Self-Center SC-H30a : #30 Horizontal Compact Machining Center

SELF-CENTER SC-H30a
A high-rigidity horizontal machining center designed with the concept of reconciling both “long-duration unmanned operation” essential for mass production machining and “controlled deburring” critical for automated burr removal.
Product introduction video
Product introduction VR
Please view in full screen mode using the button at the bottom right of the screen.
1.Long-duration unmanned operation
More than 90% of brief machine stoppages are caused by chip-related issues.
Therefore, to achieve long-duration unmanned operation, it is important not to allow chips to accumulate in the machining workspace.”
The SC-H30a minimizes wiring and piping within the machining workspace and adopts a center trough with excellent chip evacuation. Additionally, it accommodates 71 tools and can be combined with an automatic transport system, enabling long-duration unmanned operation.
1.Complete separation of machine room and processing room.
- Reduced entry of chips and coolant into the drive unit.
- Prolonged lifespan of ball screws and guides.
- Improved maintenance
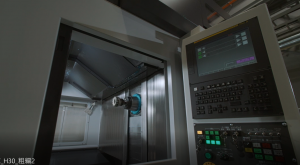
2.Center trough bed structure
Prevent chip accumulation and mitigate brief machine stoppage caused by cutting chips.
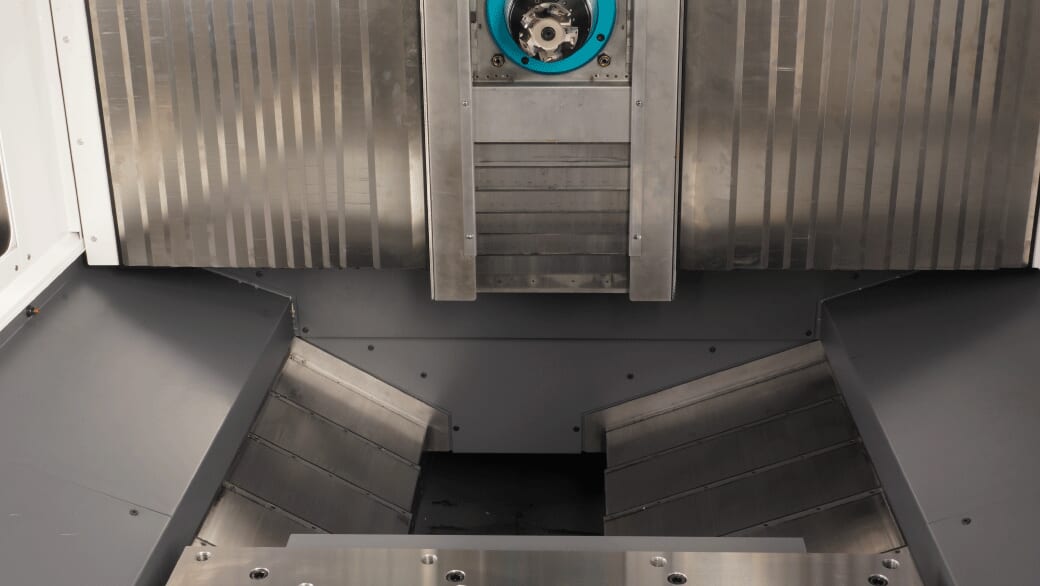
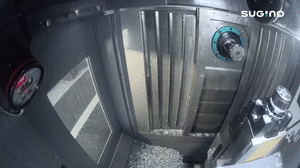
3.Exceptional chip-flow
Because of its horizontal design, chips do not accumulate on the workpiece or fixture; they fall directly and are discharged.
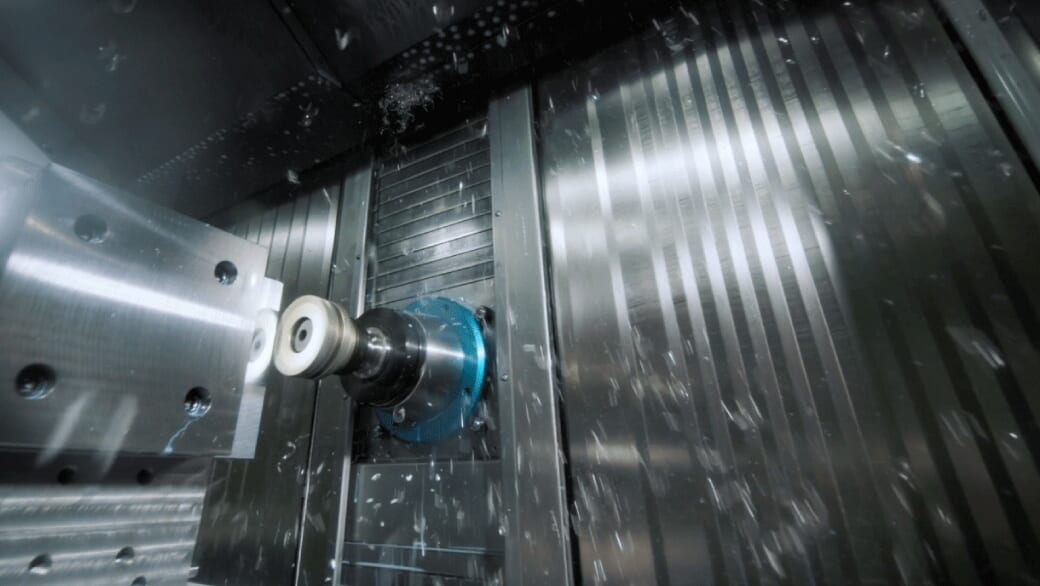
4. Combination with an automatic transport system
We offer a full range of automatic transport system
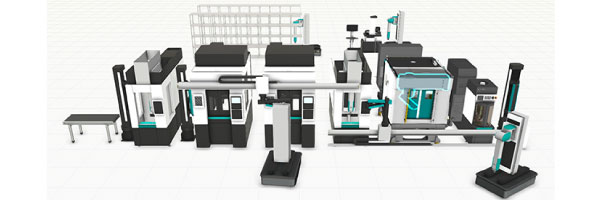
2.Precision deep hole machining
High-precision deep hole machining is achievable through the Z-axis table traverse method.
