Strengths of Sugino Water Jet
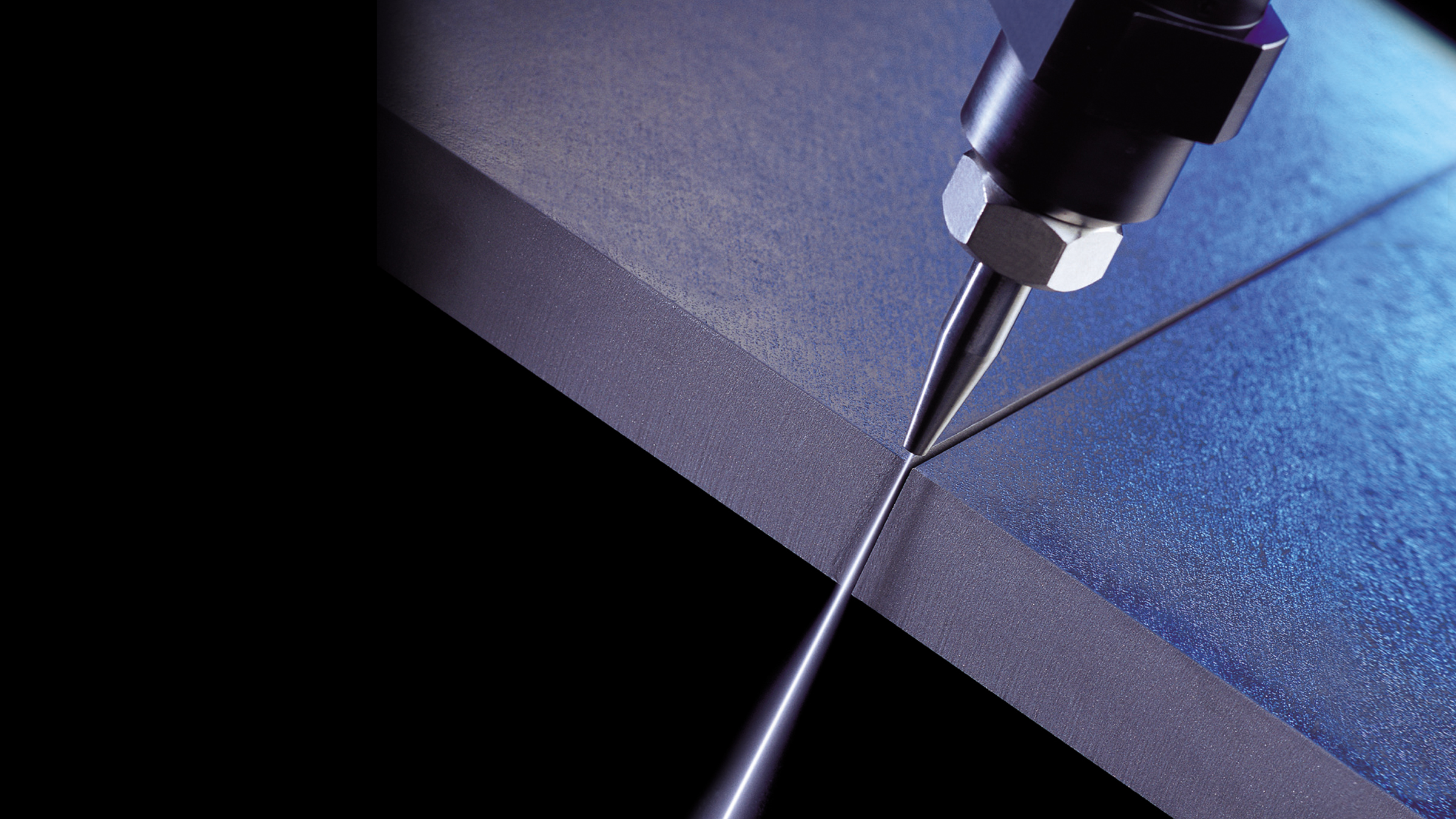
Since developing our first high-pressure pump in 1964, Sugino Machine Limited has been improving and promoting the advantages of water-jet technology for over 50+ years.
The Water Jet Cutter, a Sugino flagship product, is used in a wide range of industries, cutting many types of materials, including composites, metals, resins, ceramics, rubber, fabrics, and food.
What is a Water Jet Cutter?
Water jet cutting is a method that pressurizes water up to 600 MPa (approximately 6,000 air pressure) and injects it through a small-diameter nozzle.
Utilizing a high-speed, high-density narrow stream (water jet) with ultra-high pressure energy, it can cut and process any type of material without thermal effects.
There are two types of Water Jet Cutters: “water jet cutting,” which processes with only water, and “abrasive jet cutting,” which processes by mixing an abrasive into the water-jet stream.
Comparison with other methods
The water jet cutting method processes any material without thermal effects.
