JCC-HM: Coolant Purification Unit
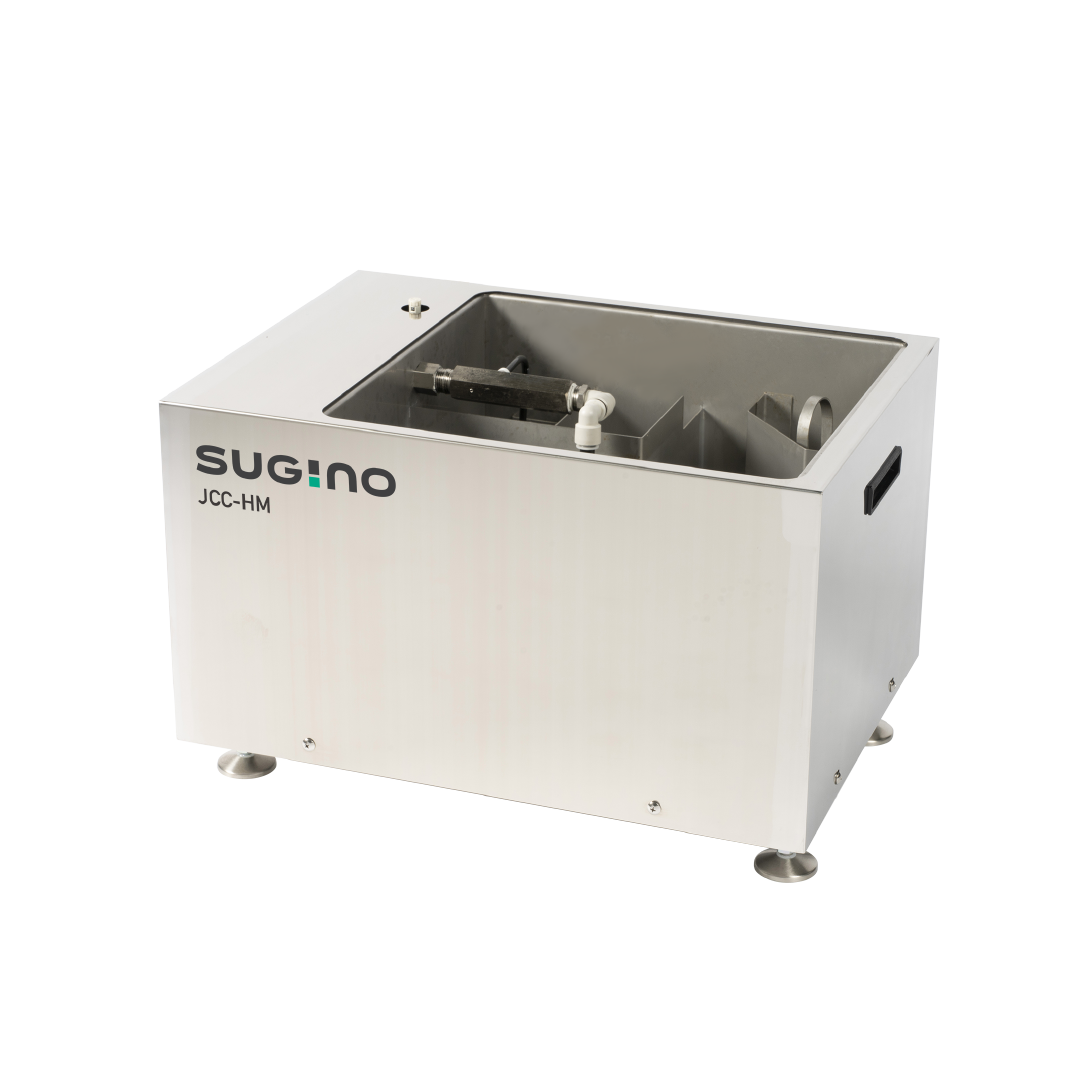
Coolant Purification Unit JCC-HM
JCC-HM is a unit which can use the power of micro bubbles to remove the fine contamination and oil in the liquid.
The only power required is air, no electricity is required. No consumables such as filters are required.
It widely includes water-soluble cleaning liquid and cutting oil.
The effect of removing foreign matter and oil in the liquid.
Longer fluid change cycle ・・・ Reduce fluid change cost !
Cleanliness of workpieces/improved processing accuracy ・・・ Quality improvement !
