JCC 104 HYBRID : Deburring Parts Washing Machine
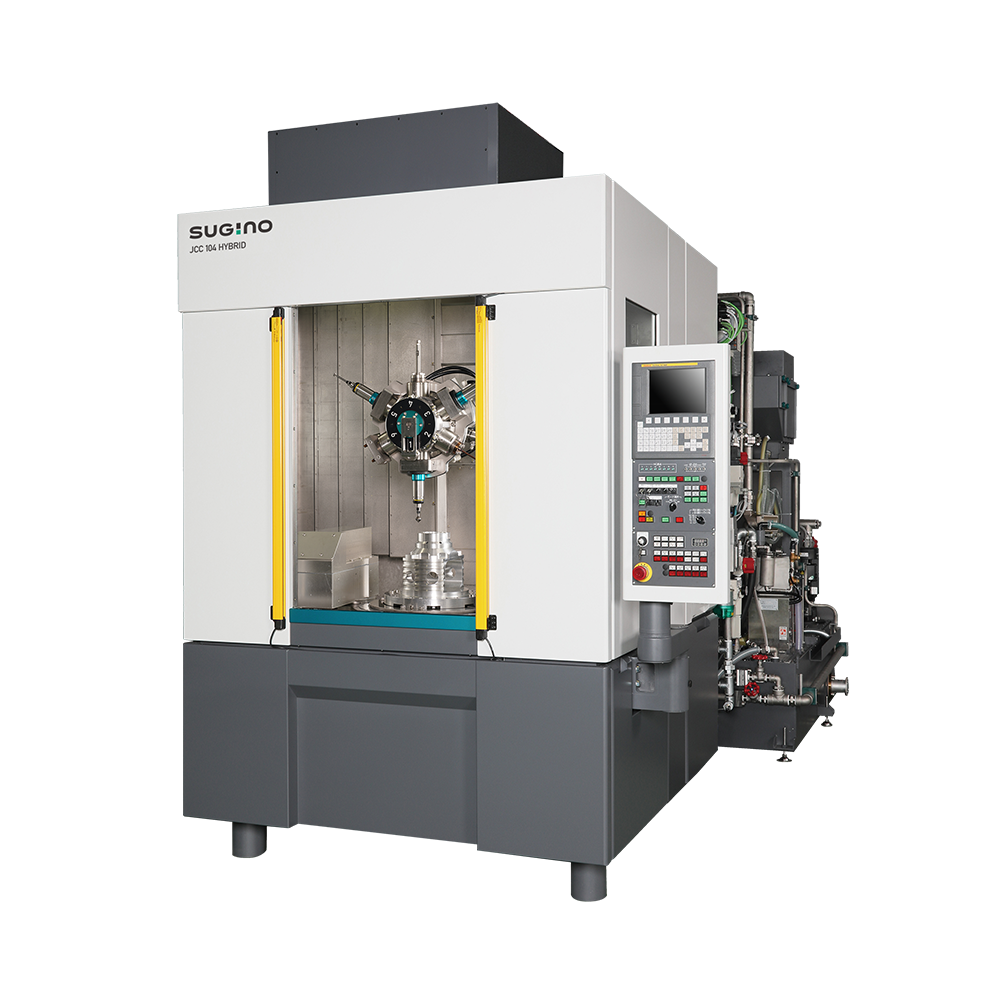
JCC 104 HYBRID
The best-selling parts washing machine “JCC” is equipped with a high-speed spindle for deburring, “BARRIQUAN,” and a hollow two-axis tilting rotary table.
This machine integrates the deburring and washing processes into one unit, effectively reducing equipment costs and installation space while thoroughly eliminating burrs from metal parts!
Product introduction video
Product introduction VR
Please view in full screen mode using the button at the bottom right of the screen.
Features
Burrs are removed completely using radial floating processing.
The JCC dedicated model features a high-speed spindle motor ‘BRQ’ equipped with a radial floating mechanism, capable of up to 20,000 min-1. For thick burrs at the base after cutting and parting lines that occur on cast components, which are difficult to remove with high-pressure water alone, the BRQ can be used as a finishing step after high-pressure water burr removal, enabling effective deburring from the root.
