Various types of chambers for “STAR BURST”
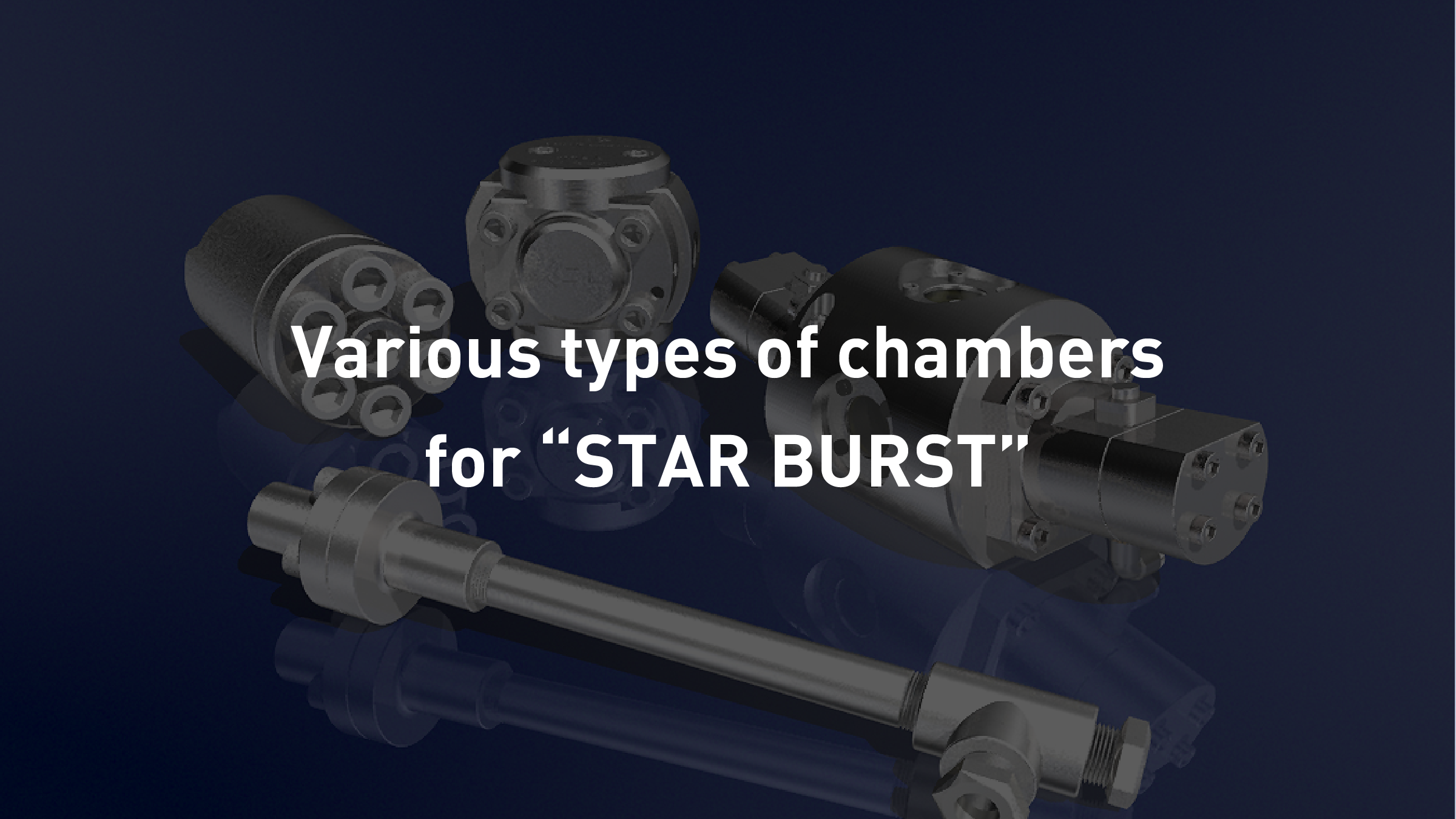
In addition to the standard oblique collision chamber other unique types of chambers are interchangeable with Star Burst 10 or Star Burst 100.
Oblique-type collision chamber
Pressurized raw materials collide with each other at an oblique angle, pulverizing the sample. This is the standard-type collision chamber, which achieves minimum contamination.
Applications: Dispersing, Pulverizing, Emulsifying, and Surface Reforming
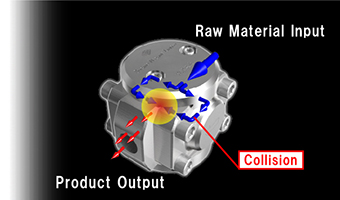
Ball type chamber
Pressurized raw material particles collide with a decentered ceramic ball.
Larger particles are effectively dispersed and homogenized preventing clogging of the nozzles.
Applications: Dispersing, Pulverizing, and Emulsifying
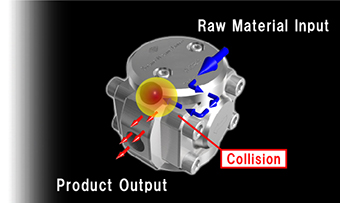
Separate type chamber
Highly concentrated raw material slurry is aspirated by injecting solvent at very high pressure. After the mixing of the particles in the pressurized solvent, the particles undergo an oblique collision thereby evenly dispersing them. This special type of chamber can be used for high-density particles or malleable particles such as nickel metal.
Applications: Dispersing, Pulverizing
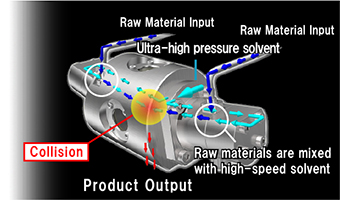
Single nozzle chamber
Raw materials are pulverized and dispersed with a cavitation effect generated by the injection of pressurized raw material slurry.
Layered clay minerals, such as mica or bentonite, can be effectively cleaved.
Applications: Dispersing, Cleaving, and Surface reforming
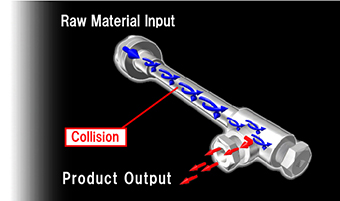
Slit chamber
Raw materials are emulsified and dispersed by compression turbulence and shear as pressurized raw materials pass through a narrow slit.
Strong shearing force accelerates the emulsification through the narrow slit. This slit chamber is used especially in materials for the Cosmetics, Foods and Pharmaceuticals Industries.
Application: Emulsification
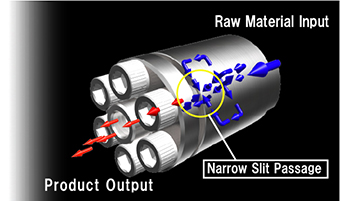
Circulation cooling type chamber
Uniquely developed chamber with circulation cooling system can reduce the temperature increase during the micronizing process of high-pressure homogenization, that enables to use low boiling point organic solvent. The temperature increase is sometimes a disadvantage of the high-pressure homogenizer, but this unique chamber achieves approximately half of the delta temperature compared with the standard chamber on the pressure condition of 245 MPa. It also helps to prevent some deterioration or chemical reactions caused by the temperature increase.