Processing type | Materials | Effects on materials | Processing precision | Processing speed | Material thickness (Max.) | |
Water Jet | Cutting | All | – | Relatively good | Relatively fast | -approx.300mm |
---|---|---|---|---|---|---|
Gas | Fusion cutting | Metals | Heat | Normal or poor | Slow | -approx.500mm |
Plasma | Fusion cutting | Metals | Heat | Relatively good | Fast | -approx.180mm |
Laser | Fusion cutting | Metals | Heat | Relatively good | Fast | -approx.25mm |
EDM | Fusion cutting | Conductive | Heat | Fairly good | Very slow | -approx.250mm |
Cutting Principle
Water Jet Cutting
For Soft Materials
Cutting using water only is suitable for soft materials such as rubbers, foam, and non-woven fabrics

Abrasive Jet Cutting
For Hard Materials
Cutting by mixing an abrasive into the water-jet stream is suitable for hard materials such as metals and glass.
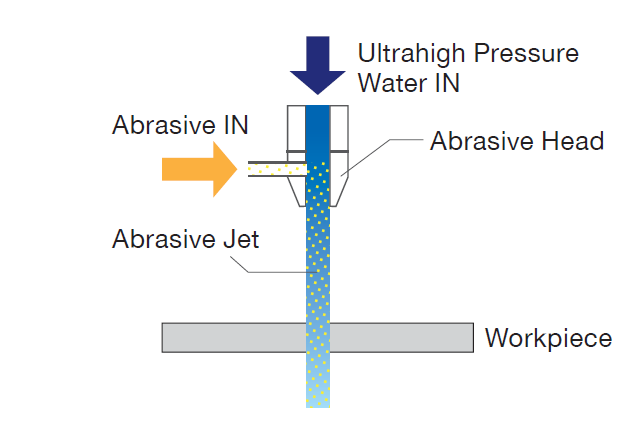
〔Applications/Materials〕
Automobiles (roof materials, floor materials, instrumental panels, acoustic materials, bumpers), plaster boards, carpets, leathers, cork boards, rubber packing, corrugated cardboards, urethane rubbers, felts, foams, resins, paper products, sushi, frozen foods, meats, snacks, etc.
〔Applications/Materials〕
Stainless steel, copper, aluminum, magnetic materials, CFRP, titanium, duralumin, marbles, tiles, glasses, inconel, hastelloy, nickel, ceramics, etc.
Features
The Water Jet Cutter processes a wide range of materials.
The following are examples of the superb advantages with various processing samples.
Retention of the cross section shape
The cross section shape of the parent material can be kept by non-contact processing.
Material: Stainless Steel / Thickness: 20mm
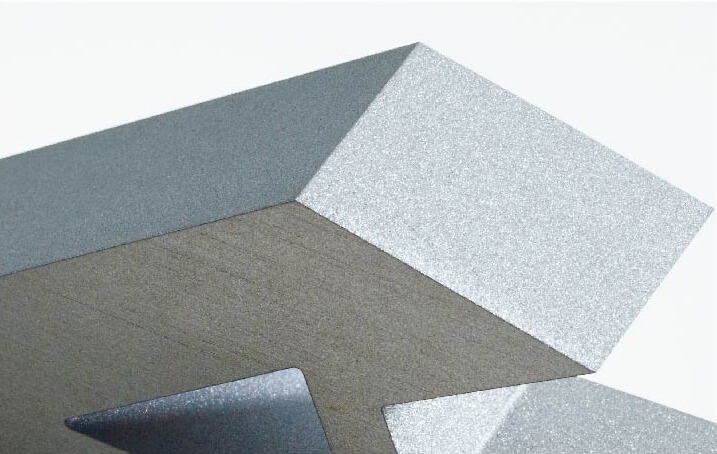
Precision processing
Precision processing is possible with a minimum cutting width of 0.3 mm.
Material: Stainless Steel / Thickness: 1mm
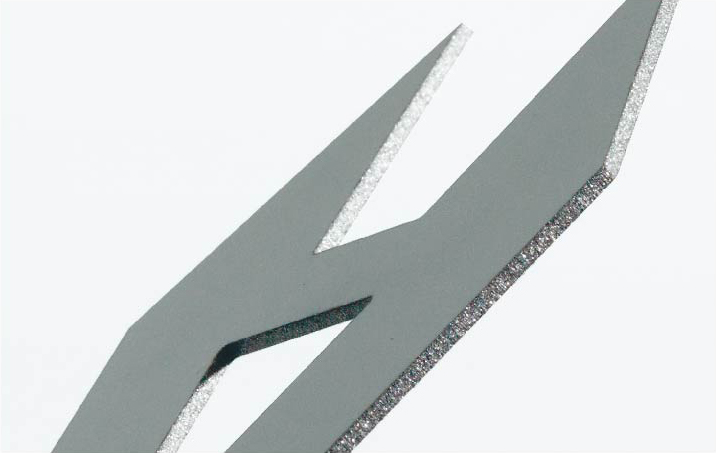
Three-dimensional processing
Processing of three dimensional shapes is possible by inclining the nozzle.