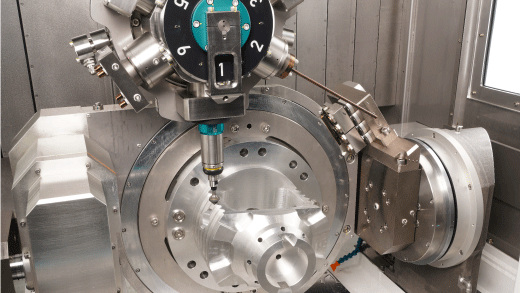
High-pressure water breaks burrs that cannot be reached by tools
High-pressure water deburring targets and breaks burrs that occur in areas inaccessible to tools, such as cross holes, deep holes, and step sections. The injection pressure is controlled by NC and can be increased up to 50 MPa. By adjusting the pressure according to work material, burr shape, and size, it is possible to minimize damage to the base material while removing only the burrs.
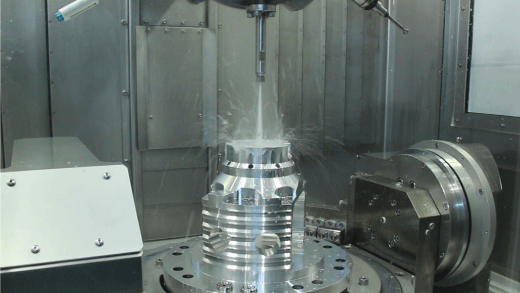
Accessible to all surfaces of the workpiece!
Equipped with a newly developed two-axis tilting rotary table with a central hole, designed for deburring and washing all surfaces of the workpiece.
Indexing five-axis control allows for deburring on all surfaces of the workpiece, including the mounting surface.
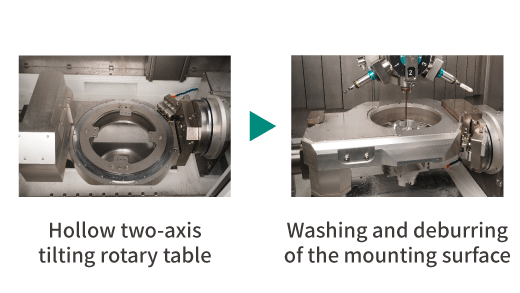
Consolidation of deburring and washing processes improves productivity.
The deburring process is often carried out manually, requiring significant time and costs.
This machine consolidates high-precision deburring and washing in a single unit, contributing to automation and labor reduction, thereby enhancing productivity.
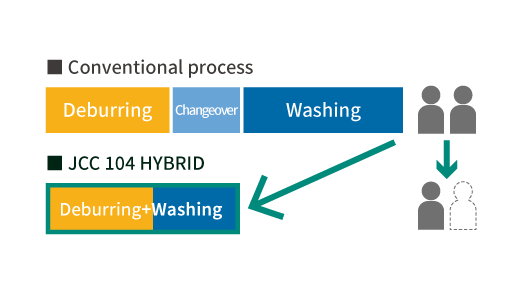
Easy operation with CNC control
Controlled by an NC device, it can be operated using well-known G-code. Unlike robots, it does not require complex teaching or special skills or qualifications, making it accessible for anyone to use.
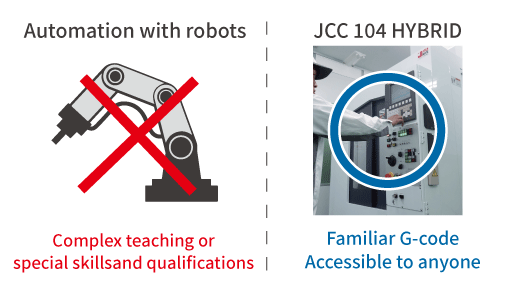
The energy-saving package “JCCeSmart” is installed
The energy-saving package ‘JCC-eSmart’ is standardly equipped, optimizing the power of the high-pressure water generation pump, which consumes the most electricity in parts washing machines, significantly reducing energy consumption.
