JCC Series (Jet Clean Center) : High Pressure Water Jet Deburring and Parts Washing Machine
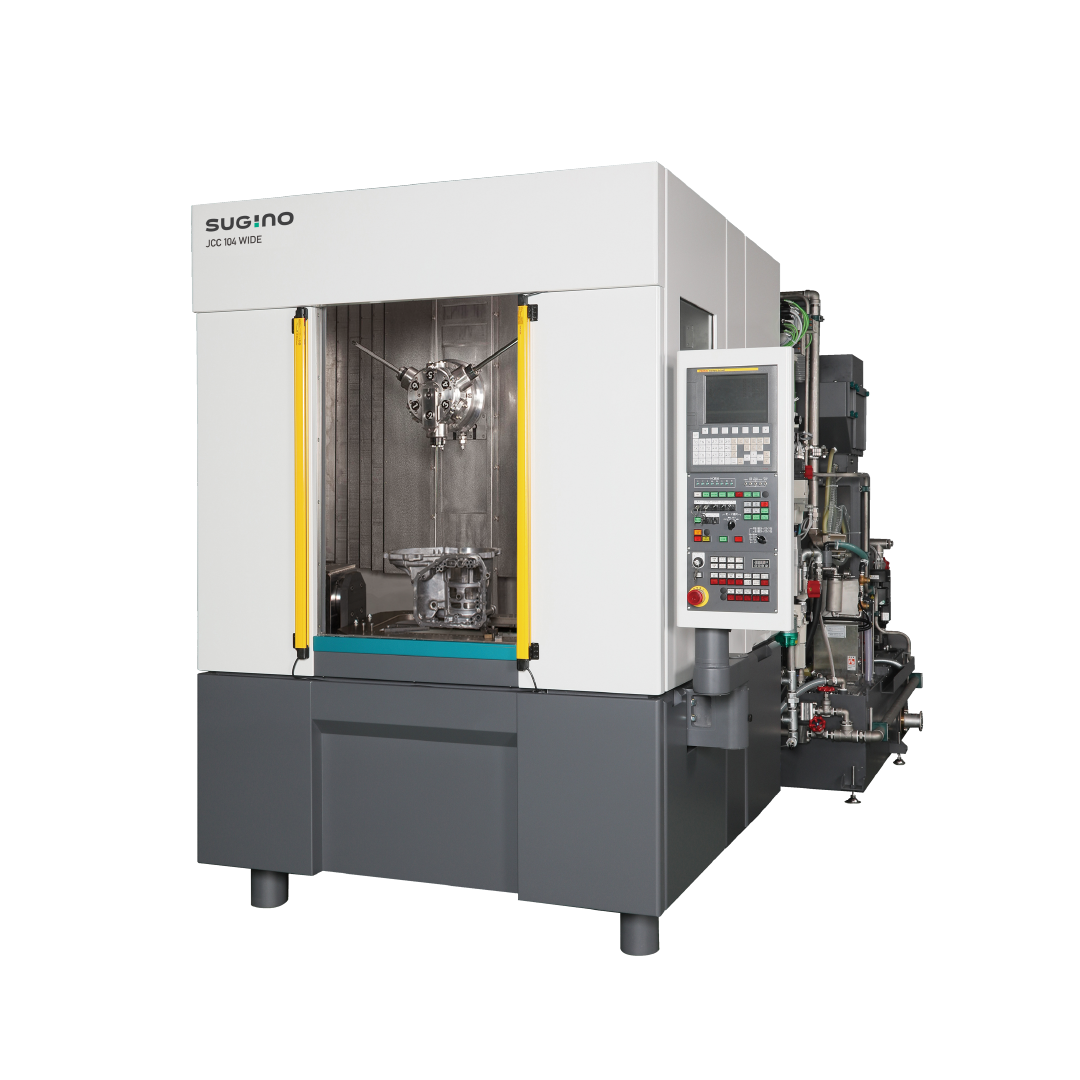
JCC Series
Explore the JCC (Jet Clean Center) series for the deburring and cleaning of all parts with high pressure water up to 245MPa.