Material: Foaming Material / Thickness: 30mm
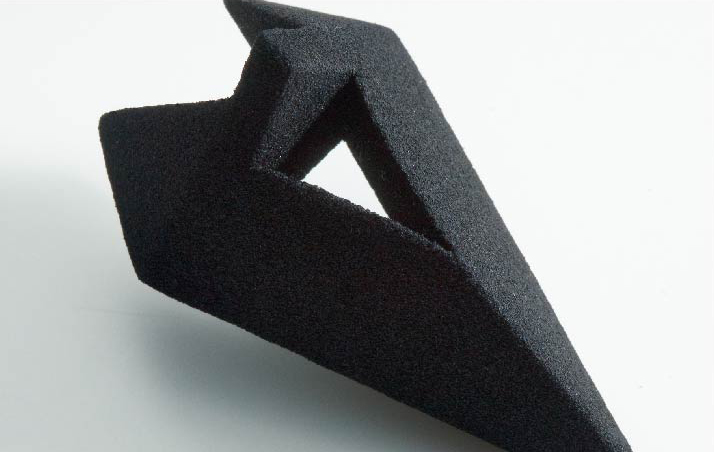
Applicable to various materials
Deformation, transformation, and residual stress are prevented by cooling effects of water, making this method applicable to a wide range of materials.
Material: Copper / Thickness: 20mm・50mm
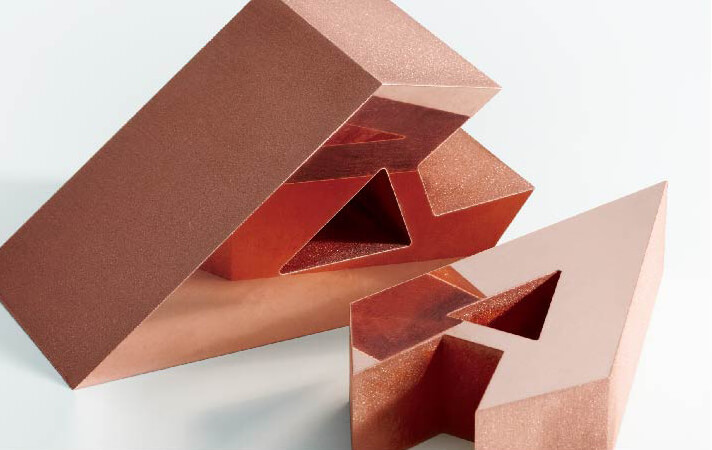
Suitable for processing of fragile or compound materials
As a result of the high energy density and localized processing, Water jet cutting is the optimum process for cutting fragile or compound materials.
Material: CFRP / Thickness: 2mm
Material: Glass / Thickness: 19mm
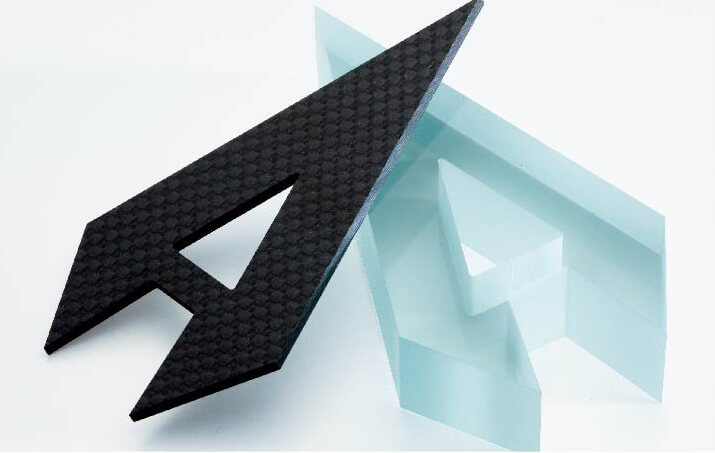
Cutting into any shapes
Materials can be cut starting from any desired position because of the piercing capabilities of the water stream.
