What is “Float Deburring”|A Method for Automated Deburring
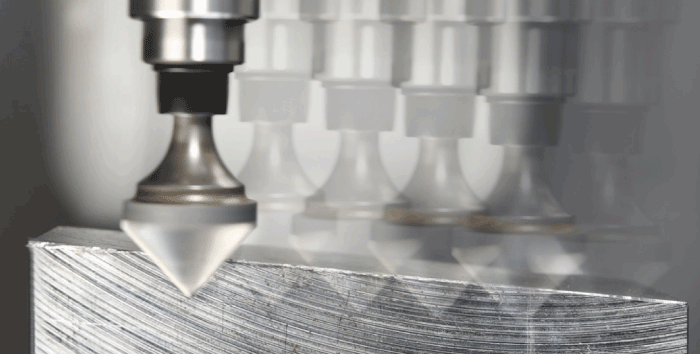
Protrusions formed during the processing of metal parts are called “burrs”, and the removal of these burrs is called “deburring”.
There is a growing need for mechanization and automation to address labor shortages, improve productivity, and eliminate hazardous work.
If you try to automate manual deburring with a machining center or robot, you may not get the deburring you are aiming for.
Causes include changes in the size and shape of burrs due to cutting tool wear, variations in workpiece dimensions, and mounting errors when fixing the workpiece. The “Float Deburring” solves these problems that stand in the way of automated deburring.
“Float Deburring” is a machining method that prevents overshaving and burrs from being left on the workpiece by aligning the tool with the shape of the workpiece using an attachment equipped with a floating mechanism.
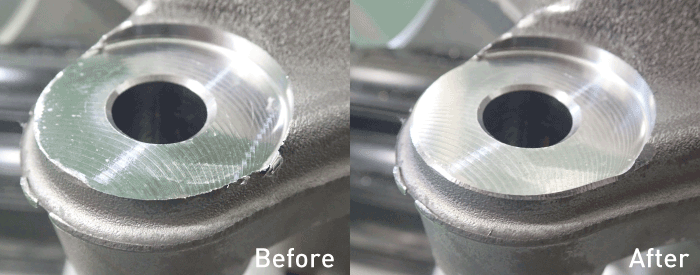
About Floating Mechanism
Attachments with floating mechanism
A floating mechanism is a structure that uses a spring or compressed air to press a tool against a workpiece at a constant pressure.
It may be built into a tool holder or spindle motor, or it may be an independent unit.
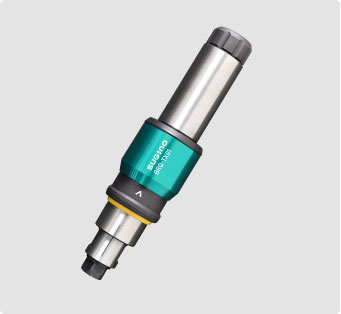

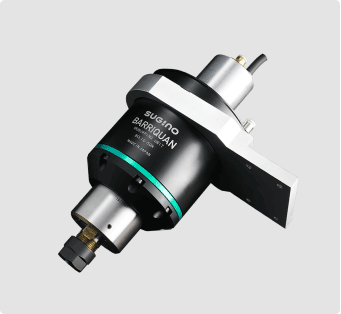
Types of floating mechanism
Axially floating type
The Axially Floating type is a mechanism that extends and retracts in the Z direction.
It is suitable for deburring the edges of workpieces and is often used to deburr the contours of castings and after machining.
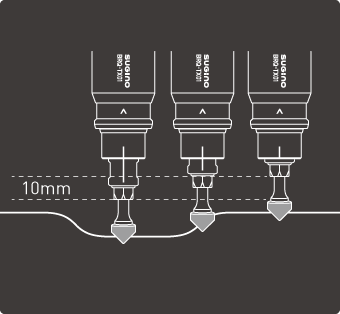
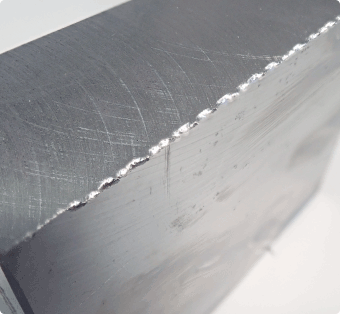
Tilting floating type
In the Tilting floating type, the tool is tilted to the workpiece.
Suitable for protrusions and burrs that occur on the “surface” rather than the edge of the workpiece.
It is often used for parting line removal of aluminum die castings, etc., and is mainly suitable for deburring by robots.