Longer service life of high-pressure pumps and coolant pumps ・・・Reduced maintenance costs !
Reduction of odors Reduce fluid change cost ・・・ Better work environment !
Comparison with Before/After process (grinding fluid)
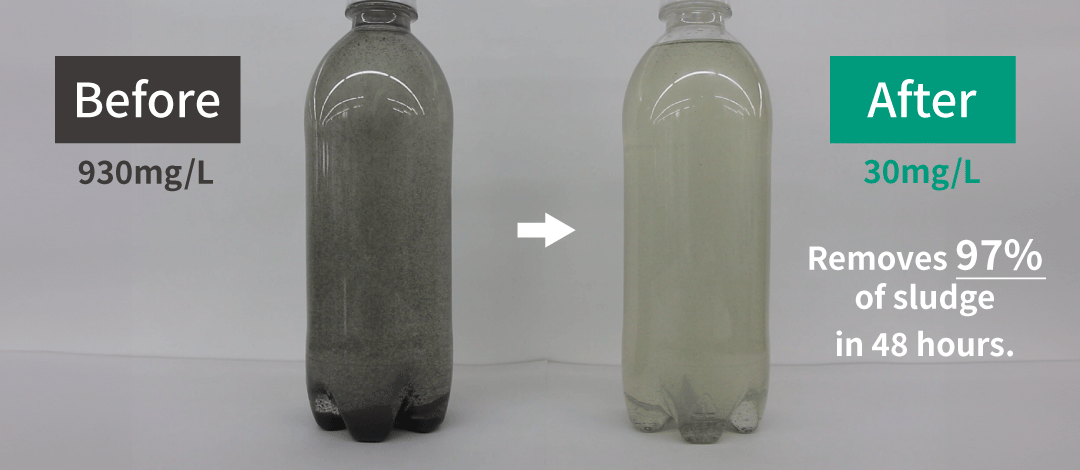
Introduction video
Principle and Features for JCC-HM
How it works

Features
① Clean used liquids with micro bubbles.
Micro bubbles attach to the contamination in the liquid (such as oils and foreign matter) and float to the surface, thereby purifying the liquid.
② The Dirt can be separated quickly and cleanly with the unique internal structure.
Contamination and oil is attached in coalescer so that dirt can be separated quickly. With its unique flow path structure, it separates dirt, prevents their re-mixing, and reduces the amount of waste liquid.
Additionally, the components of the processing tank are detachable, making cleaning easy.
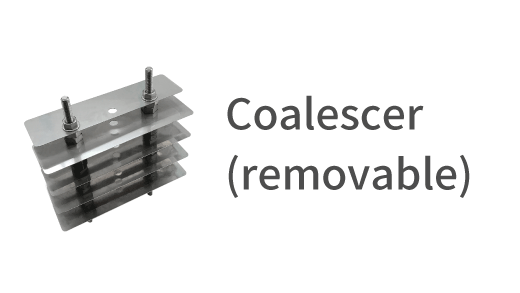
③ Air is the only power source needed!
Requires only air power for easy installation and immediate operation.
And No filter is required.
All you have to do is connect two hoses (dirty water IN/purified water OUT) and air.
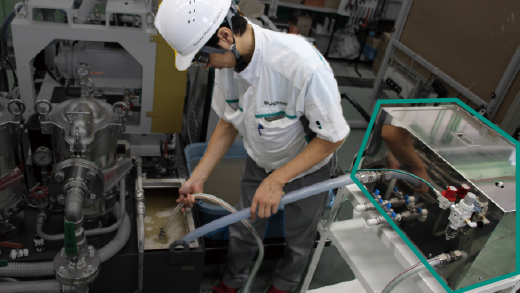
Flexible installation location!
The JCC-HM is compact and can be installed in available spaces, such as on top of tanks.
Regardless of installation locations, you can choose a model that suits your equipment and environment.