Material: Nylon / Thickness: 10mm・20mm
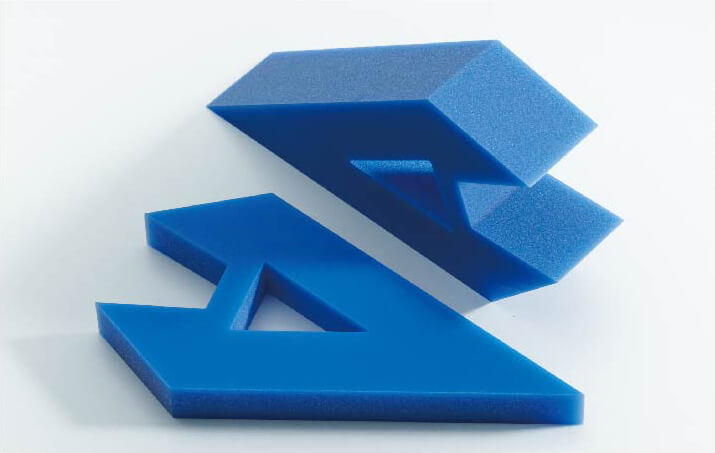
Applicable to thick materials
A deep effective processing distance allows materials that are 100 mm or thicker to be cut.
Material: Aluminum / Thickness: 50mm・100mm
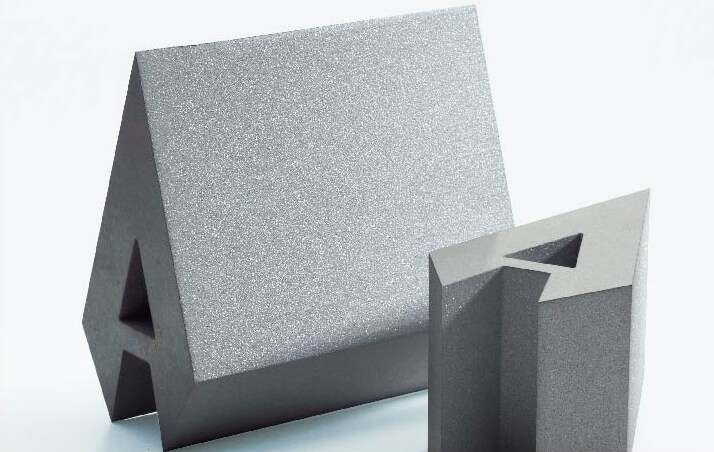
Clean environment
No dust is created from the cutting process, providing a cleaner, safer working environment.
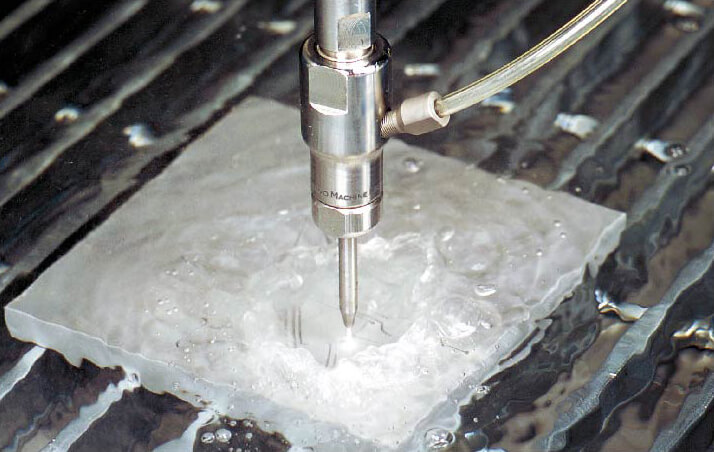
Strengths of Sugino Water Jet
Outstanding technology recognized by the world’s leading manufacturers.
Technology (Accuracy)
Three-dimensional shape processing
The nozzle can be controlled at high precision from 0-360° in the C-axis and ±90° for the A-axis. This capability allows cutting of
three-dimensional shapes. (5-axis control specification)
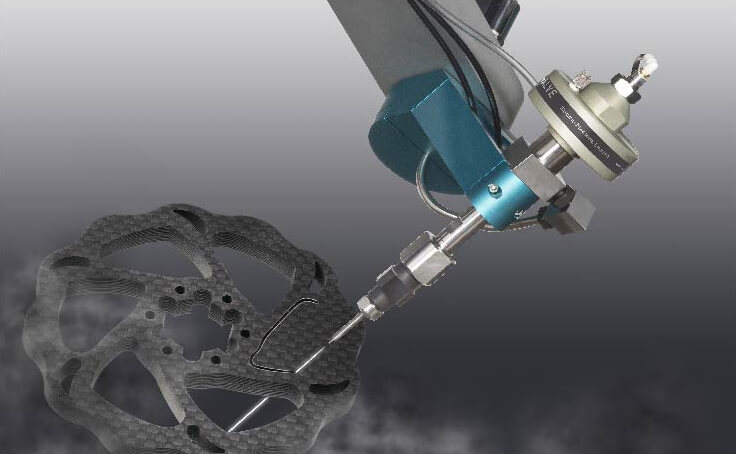
Perpendicular cross section
Incident angle of the nozzle is a processing characteristic of water jet cutting that can be automatically controlled in order to prevent
sloping of the cross sectional area. This feature simultaneously helps improve the processing speed and creating a more precise cut. (5-axis control specification)