1. Z-axis table traverse with a stroke of 500mm
Due to the stationary main spindle, high straightness is achieved even in deep hole machining
2.Max. tool length: Max. 450mm
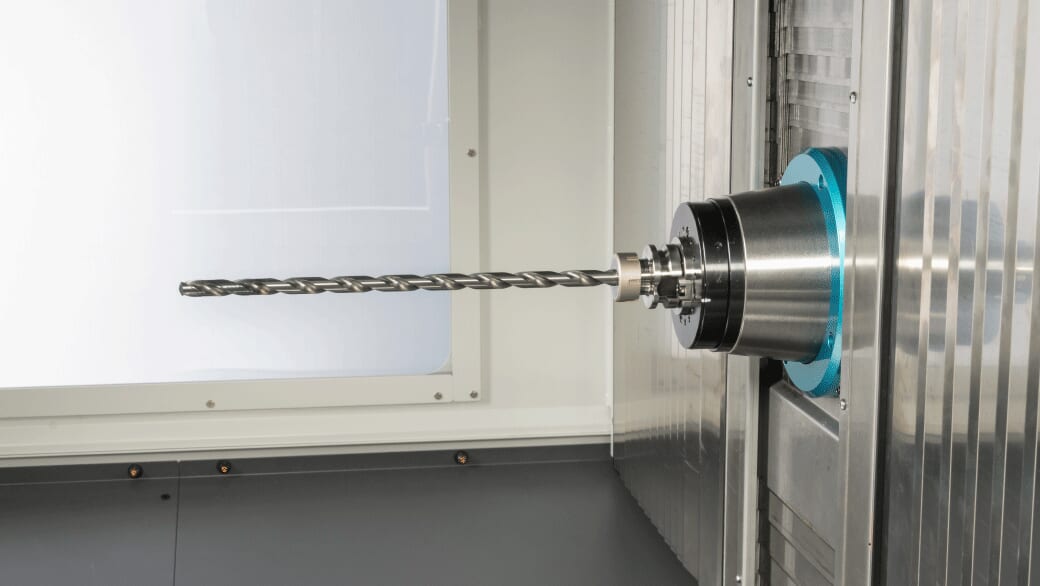
3.Burr control
Max. number of tools: 71 tools
To optimize tool life and control burr size, Sugino Machine proposes deburring control process.
1.Wide-variety compatibility ・・・ Reducing tool changeover time during setup.
2.Long-duration continuous operation ・・・Capable of setting up spare tools.
3.Burr Control ・・・Proper replacement of worn tools to control burrs.

Specification
Stroke | X-axis | mm | 500 (column traverse) |
---|---|---|---|
Y-axis | mm | 400 (column traverse) | |
Z-axis | mm | 500 (table traverse) | |
Spindle | Tool shank | – | BBT30 (Pull stud MAS-II (standard) |
Max. rotation speed | min-1 | 12000 (Standard) | |
Acceleration time to 10,000min-1 | sec. | 0.16 (Standard) | |
Max. tap rotation speed | min-1 | 8,000 | |
Feed | Rapid feed rate | m/min | 60 (X, Y, Z-axis) |
Cutting feed rate | m/min | Max. 30 | |
Acceleration and deceleration | 1.5 G (X, Y, Z-axis) | ||
Min. programmable Unit | mm | 0.001 | |
Accuracy | Positioning | mm | 0.004 (in full travel) |
Repeatability | mm | ±0.001 (all spindle) | |
ATC | Number of tools | – | 29 (optional 71) |
Tool to Tool | sec | 2.2 | |
Max. tool length | mm | 250/350 (option) / 450 (option) | |
Max. tool dimensions | mm | φ60 (with adjacent tool) | |
φ120 (No adjacent tool) | |||
Max. tool weight | kg | 2.0 (3.5 at low-speed ATC) | |
Tool selection | – | Memory random | |
Machine | Width × Length × Height | mm | 1,500 + 380 (operation panel) ×3,210×2,280 |
Weight | kg | 4,700 |