Since the JCC’s inception in 1998, it has been highly regarded both in Japan and overseas. To date, we have delivered more than 6,000 JCC machines in more than 30 countries around the world.
As a leading supplier of deburring and parts-washing machines, we solve customers’ problems in all aspects of quality, safety and environment.
High-pressure targeted washing
Water is pressurized up to 245 MPa and injected by CNC control.
Without relying on chemical properties, the impact force of the injection effectively removes burrs and chips generated on various components.
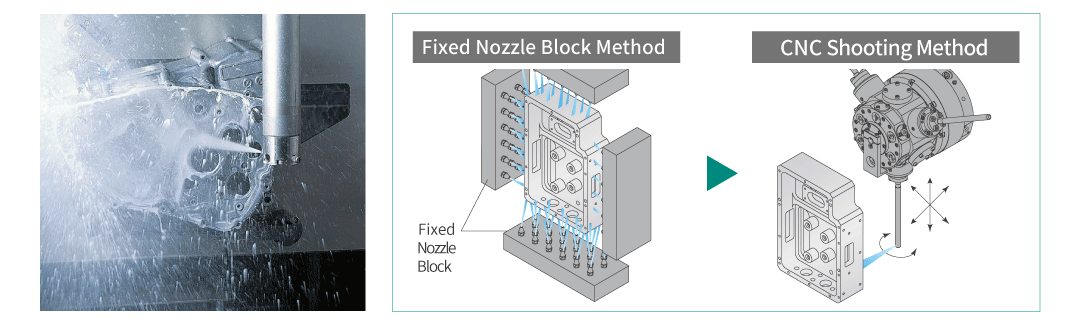
Features of High-pressure targeted washing
1. Effecive
High-pressure water, with its high velocity, removes chips instantly and effectively, providing stable cleaning quality.
2. Energy Saving
The combination of the right nozzles and targeted positioning saves time, energy and cost.
3. Flexible
The cleaning conditions can be freely changed through CNC programming, allowing for quick response to changes.
Submerged Cleaning
Submerged cleaning is critical for internal passages of a workpiece. The synergistic effect of the U-Jet high pressure jets and cavitation creates a vortex, completely removing residual chips from hard to reach places within a part. Even workpieces with complex geometry can be effectively cleaned.
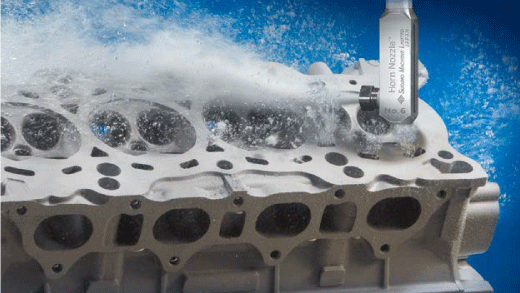
Features of underwater washing with U-Jet
When high- pressure water is sprayed underwater, cavitation (fine bubbles) is generated.
When these bubbles collapse, an impact pressure of several GPa is generated, and the power is used for cleaning.
Open-Air Deburring and Washing
High cleaning effect in and around the area where high-pressure water collides.
Ideal for parts with many taps, For deburring crossed holes and deep oil passage holes.
■ ex. Transmission case, gearbox case
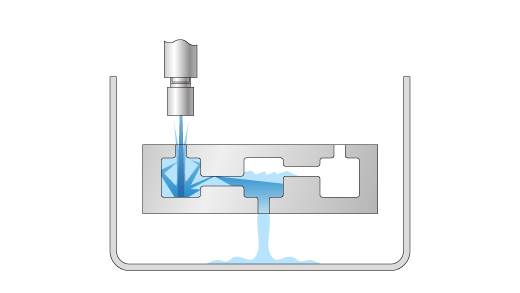
Submerged Washing
The vortex cleans the entire inside of the workpiece.