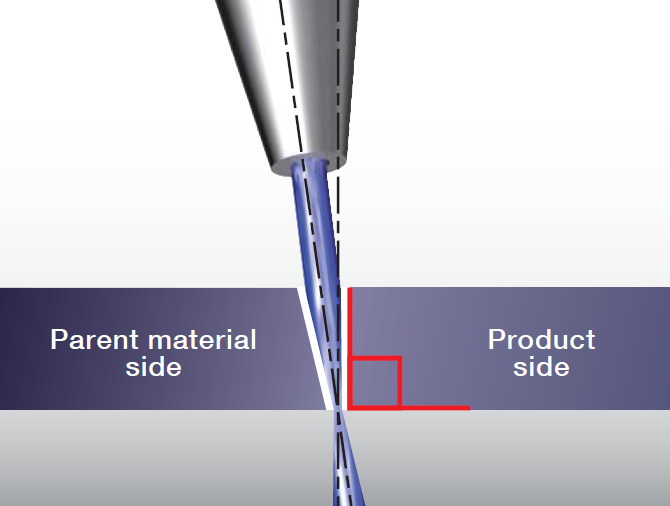
Realization of further precision processing
Extremely narrow cutting widths down to 0.3 mm can be achieved using the newly developed extra narrow abrasive nozzle. One key advantage of a narrow water stream is improved sur face finish. (KATANA 2)
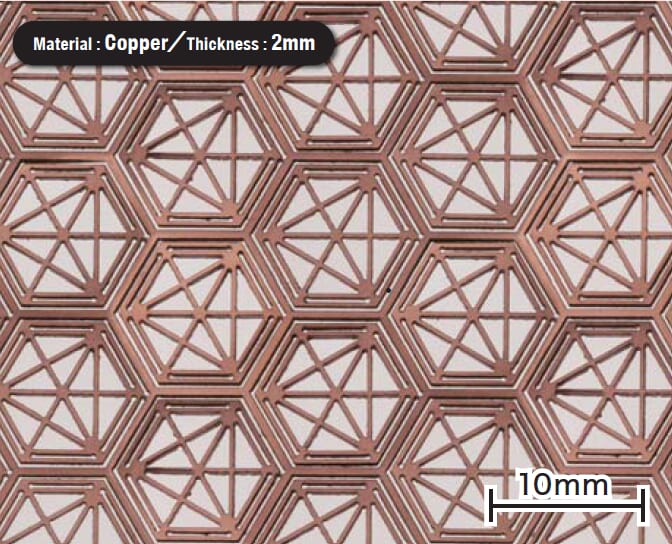
No “Drag”
Drag is a processing characteristic of water jet cutting at high speed that is automatically controlled to help prevent defective corner shapes. (5-axis control specification)
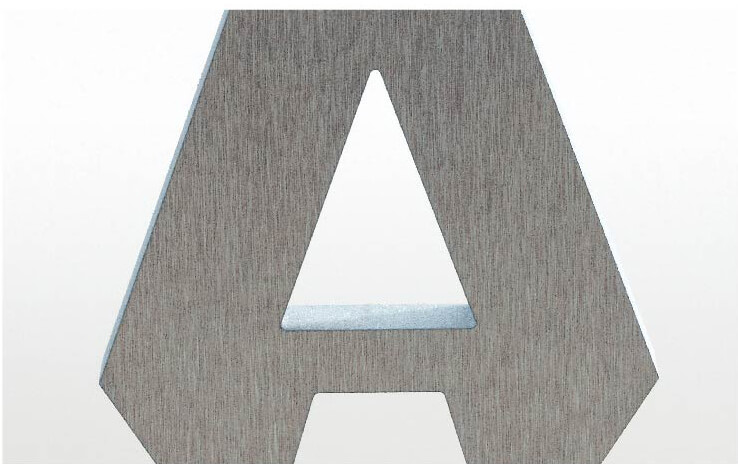
Practicability
Sugino Jet Processor
Know-how cultivated over years is compiled in a database.
Anyone can perform high precision processing easily by entering information and values such as work material, thickness, and pressure.
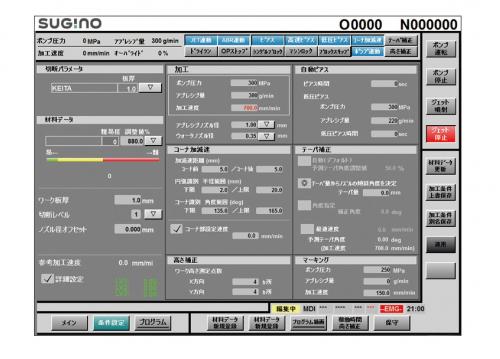
Processing tip adjustment
A function to measure an error between the processing data and the actual work and automatically correct the nozzle. This function is useful when replacing the nozzle.
