What is “SUPEROLL” processing?

What are “SUPEROLL” roller burnishing tools?
SUPEROLLs are roller burnishing tools that create smoother finishes by compressing machined peaks into machined valleys using precision rollers.
Machined surface undergoes plastic deformation as they are compressed with rollers resulting in smooth and seamless finishes. Productivity is improved, precision finishes are created, abrasion resistance is maximized, and part surfaces with improved fatigue strength are achieved.
Since parts can be given a precision finish easily and at low cost, SUPEROLLs are widely used worldwide for countless applications throughout the automotive industry, within the precision machinery market, chemical industry and parts manufactured for the home appliance markets.
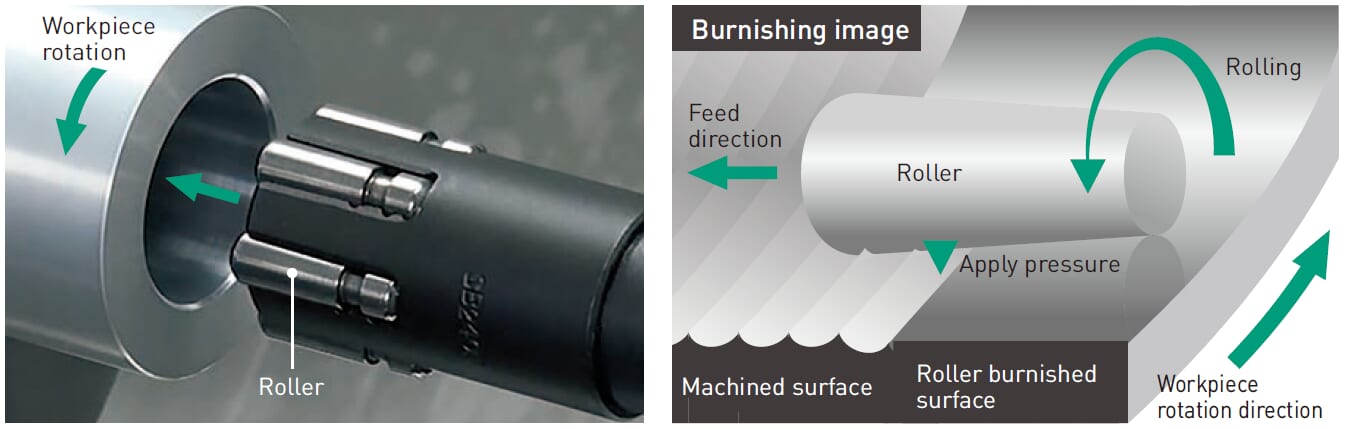
Principles of roller burnishing
Roller burnishing is a plastic processing method that allows hard and smooth rollers to contact the metal surface with compressed revolutions, and it finishes the surface layer by giving the surface layer a partial micro plastic deformation.
As the surface roughness is improved during a short time period, the surface hardens and produces the finished surface with increased durability because residual compressive stress is generated.
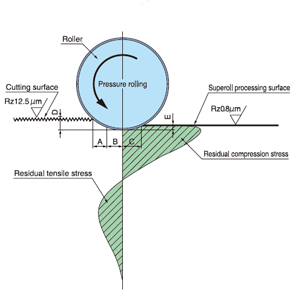
Figure 1 is a schematic showing this process method.
At transference area (A), the roller gradually pressurizes while contacting the cutting side of the surface, and when the contact pressure exceeds the yielding point of the material at transference area (B), a partial plastic deformation occurs.
After the maximum load is reached directly below the roller, elastic restoration starts at the smooth area (C), and the roller gradually separates from the processed surface.
During actual SUPEROLL processing, the series of movements explained above is repeated with multiple rollers, smoothing the processed surface.
Benefits of burnishing with SUPEROLL.
Smooth: Improve machined surface roughness by SUPEROLL.
Achieve Rz 0.1 – 0.8 μm finish in one pass.
The finished surface without any sharp projections is suitable for sliding and sealing surfaces.