Ideal for removing chips and sand from complex-shaped parts
■ex. Construction machinery / hydraulic parts, cylinder head / block
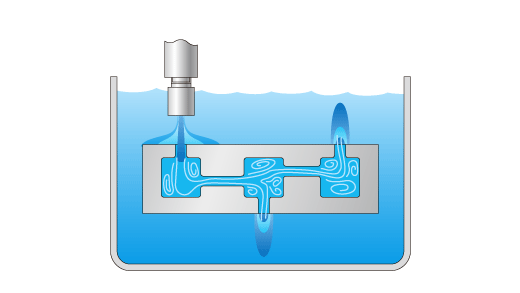
Features of JCC Series
Dramatically Reduce Cycle Time
By improving the performance of the XYZ column and circular table, the cycle is higher than that of the conventional machine.
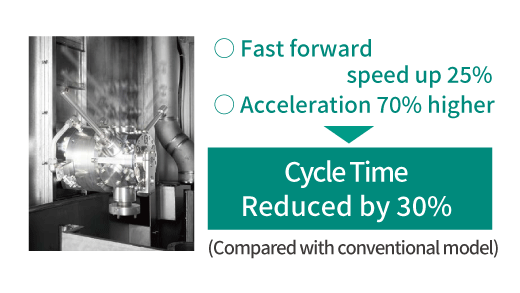
Reduce CO2 Emissions by 50% or more with eSmart
The energy-saving package “JCC-eSmart” is installed as standard.
By washing under optimal conditions tailored to the target, excessive power generation is minimized, significantly reducing power consumption and CO2 emissions.
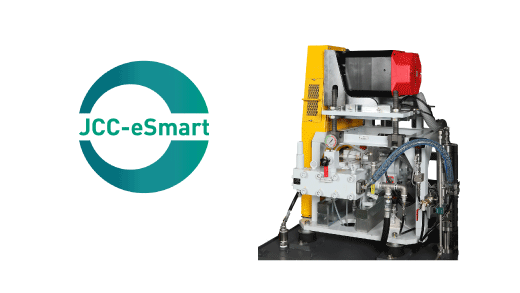
Advanced Air Blow Option
The 2 station type drying option now features a robot air blowing system. A robot with an air nozzle moves around the workpiece freely to achieve high-precision, targeted drying.

Supports underwater and open air cleaning
Both submerged and open air parts cleaning can be performed with one machine.(compatible models: JCC 403 U-JET, 421 UT). The optimal method can be selected based on the part geometry and workpiece specifications.
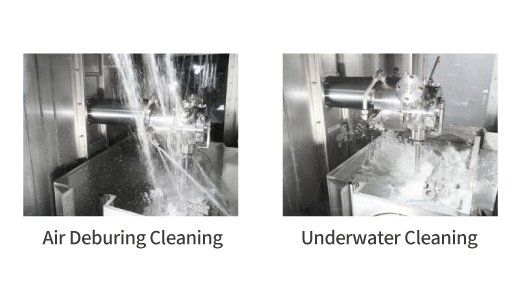
Target workpiece : air parts cleaning
Transmission parts, e-axle parts, ABS housing beake caliper, etc.
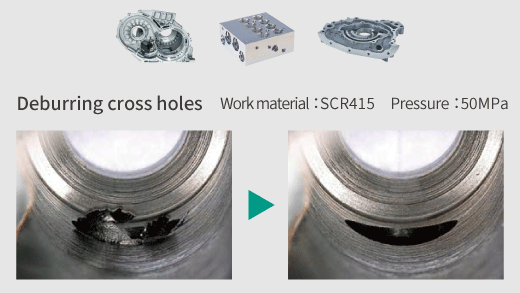
Target workpiece : Supports underwater
Cylinder head, cylinder block, hydraulic manifold, etc.