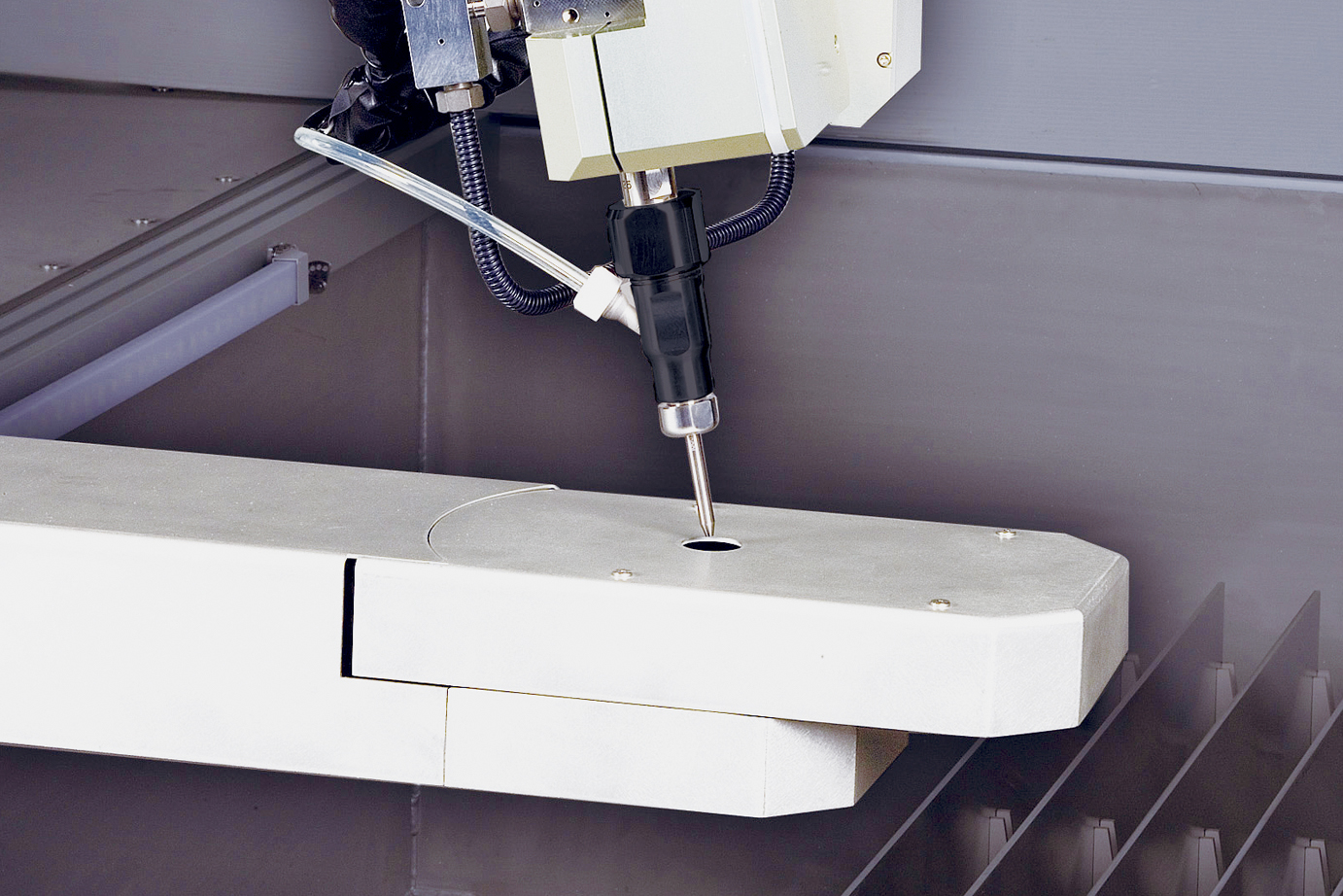
Nozzle height adjustment unit
A unit to measure and adjust the distance between the work and the nozzle with laser or a contact-type sensor. Settings can be changed easily.
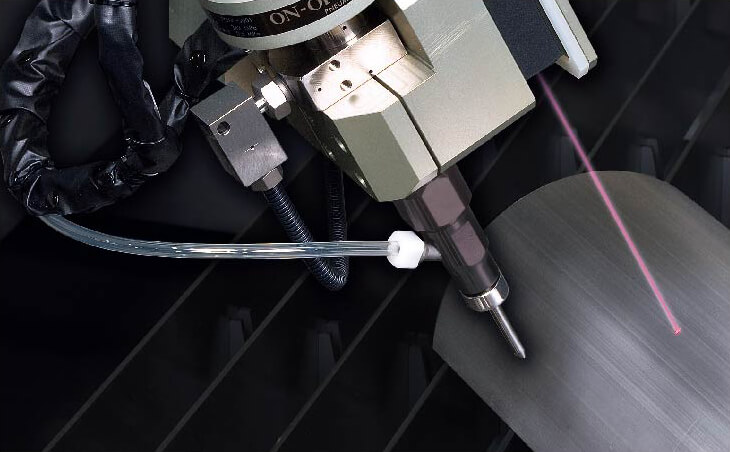
Automatic piercing
A function to automatically adjust the pressure and abrasive supply amount when processing afragile material or creating multiple holes.
