacuum drying, power consumption and labor costs can be significantly reduced.