Comparison with other methods
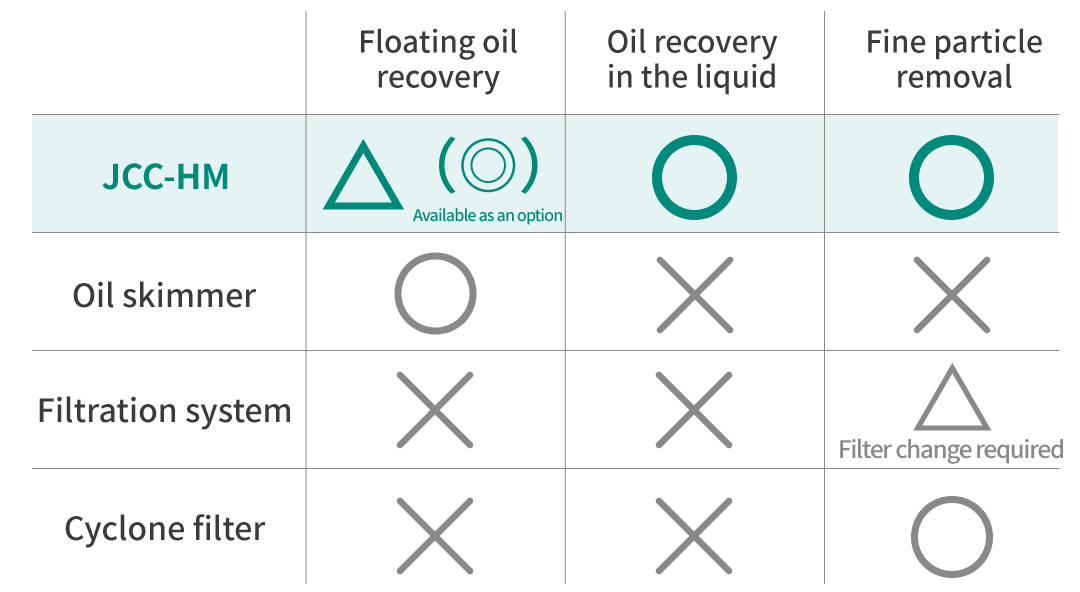
The mechanism that makes a difference is…
The JCC-HM uses microbubbles, with diameters as small as 1 to 100 µm, to lift and remove oils and contaminants from cutting fluids and cleaning liquids.
No consumables, such as filters, are required, making it an environmentally friendly processing method.
Specification / Option
Specification
Model | JCC-HM2 |
---|---|
Throughput | 13L/min (air pressure 0.15MPa) |
Air consumption | 40L/min (air pressure 圧0.15MPa) |
Noise | Under 70dB(A) (equivalent noise) |
Liquid temperature | Max.50℃ |
Utility | Compressed air *No power supply required |
Size | W550 × D390 × H370 mm |
Weight | 35kg |
Tank capacity | 25L |
Remarks | Not applicable to oil-based liquids |
Option
Dedicated cart for JCC-HM2
Enhanced wear resistance specification
Enhanced alkaline resistance specification
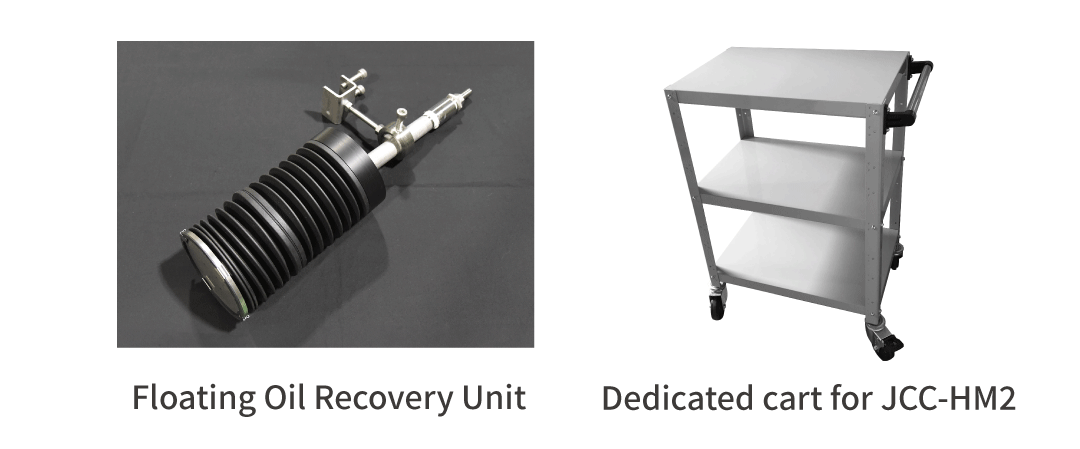