With this function, chipping or delaminating the workpiece is prevented.
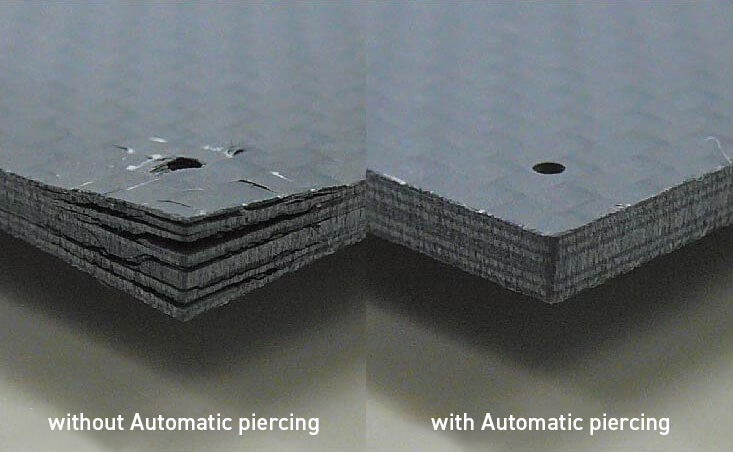
Abrasive automatic supply device
This device supplies a stable and consistent amount of abrasive material to the cutting system. Adjustments are easily done according to the material type and thickness.
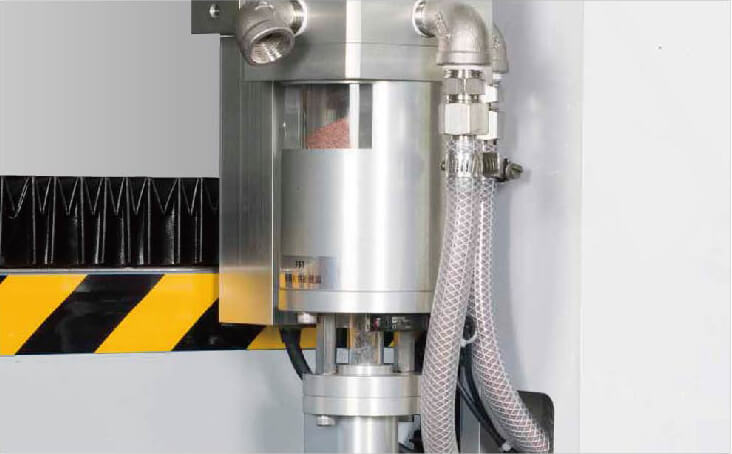
Equipped with IoT function for visualization of operation status
The system remotely controls machine operating status, monitors for signs of abnormalities, and manages consumable parts to ensure effective production.
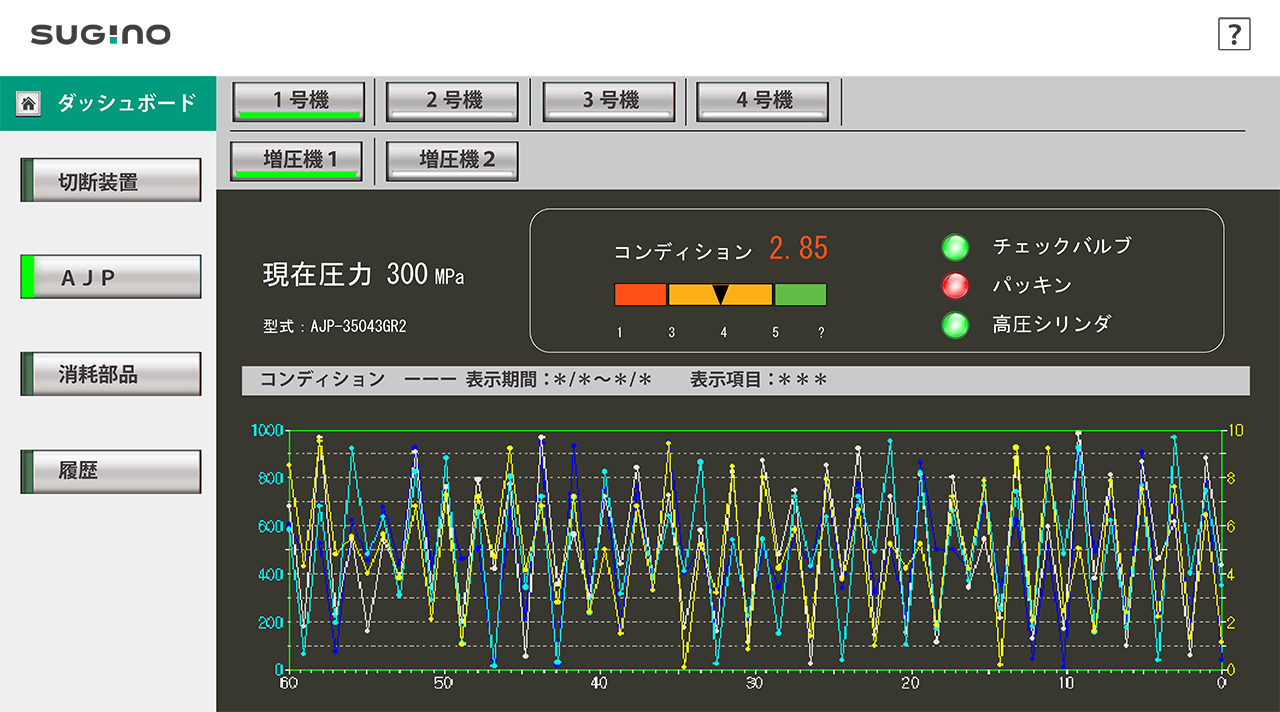
Abrasive collecting device
This device collects abrasives and scraps that have accumulated in the catcher tank after processing.