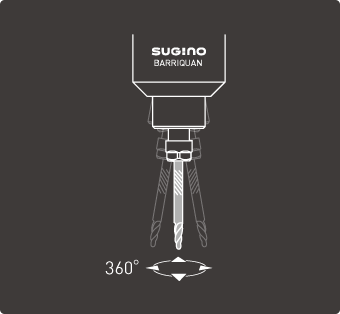
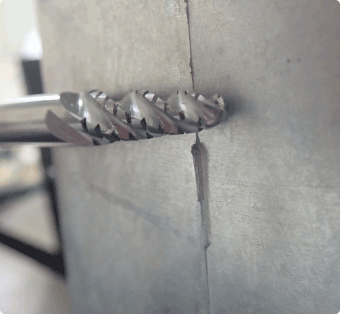
Role like the autonomic nervous system, which is responsible for human hunches and knacks
The biggest problem in the automation of deburring is the question of what will take care of the hunches, tricks, and judgments. Vision cameras, various sensors and software are the parts that correspond to human perception and brain, but they cannot process ambiguous information like humans.
In addition, because it must go through multiple processes of inputting information, computing, outputting, and running the machine, it is insufficient from the standpoint of speed in deburring, where high-speed processing is required.
Floating mechanisms work in areas that people are not aware of, like autonomic nerves, so to speak.
By directly receiving and reacting to ambiguous information, high-speed deburring, which cannot be achieved with sensors and software alone, is realized.
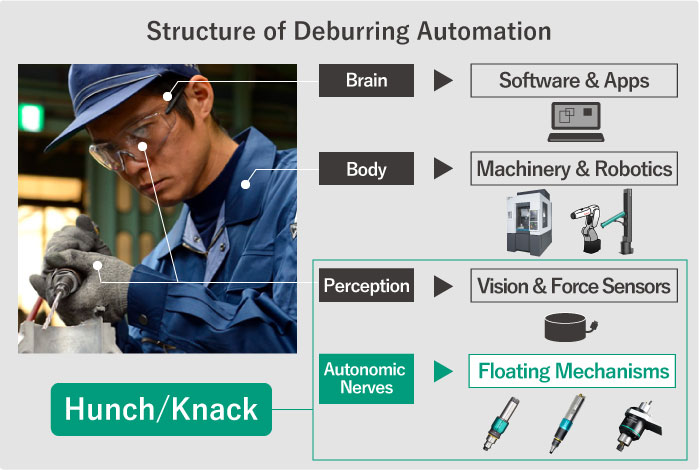
Indispensable for faster deburring
We often see people deburring with amazing speed and accuracy. However, deburring is characterized by the fact that it becomes instantly slower when mechanized.
To stabilize quality, the aforementioned problems (variation and ambiguous information processing) make it difficult to increase speed in terms of tool and machine protection.
However, there is not much time allowed for the deburring process, which is originally performed at high speed.
The floating mechanism can process while absorbing impact by constantly pressing the tool against the workpiece at a constant pressure.
Even if the relative position of the workpiece and machine changes or the size of the burr changes, the load and impact will not increase, thus enabling high-speed deburring.
Small articulated robot becomes a processing machine
Articulated robots are widely used to automate transport and non-contact tasks, but are not suitable for tasks that require rigidity, such as metalworking. (making them larger than necessary)
As mentioned above, a floating mechanism can soften the load and impact on the robot, enabling automation of deburring even with a small multi-joint robot with low rigidity.
The floating mechanism also reduces teaching work and compensates for inaccurate trajectories, making it an excellent match for robot deburring.
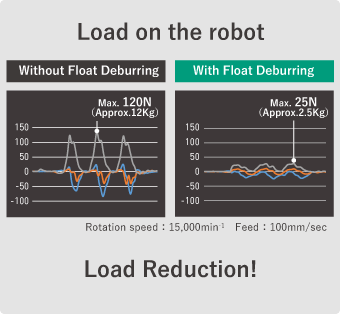
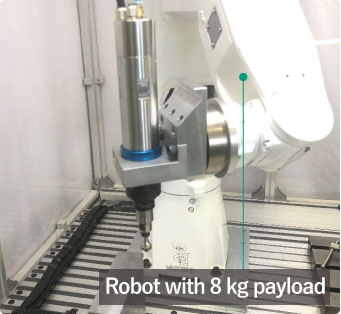
Mechanism for Tool to follow the Workpiece in Float Deburring
This section explains how the tool follows the shape of the workpiece in floating machining, preventing overshaving and burring of the workpiece.
Mechanism in which a tool follows a workpiece in axially floating type
It is the axially floating type floats vertically, but it follows the workpiece not only in the height (Z) direction but also in the horizontal (XY) direction.
Height direction (Z direction)
Even if the distance between the workpiece and the tool in the height direction changes, the tool stays with the workpiece due to the axially floating mechanism.
Horizontal direction (XY direction)
Even if the lateral distance between the workpiece and tool changes, the tool follows the workpiece due to the expansion and contraction of the floating mechanism.