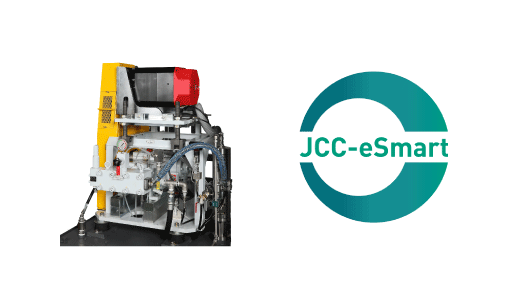
Case study
Deburring of the valve cross hole section
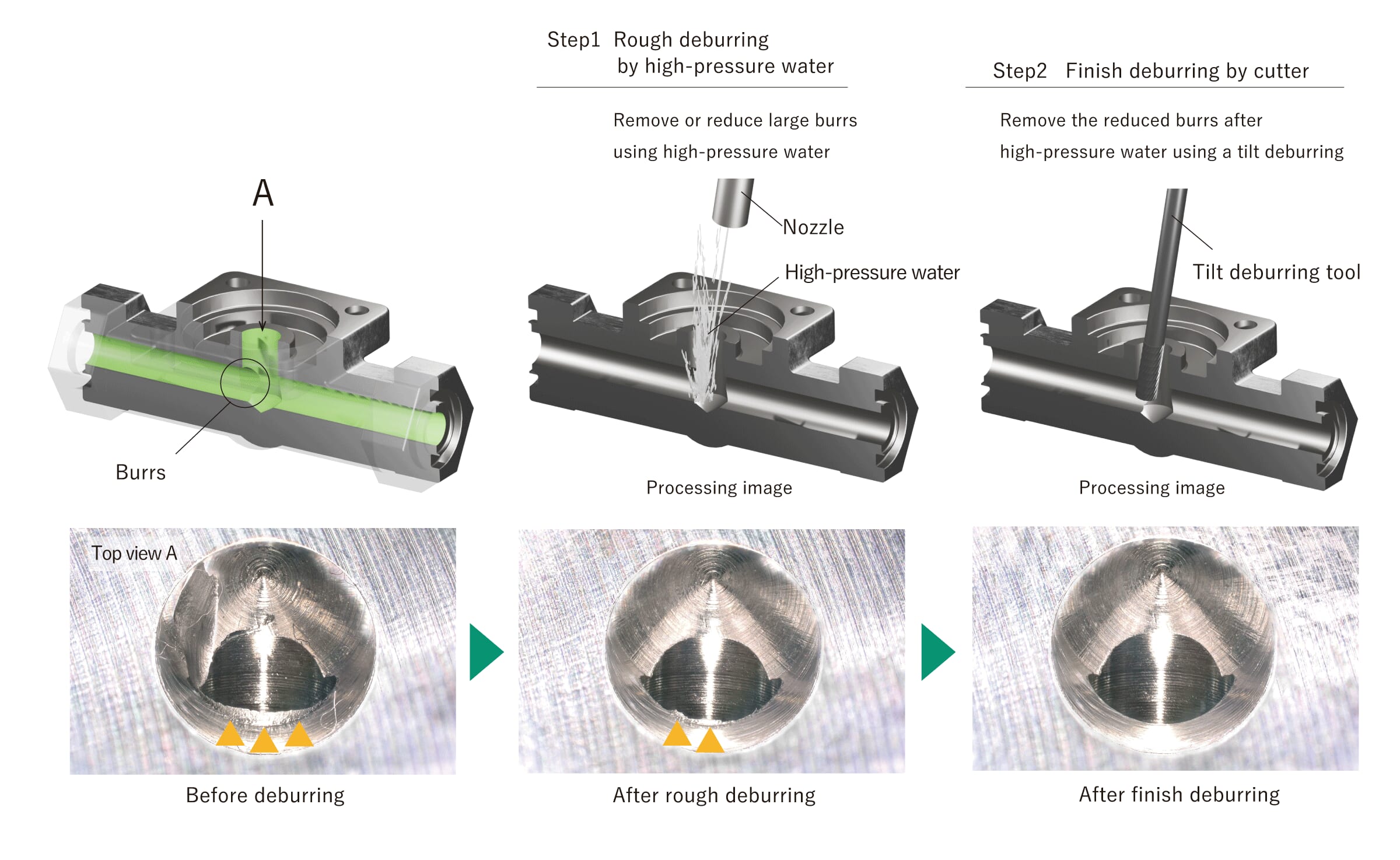
Specification
Working Pressure | Max. 50MPa |
---|---|
Flow Rate | Max. 29L/min |
Spindle Speed | Max. 20,000min-1 |
Stroke | X: 750 mm, Y: 500 mm, Z: 500 mm |
Rapid Traverse Rate (X,Y,Z axis) | 60m/min |
Number of Tools | 6 |
Control Device | FANUC 0i-MF Plus |
Machine Dimensions (equipment body) |
W 1,600 × D 2,700 × H 2,500mm |
Machine Weight (equipment body) |
4,300kg |