With this collection system, the time needed for daily cleaning is reduced.
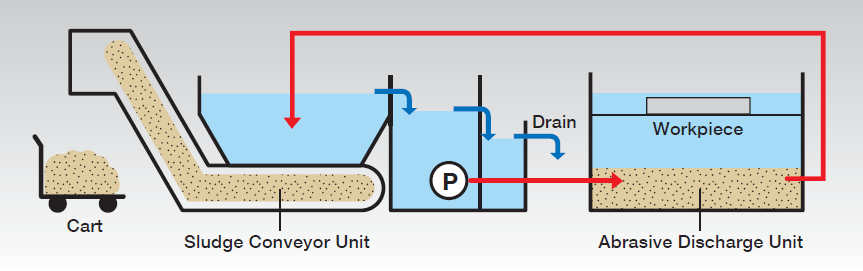
Water level adjustment mechanism
Cutting under water and cutting in air can be switched quickly without supplying or draining water.
Scattering of water is extremely small with cutting under water, and noise is kept low. (Compatible with open catcher)
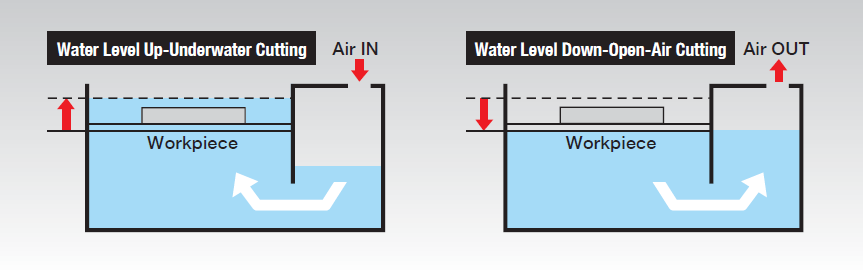
Catcher unit to match the purpose
Three types of water jet catching units are available with low noise and ease of maintenance considered for each design.
Jet Catcher
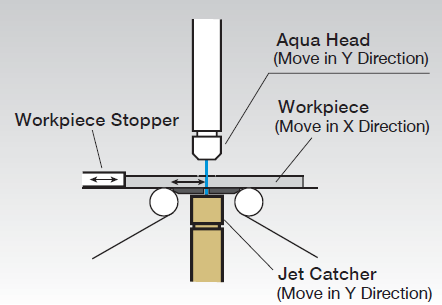
Slit Catcher
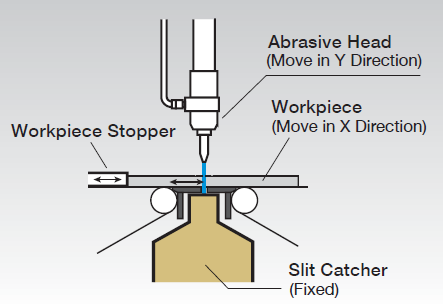
Open Catcher
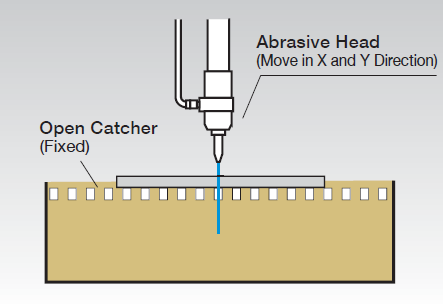