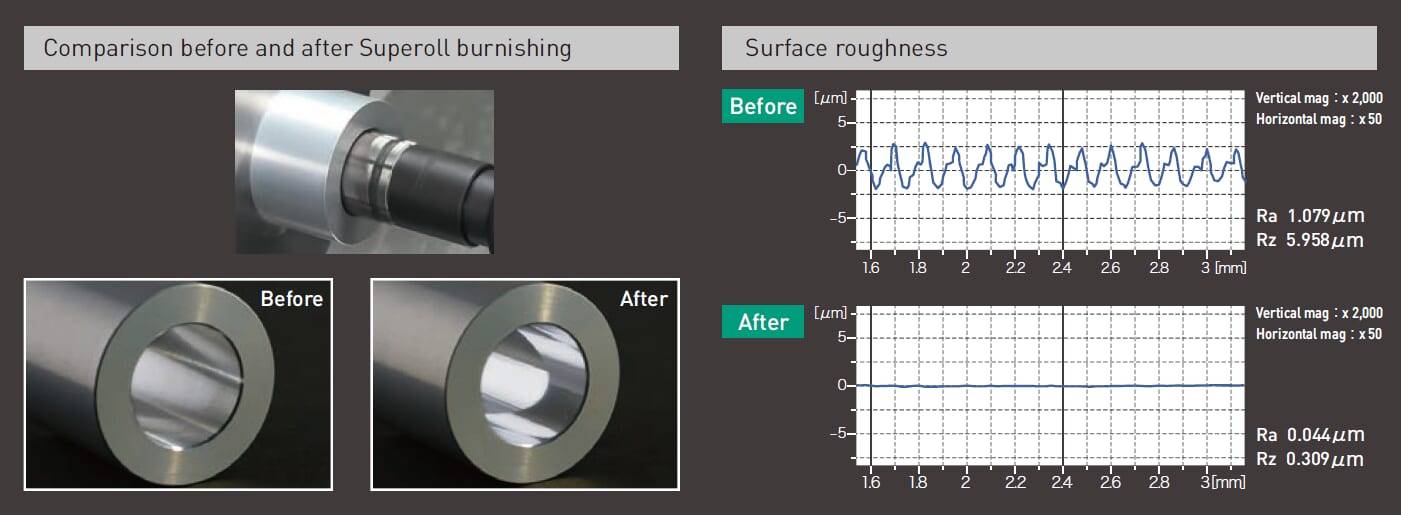
Achieve dimensional accuracy by machining, and improve surface roughness with SUPEROLL.
If it is difficult to achieve the required surface roughness while maintaining dimensional tolerance during machining,
Superoll can be used to easily improve the surface roughness. Using Superoll after the machining also
helps to extend the time (life time) to replace cutting tips relatively.
Improve roundness by using SUPEROLL to smooth out uneven surfaces.
Expand: Slight diameter sizing (in microns) without machining.
Smoothing out uneven workpiece surfaces allows dimensional amendment of several μm.
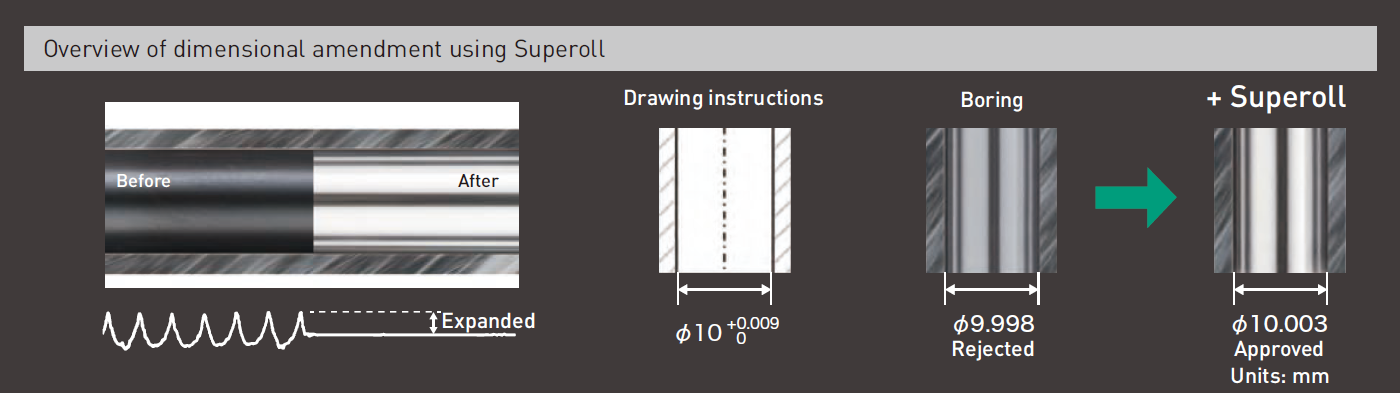
Increase yield with dimensional amendment using SUPEROLL!
Dimensional amendment by burnishing with SUPEROLL helps to reduce unnecessary time and cost for re-manufacturing units.
Increase strength: Increase endurance life of workpiece with SUPEROLL.
As residual stress in the compressive direction is induced at the surface, fatigue strength is increased by more than 30% using SUPEROLL tools.