However, since the contact position between the tool and the workpiece changes, the distance that can be followed depends on the size of the tool.
Mechanism in which a tool follows a workpiece in Tilting floating type
In the tilting type, a mechanism that tilts 360° acts as a cushion where the tool meets the workpiece when approaching from any direction, as in robot teaching.
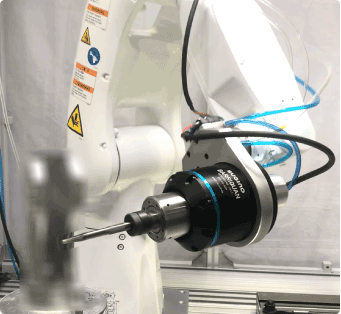
Suitable tools for Flaot Deburring
Tools suitable for axially floating type
Cutter: 90° angle at the tip is recommended
A conical carbide rotary bar with a 90° tip opening angle is suitable.
Use of sharp-edged cutters will shorten the life of the tool due to forces that prevent it from floating.
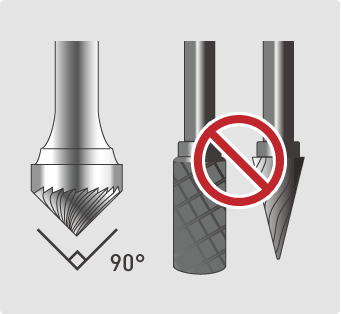
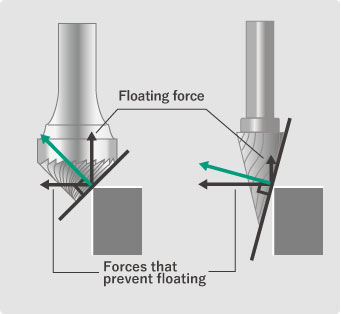
Cutter: the more blades, the better
A cutter with a large number of blades is suitable for floating processing.
If the number of blades is small, the finished surface will deteriorate.
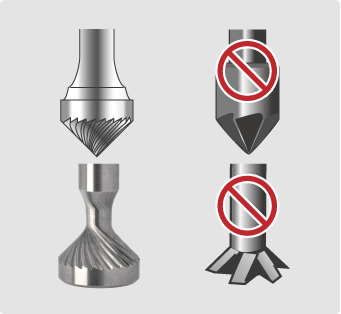
Brushes: bristles should have cutting power at the tips
If the burr thickness is less than 0.15 mm, it can be deburred using a brush.
The floating mechanism allows the tip to extend as much as it wears, enabling stable deburring.
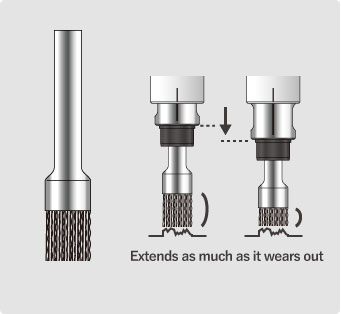
Tools suitable for tilting floating type
Tools suitable for tilting type are of a special shape. Please contact us for details.
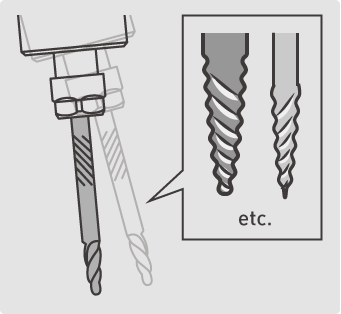
Summary of Automated Deburring by Float Deburring
Floating deburring is a machining method that aids in the automation and mechanization of deburring.
It may take some getting used to because the required know-how and tool behavior are different from those of normal cutting processes.
It is also necessary to select the tool, the number of revolutions and feed rate, the pressing pressure and offset amount, and whether it is for machining or robotic machining.
However, once you understand how to use the machine, you will be able to achieve the results you have imagined due to its simple mechanism.
Automate the deburring process with floating deburring to increase productivity and improve the work environment.
Do you have Trouble with Deburring Automation?
Sugino Machine Limited develops, manufactures, and sells tool holders and spindle motor units for deburring.
We will do our utmost to help improve productivity at manufacturing sites by utilizing our technical capabilities backed by many years of development of machine tools and tools, and our expertise in deburring automation.
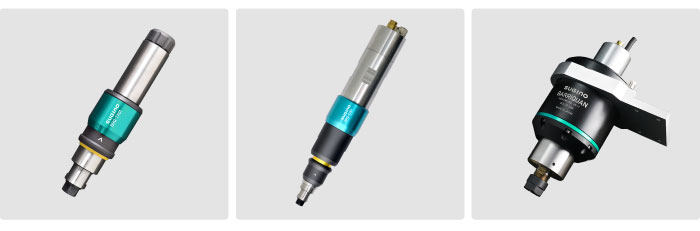