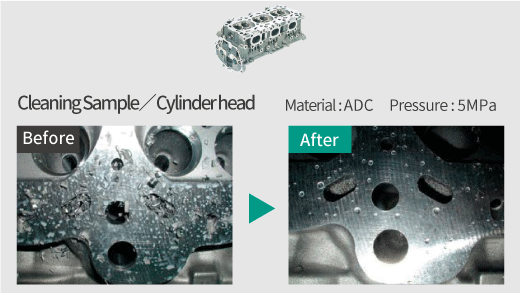
JCC 421 UT Introduction Video
Main Specifications
Line Up
We offer a variety of options to fit your deburring, parts cleaning, and drying needs. 1 and 2 station setups allow for muliple processes for faster cycle times.
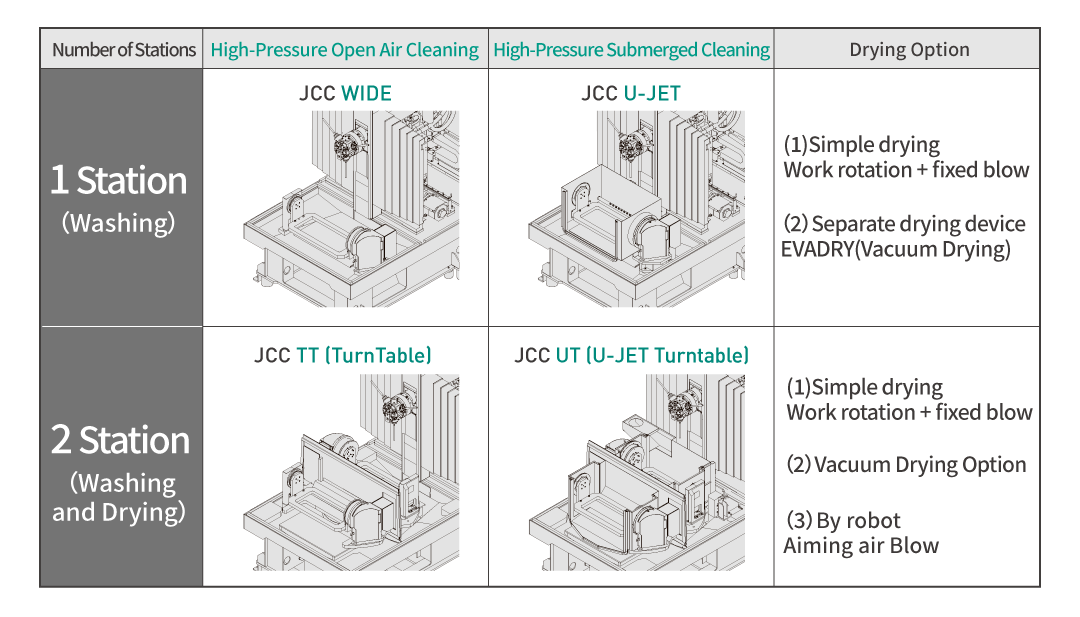
Specifications
JCC 104 WIDE | JCC 303 TT | JCC 403 U-JET | JCC 421 UT | |
---|---|---|---|---|
Model | JCC-W6750F | JCC-W6750TF | JCC-W6750UF | JCC-W6750UTF |
Working Pressure | Max. 50 MPa | |||
Flow Rate | Max. 29 L/min | |||
Stroke | X: 750 mm, Y: 500 mm, Z: 500 mm | |||
Rapid Traverse Rate (X,Y,Z axis) |
60 m/min | |||
Spindle Speed | Max. 1,000 min-1 | |||
Positioning Accuracy | 0.08 mm (full stroke) | |||
Repeatability | ± 0.05 mm | |||
Number of Tools | Max. 6 | |||
Tool Indexing Time | 0.5 s (random shortcut by CNC control) | |||
Machine Dimensions (Width x Depth x Height) |
1,600 × 2,700 × 2,500mm | 1,600 × 3,450 × 2,500 mm | 1,600 × 2,700 × 2,800 mm | 1,600 × 3,450 × 2,800 mm |
Machine Weight (equipment body) |
4,300 kg | 4,800 kg | 5,300 kg | 5,800 kg |
Control Device | FANUC 0i-MF Plus | |||
Power Supply Capacity (Standard Specifications) |
65 kVA | 72 kVA |