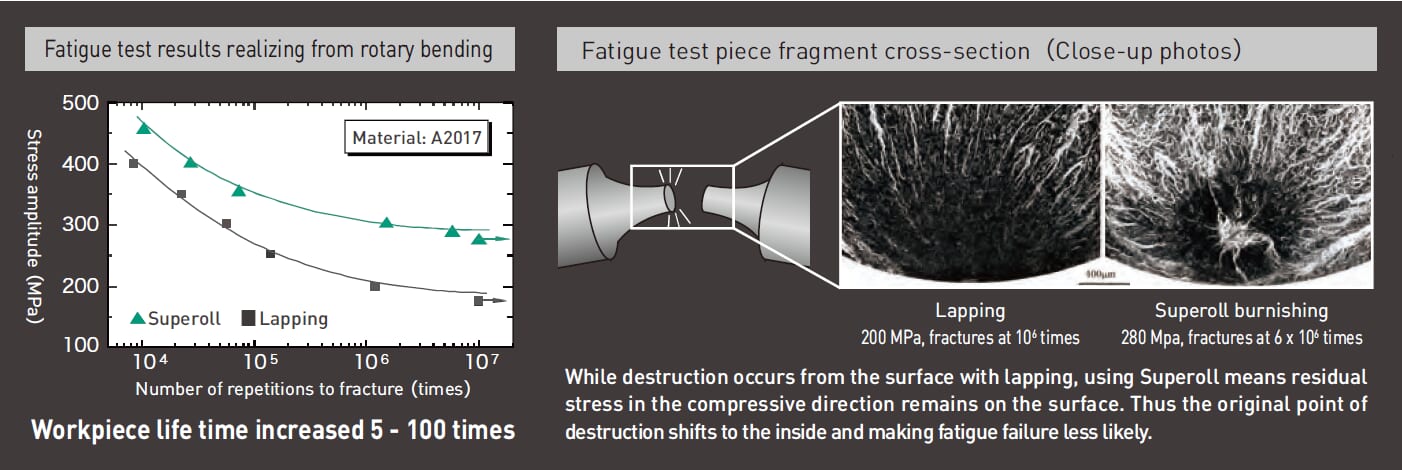
Improved fatigue strength.
Residual stress in the compressive direction can reach a deeper position than with shot peening, to help improve fatigue strength.
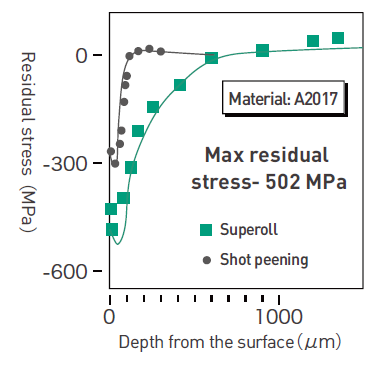
Increase hardness: Increase metal wear resistance by SUPEROLL.
Uneven metal surface is pressed evenly to harden the areas around the surface, increasing the surface hardness.
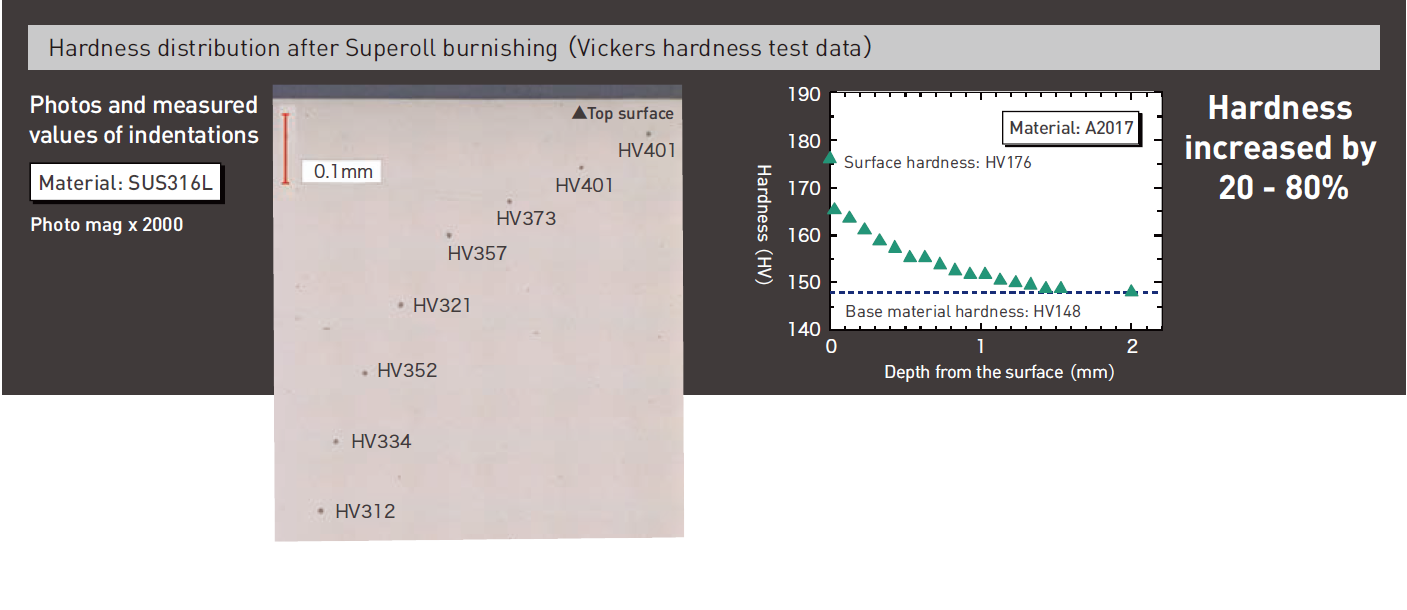
Increasing abrasion resistance.
Best-suited to finishing of sealing or sliding surfaces.